Pyrolysis is a thermochemical process that decomposes organic materials at high temperatures in the absence of oxygen. It is used to convert biomass, plastics, and other carbon-based materials into valuable products such as bio-oil, syngas, and bio-char. The process involves heating the material in a reactor, causing its chemical bonds to break down into smaller molecules. Pyrolysis is energy-intensive and requires precise control of temperature and pressure to optimize product yields. It is widely applied in waste management, biofuel production, and chemical manufacturing, offering a sustainable way to reduce waste and generate useful outputs.
Key Points Explained:
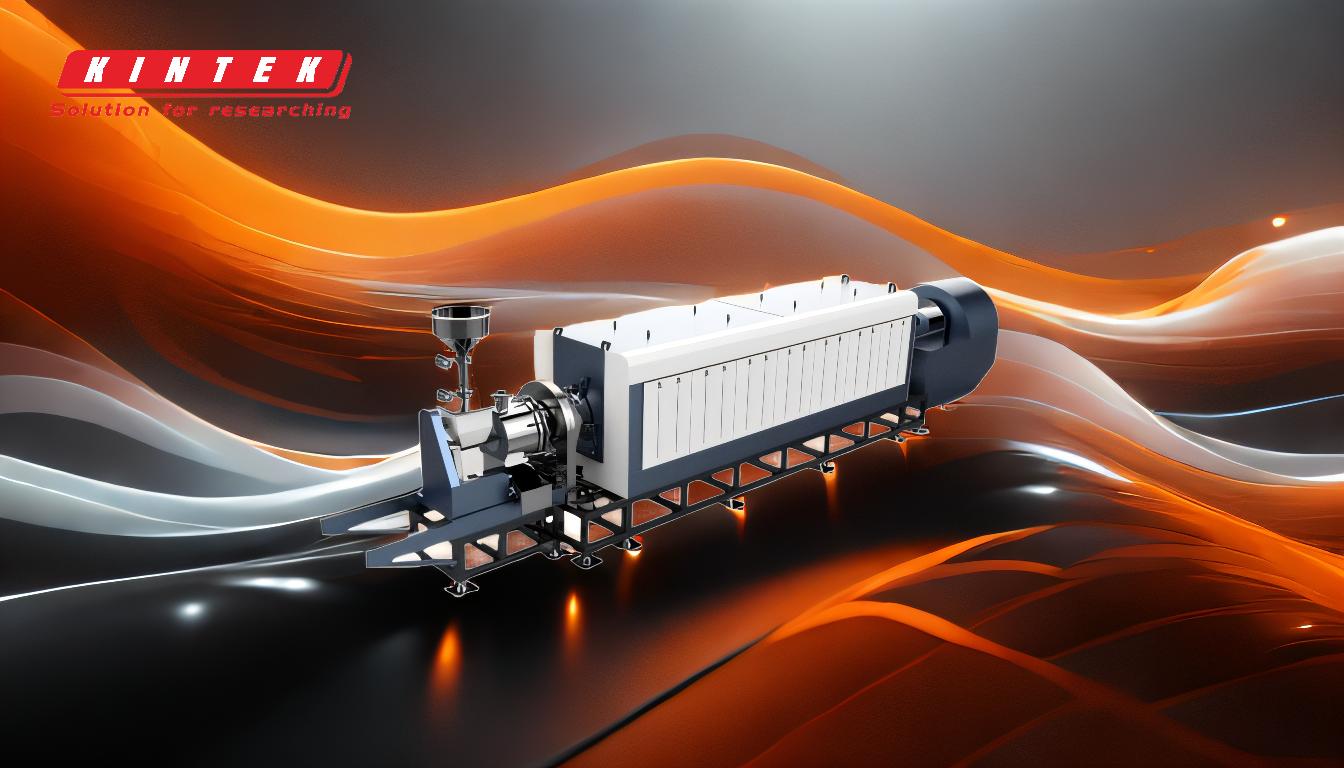
-
Definition of Pyrolysis:
- Pyrolysis is a thermochemical decomposition process that occurs when organic materials are heated in the absence of oxygen.
- The term "pyrolysis" comes from the Greek words "pyro" (fire) and "lysis" (separating), reflecting its nature of breaking down materials through heat.
-
How Pyrolysis Works:
- The process involves feeding organic waste into a reactor where it is exposed to controlled high temperatures, typically above 430 °C (800 °F).
- In the absence of oxygen, the material's chemical bonds break down, leading to the formation of smaller molecules.
- The process generates three main products:
- Gases (Syngas): A mixture of hydrogen, carbon monoxide, and other gases.
- Liquids (Bio-oil or Pyrolysis Oil): A liquid fuel or chemical precursor.
- Solids (Bio-char): A carbon-rich solid residue.
-
Key Conditions for Pyrolysis:
- Temperature: Pyrolysis typically occurs at high temperatures, ranging from 430 °C to over 800 °C, depending on the material and desired products.
- Oxygen-Free Environment: The absence of oxygen prevents combustion and ensures the material decomposes rather than burns.
- Pressure: The process may occur under pressure to optimize the breakdown of materials and product yields.
-
Applications of Pyrolysis:
- Biomass Conversion: Pyrolysis is used to convert biomass into biofuels, such as bio-oil, which can be refined into drop-in hydrocarbon fuels or oxygenated additives.
- Waste Management: It is applied to process plastics, tires, and other waste materials, reducing landfill use and generating valuable byproducts.
- Chemical Production: Pyrolysis can produce petrochemical replacements and other industrial chemicals.
-
Advantages of Pyrolysis:
- Waste Reduction: It provides a sustainable way to manage organic waste by converting it into useful products.
- Energy Recovery: The process generates syngas and bio-oil, which can be used as energy sources.
- Carbon Sequestration: Bio-char produced during pyrolysis can be used as a soil amendment, helping to sequester carbon and improve soil health.
-
Challenges and Limitations:
- Energy-Intensive: Pyrolysis requires significant energy input to maintain high temperatures and controlled conditions.
- Process Complexity: Optimizing the process for specific materials and desired outputs can be technically challenging.
- Byproduct Management: The handling and utilization of syngas, bio-oil, and bio-char require additional processing and infrastructure.
-
Comparison to Other Processes:
- Thermal Cracking: Pyrolysis is similar to thermal cracking used in petroleum refining but operates at lower temperatures and without oxygen.
- Combustion and Gasification: Unlike combustion, which requires oxygen and produces heat, and gasification, which uses limited oxygen to produce syngas, pyrolysis occurs in a completely oxygen-free environment.
-
Future Prospects:
- Pyrolysis is a promising technology for sustainable waste management and renewable energy production.
- Advances in reactor design, process optimization, and byproduct utilization are expected to enhance its efficiency and economic viability.
In summary, pyrolysis is a versatile and valuable process for converting organic materials into useful products. While it presents challenges, its potential for waste reduction, energy recovery, and sustainable chemical production makes it a key technology for the future.
Summary Table:
Aspect | Details |
---|---|
Definition | Thermochemical decomposition of organic materials in the absence of oxygen. |
Process | Heating materials above 430°C to break chemical bonds, producing syngas, bio-oil, and bio-char. |
Key Conditions | High temperature (430°C–800°C), oxygen-free environment, and controlled pressure. |
Applications | Biomass conversion, waste management, and chemical production. |
Advantages | Waste reduction, energy recovery, and carbon sequestration. |
Challenges | Energy-intensive, process complexity, and byproduct management. |
Future Prospects | Enhanced reactor design and process optimization for greater efficiency. |
Ready to explore pyrolysis solutions for your waste management needs? Contact us today for expert guidance!