Refractory in a rotary kiln is a specialized material used to insulate and protect the kiln shell from the extreme internal temperatures generated during operation. It plays a critical role in maintaining the kiln's efficiency by minimizing heat loss and ensuring consistent internal temperatures. Refractory linings are essential for direct-fired rotary kilns, where they protect the shell from high temperatures and abrasion. The choice of refractory material depends on factors such as kiln temperature, material chemistry, and abrasiveness. In contrast, refractory is not used in indirect-fired kilns, as it would reduce efficiency by adding an extra layer for heat to pass through. Proper maintenance of the refractory lining is crucial to avoid process inconsistencies, heat distortion, and costly repairs.
Key Points Explained:
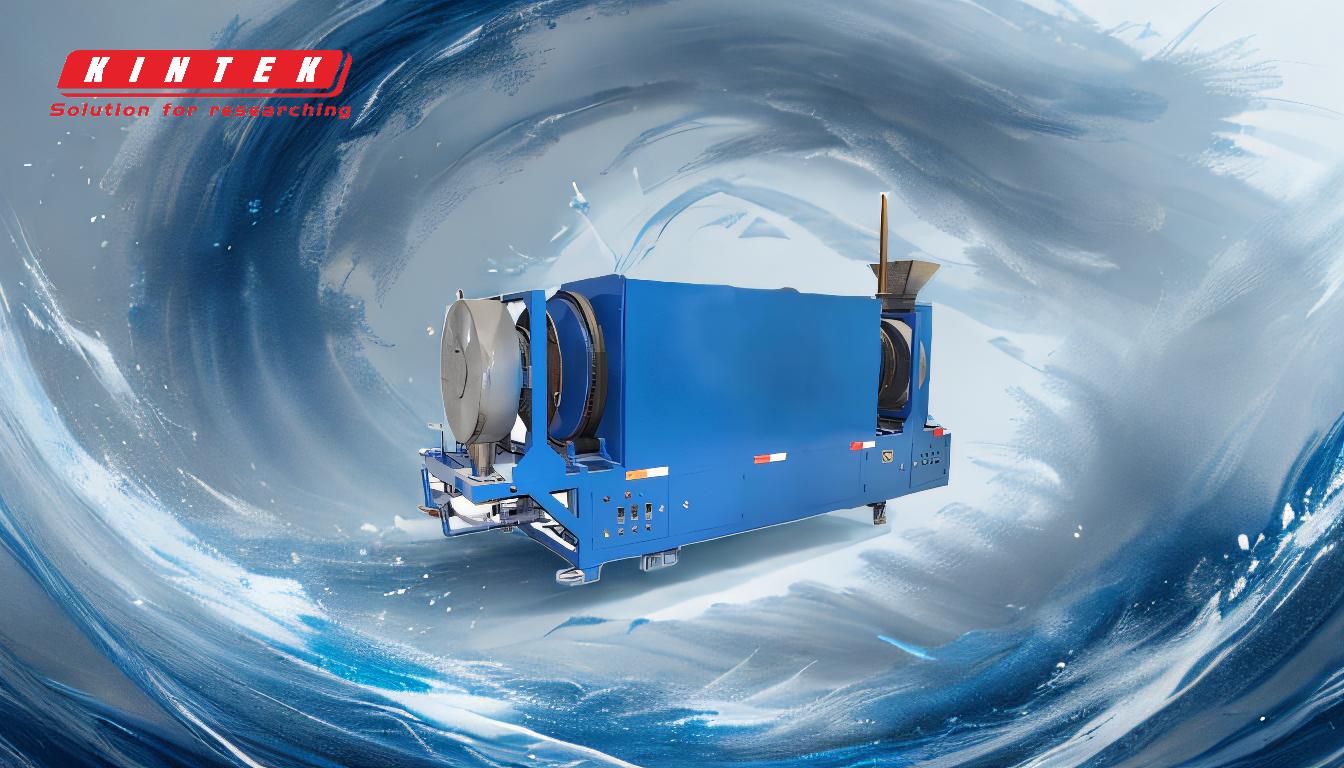
-
Purpose of Refractory in Rotary Kilns:
- Refractory materials serve two primary purposes in rotary kilns:
- Insulation: They help retain heat within the kiln, ensuring efficient operation and minimizing heat loss to the external environment.
- Protection: They shield the kiln shell from the extreme internal temperatures, which can otherwise cause distortion or damage to the drum shell.
- Refractory materials serve two primary purposes in rotary kilns:
-
Types of Refractory Materials:
- Refractory materials are customized based on the specific application and operating conditions of the kiln. The choice of refractory depends on factors such as:
- Kiln Temperature: Different refractory materials have varying temperature tolerances.
- Material Chemistry: The chemical composition of the materials being processed can affect the choice of refractory.
- Abrasiveness: The level of abrasion caused by the materials inside the kiln influences the selection of refractory.
- Refractory materials are customized based on the specific application and operating conditions of the kiln. The choice of refractory depends on factors such as:
-
Application in Direct-Fired vs. Indirect-Fired Kilns:
- Direct-Fired Kilns: Refractory is a critical component in direct-fired rotary kilns, where it protects the kiln shell and helps retain heat.
- Indirect-Fired Kilns: Refractory is not used in indirect-fired kilns because it would reduce efficiency by adding an extra layer for heat to pass through.
-
Importance of Refractory Lining Maintenance:
- The refractory lining is crucial for maintaining the desired internal temperature and ensuring efficient operation.
- Degradation or damage to the refractory lining can lead to:
- Process Inconsistencies: Variations in temperature can affect the quality of the materials being processed.
- Heat Distortion: Damage to the kiln shell can occur if the refractory lining fails.
- Costly Repairs: Replacing or repairing the refractory lining is expensive and can lead to significant downtime.
-
Impact on Kiln Efficiency:
- Properly functioning refractory lining ensures that the kiln operates at optimal efficiency by:
- Retaining heat within the kiln.
- Protecting the kiln shell from damage.
- Maintaining consistent internal temperatures, which is essential for the quality of the materials being processed.
- Properly functioning refractory lining ensures that the kiln operates at optimal efficiency by:
-
Customization of Refractory Layers:
- Refractory layers can be customized to suit specific applications, ensuring that the kiln operates efficiently and safely under various conditions. This customization involves selecting the appropriate material and thickness based on the operating parameters of the kiln.
By understanding these key points, equipment and consumable purchasers can make informed decisions about the selection and maintenance of refractory materials in rotary kilns, ensuring optimal performance and longevity of the equipment.
Summary Table:
Key Aspect | Details |
---|---|
Purpose | Insulation and protection of the kiln shell. |
Material Selection Factors | Kiln temperature, material chemistry, and abrasiveness. |
Direct-Fired Kilns | Refractory is essential for heat retention and shell protection. |
Indirect-Fired Kilns | Refractory is not used to avoid efficiency loss. |
Maintenance Importance | Prevents process inconsistencies, heat distortion, and costly repairs. |
Impact on Efficiency | Ensures heat retention, shell protection, and consistent temperatures. |
Customization | Tailored to specific applications for optimal performance. |
Need expert advice on refractory materials for your rotary kiln? Contact us today for tailored solutions!