Sintering in a muffle furnace is a thermal process used to compact and form solid materials by applying heat without reaching the material's melting point. This process is widely used in industries such as ceramics, metallurgy, and powder metallurgy to create dense, durable products with specific mechanical and physical properties. The sintering process involves several key steps, including material preparation, heating, and controlled cooling, all of which are carefully managed within the furnace to ensure the desired outcome. The muffle furnace provides a controlled environment, allowing precise regulation of temperature and atmosphere, which are critical for successful sintering.
Key Points Explained:
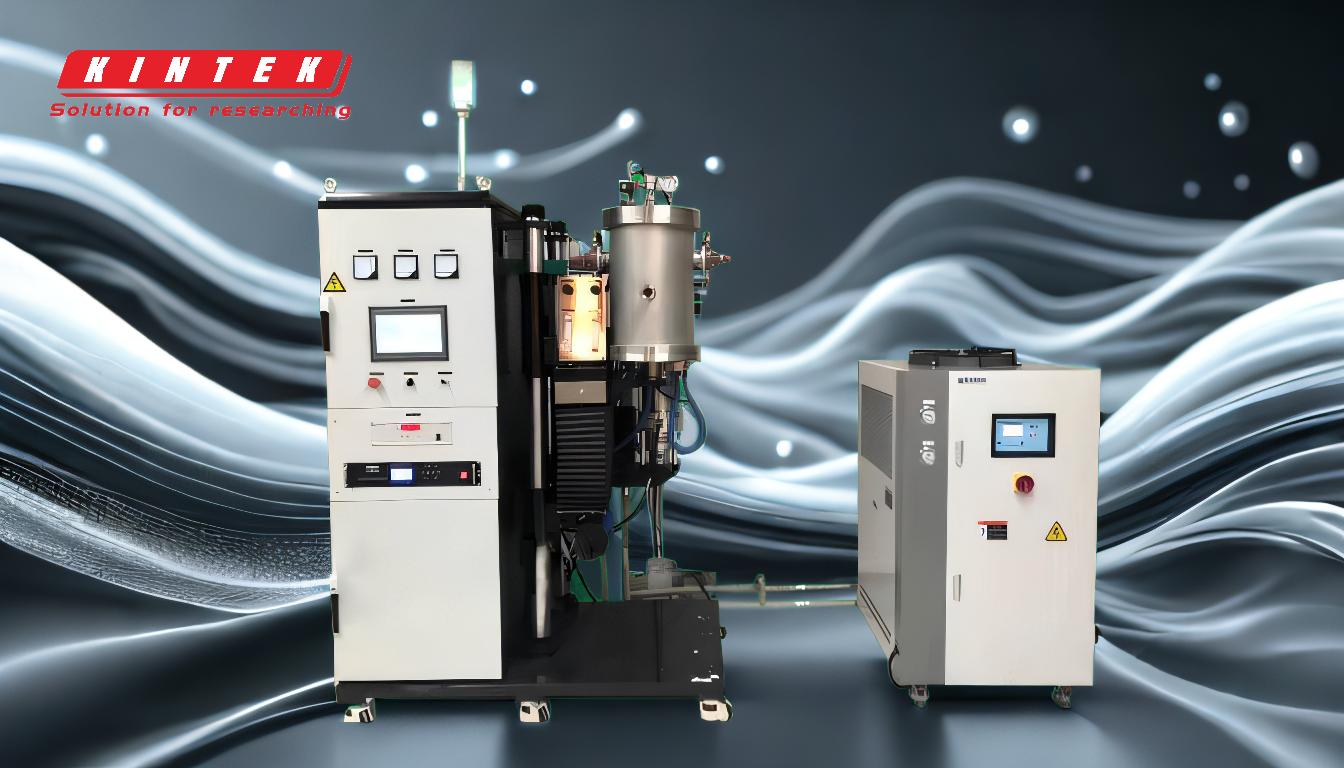
-
Definition of Sintering in a Muffle Furnace:
- Sintering is a process that compacts and forms a solid mass of material by applying heat or pressure without melting the material to the point of liquefaction.
