A resistance heating furnace is a type of industrial furnace that uses electric current to generate heat, either directly by passing current through the material being heated or indirectly by heating elements or conductive media. This method of heating is widely used in various industries, including ceramics, metallurgy, electronics, and chemical processing, due to its precise temperature control and efficiency. Unlike other heating methods, such as induction or arc heating, resistance heating relies on the electrical resistance of materials to produce heat, making it versatile for applications ranging from material treatment to high-temperature experiments.
Key Points Explained:
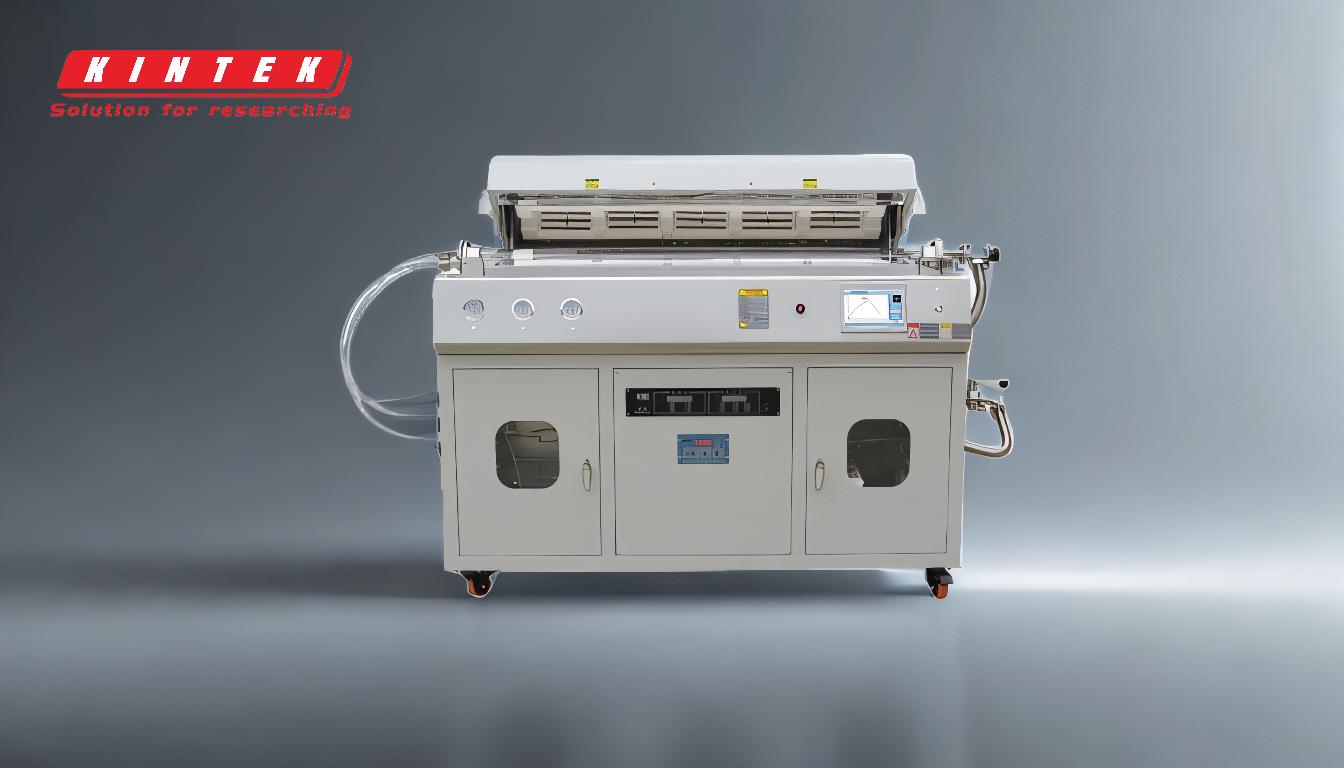
-
Definition and Working Principle:
- A resistance heating furnace operates by passing an electric current through a material or heating element, which generates heat due to the material's electrical resistance. This heat is then transferred to the workpiece or material being processed.
- It can function in two primary modes:
- Direct Heating: The electric current passes directly through the material, heating it internally.
- Indirect Heating: The current heats a separate heating element or conductive medium, which then transfers heat to the material via conduction, convection, or radiation.
-
Types of Resistance Heating Furnaces:
- Graphite Resistance Furnace: This type uses a graphite resistor, which has excellent electrical conductivity and high-temperature resistance. The graphite resistor is heated by passing an electric current through it, creating a high-temperature environment suitable for processes like graphitization.
- Vertical Tube Furnace: Utilizes resistive heating elements surrounding a tube to heat the interior. This design is ideal for precise temperature control in research and industrial applications, such as material testing and sintering.
- Other Variants: Resistance furnaces can also include box furnaces, muffle furnaces, and continuous furnaces, each tailored for specific industrial needs.
-
Applications:
- Resistance heating furnaces are widely used in industries such as ceramics, metallurgy, electronics, glass, chemicals, and materials science. They are employed for processes like:
- Powder roasting
- Ceramic sintering
- High-temperature experiments
- Material treatment (e.g., annealing, tempering)
- High-temperature atmosphere sintering
- Flue gas treatment
- Resistance heating furnaces are widely used in industries such as ceramics, metallurgy, electronics, glass, chemicals, and materials science. They are employed for processes like:
-
Advantages:
- Precise Temperature Control: Resistance heating allows for accurate regulation of temperature, making it suitable for processes requiring specific thermal profiles.
- Efficiency: The direct conversion of electrical energy into heat minimizes energy loss.
- Clean Heating: Unlike combustion-based heating, resistance heating does not produce harmful byproducts, making it environmentally friendly.
- Versatility: Can be used for a wide range of materials and processes, from small-scale laboratory experiments to large-scale industrial production.
-
Comparison with Other Heating Methods:
- Induction Heating: Induction furnaces generate heat within the material itself using electromagnetic induction, making them ideal for melting metals. However, resistance heating is more versatile for non-metallic materials and processes requiring uniform heating.
- Arc Heating: Electric arc furnaces are primarily used for metal smelting and rely on an electric arc to generate heat. Resistance furnaces, on the other hand, are more controlled and suitable for precision applications.
-
Key Components:
- Heating Elements: Typically made of materials like graphite, silicon carbide, or metal alloys, these elements are designed to withstand high temperatures and provide consistent heat.
- Insulation: High-quality insulation is essential to minimize heat loss and improve energy efficiency.
- Control Systems: Advanced temperature control systems ensure precise regulation of heating cycles, which is critical for processes like sintering and annealing.
-
Material Considerations:
- The choice of heating elements and furnace design depends on the material being processed. For example, graphite is preferred for high-temperature applications due to its thermal stability and conductivity, while metal alloys are used for lower-temperature processes.
In summary, resistance heating furnaces are a cornerstone of modern industrial and scientific processes, offering precise, efficient, and versatile heating solutions. Their ability to handle a wide range of materials and applications makes them indispensable in fields ranging from materials science to manufacturing.
Summary Table:
Aspect | Details |
---|---|
Definition | Uses electric current to generate heat through material resistance. |
Types | Graphite resistance, vertical tube, box, muffle, and continuous furnaces. |
Applications | Ceramics, metallurgy, electronics, material treatment, high-temperature experiments. |
Advantages | Precise temperature control, energy efficiency, clean heating, versatility. |
Key Components | Heating elements, insulation, advanced control systems. |
Looking for a reliable resistance heating furnace? Contact us today to find the perfect solution for your needs!