Injection capacity, also known as shot capacity, refers to the maximum volume or weight of material that an injection molding machine's screw can inject in a single operation cycle. This parameter is critical for determining the machine's suitability for producing specific parts, as it directly impacts the size and weight of the components that can be manufactured. Understanding shot capacity helps equipment purchasers select the right machine for their production needs, ensuring efficiency and quality in the molding process.
Key Points Explained:
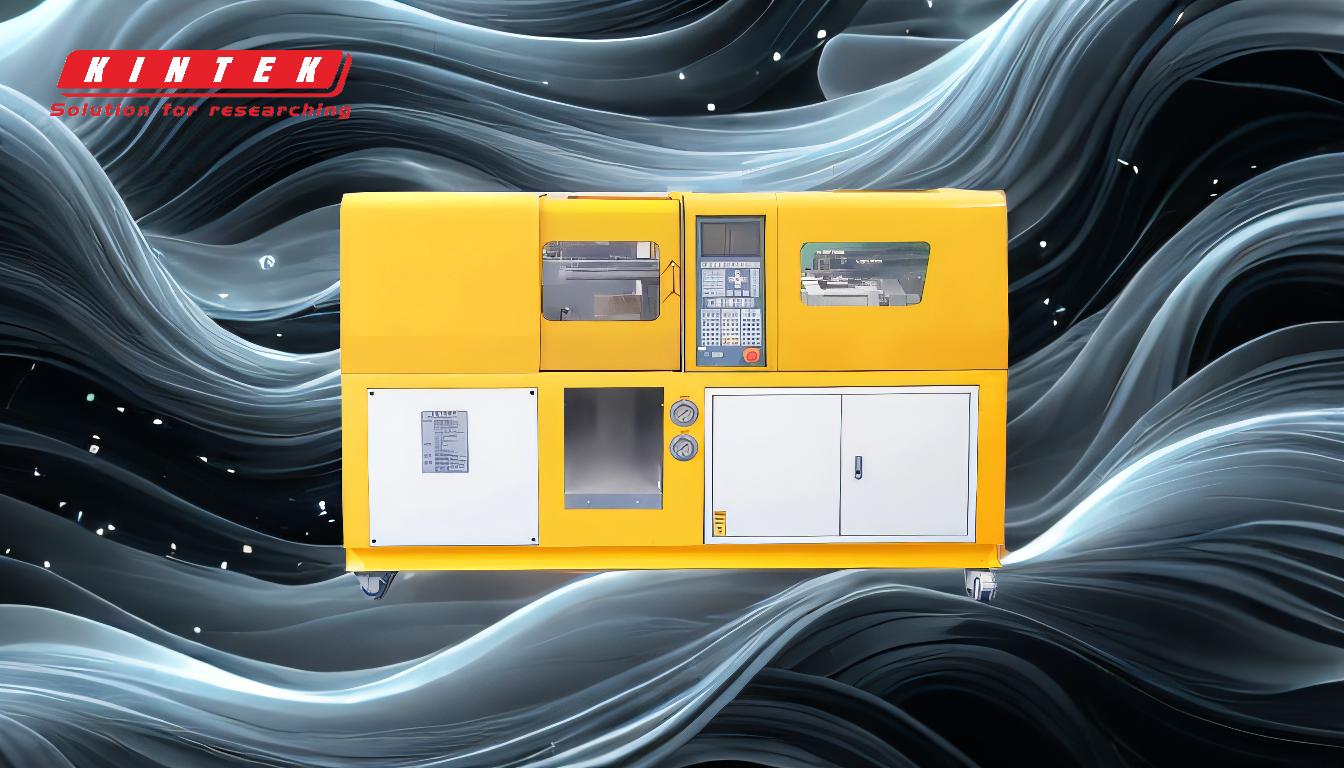
-
Definition of Shot Capacity
- Shot capacity is the maximum volume or weight of material that the screw of an injection molding machine can inject in one cycle.
- It is a key specification that defines the machine's ability to produce parts of a certain size and weight.
-
Importance of Shot Capacity
- Part Size and Weight: Determines the maximum size and weight of the parts that can be produced.
- Material Efficiency: Ensures the machine can handle the required amount of material without underfilling or overfilling the press mold.
- Production Suitability: Helps in selecting the right machine for specific applications, avoiding inefficiencies or limitations in production.
-
Factors Influencing Shot Capacity
- Screw Diameter: Larger screws can inject more material per cycle.
- Screw Stroke Length: Longer strokes allow for greater material displacement.
- Material Density: Different materials have varying densities, affecting the weight of the shot.
- Machine Specifications: The design and capabilities of the injection molding machine itself play a significant role.
-
How Shot Capacity is Measured
- Shot capacity is typically measured in grams (weight) or cubic centimeters (volume).
- The measurement is often based on polystyrene, a common reference material with a known density.
- For other materials, the shot capacity may need to be adjusted based on their specific density.
-
Practical Considerations for Purchasers
- Matching Shot Capacity to Production Needs: Ensure the machine's shot capacity aligns with the size and weight of the parts being produced.
- Future-Proofing: Consider potential future projects that may require larger or heavier parts.
- Material Compatibility: Verify that the machine can handle the specific materials used in production.
-
Common Misconceptions
- Shot capacity is not the same as the clamping force of the machine, which is a separate specification.
- It is not a fixed value for all materials; it varies based on the density of the material being used.
-
Example Calculation
- If a machine has a shot capacity of 200 grams for polystyrene (density: 1.05 g/cm³), the volume capacity would be approximately 190 cm³.
- For a denser material like polycarbonate (density: 1.2 g/cm³), the weight capacity would decrease to around 167 grams for the same volume.
By understanding shot capacity, equipment and consumable purchasers can make informed decisions, ensuring that the selected injection molding machine meets their production requirements while optimizing efficiency and cost-effectiveness.
Summary Table:
Aspect | Details |
---|---|
Definition | Maximum volume or weight of material injected in one cycle. |
Importance | Determines part size, weight, and material efficiency. |
Factors Influencing | Screw diameter, stroke length, material density, and machine specifications. |
Measurement | Typically in grams (weight) or cubic centimeters (volume). |
Practical Considerations | Match capacity to production needs, future-proofing, and material compatibility. |
Common Misconceptions | Not the same as clamping force; varies by material density. |
Need help selecting the right injection molding machine? Contact our experts today for tailored advice!