- In a muffle furnace, this process is carried out in a controlled environment, where the temperature and atmosphere are precisely regulated to achieve the desired material properties.
-
Key Steps in the Sintering Process:
- Material Preparation: The process begins with the preparation of the powder compact. This involves mixing primary materials, binders, and other additives to form a homogeneous mixture. The mixture is then pressed into the desired shape using methods such as cold pressing or 3D printing.
- Heating and Consolidation: The shaped material, known as the green body, is placed in the muffle furnace. The furnace is heated to a temperature just below the material's melting point. During this stage, the particles in the material begin to diffuse across their boundaries, fusing together to form a denser, more cohesive structure.
- Particle Merging: As the temperature increases, the particles densify and merge. This process can be accelerated using techniques such as liquid phase sintering (LPS), where a small amount of liquid phase is introduced to facilitate particle bonding.
- Solidification: After the sintering process is complete, the material is allowed to cool slowly within the furnace. This controlled cooling helps to prevent cracking and ensures that the material solidifies into a unified mass with the desired mechanical properties.
-
Role of the Muffle Furnase:
- Temperature Control: The muffle furnace allows for precise control of the heating and cooling rates, which are critical for achieving the desired material properties. The furnace is typically equipped with resistance heating elements or induction heating systems that generate and maintain the required temperatures.
- Atmosphere Control: The furnace can be operated in various atmospheres, including inert gases, reducing atmospheres, or vacuum, depending on the material being sintered. This control over the atmosphere helps to prevent oxidation, reduce surface oxides, and remove any binders or lubricants used during the material preparation stage.
-
Applications of Sintering in a Muffle Furnace:
- Ceramics: Sintering is widely used in the production of ceramic materials, where it helps to fuse ceramic particles into a dense, durable product. The muffle furnace provides the necessary environment for the ceramic to undergo the required physical and chemical changes.
- Metallurgy: In powder metallurgy, sintering is used to create metal parts with specific mechanical properties. The muffle furnace allows for the precise control of temperature and atmosphere, which is essential for achieving the desired microstructure and strength in the final product.
- High-Melting-Point Materials: Sintering is particularly useful for materials with extremely high melting points, such as tungsten and molybdenum. The muffle furnace provides the controlled environment needed to sinter these materials without melting them.
-
Advantages of Using a Muffle Furnace for Sintering:
- Precision: The muffle furnace offers precise control over temperature and atmosphere, which is critical for achieving consistent and high-quality results.
- Versatility: The furnace can be used for a wide range of materials and applications, making it a versatile tool in various industries.
- Efficiency: The ability to perform multiple sintering steps (e.g., binder removal, sintering, and cooling) in a single, continuous process within the furnace increases efficiency and reduces production time.
-
Challenges and Considerations:
- Material Compatibility: Not all materials are suitable for sintering in a muffle furnace. The material must be able to withstand the high temperatures and specific atmospheres used in the process.
- Process Optimization: Achieving the desired material properties requires careful optimization of the sintering parameters, including temperature, heating rate, and atmosphere. This may involve trial and error to determine the optimal conditions for a given material.
- Equipment Maintenance: Regular maintenance of the muffle furnace is essential to ensure consistent performance and prevent issues such as temperature fluctuations or contamination of the furnace atmosphere.
In summary, sintering in a muffle furnace is a critical process for producing dense, durable materials with specific mechanical and physical properties. The muffle furnace provides the controlled environment needed for precise temperature and atmosphere regulation, making it an essential tool in industries such as ceramics, metallurgy, and powder metallurgy. Understanding the key steps and considerations involved in the sintering process is essential for achieving high-quality results and optimizing production efficiency.
Summary Table:
Aspect | Details |
---|---|
Definition | Compacts materials using heat without melting, in a controlled environment. |
Key Steps | Material prep, heating, particle merging, and controlled cooling. |
Applications | Ceramics, metallurgy, and high-melting-point materials like tungsten. |
Advantages | Precise temperature control, versatility, and efficiency. |
Challenges | Material compatibility, process optimization, and equipment maintenance. |
Ready to optimize your sintering process? Contact our experts today for tailored solutions!