Sintering in powder metallurgy is a critical heat treatment process that transforms compacted metal powders into strong, durable, and functional components. By heating the powder compact to temperatures below the melting point of the primary material, sintering bonds the particles together, enhancing mechanical strength, density, and structural integrity. This process is essential for creating end-use parts with precise shapes and properties, making it a cornerstone of modern manufacturing techniques.
Key Points Explained:
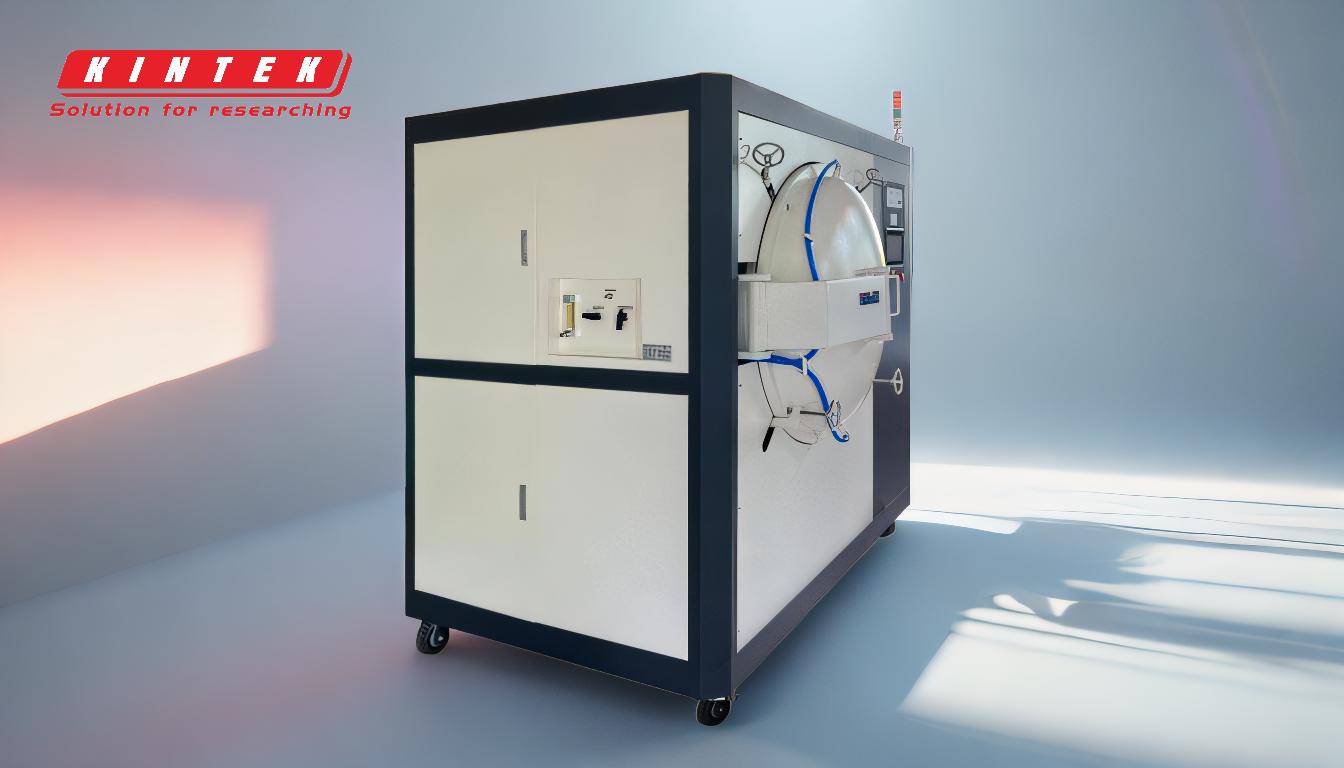
-
Definition of Sintering:
- Sintering is a heat treatment process used in powder metallurgy to bond metal particles together without melting the primary material. This creates a solid, cohesive structure from a compacted powder form.
- The process involves heating the powder compact to temperatures just below the melting point of the major constituent, allowing particles to weld together and form a dense, strong material.
-
Purpose of Sintering:
- Mechanical Strength: Sintering significantly increases the strength of the material by bonding particles together, making the final product suitable for structural applications.
- Density Improvement: The process reduces porosity, enhancing the density and durability of the component.
- Dimensional Stability: Sintering ensures the part maintains its shape and size, which is crucial for precision engineering.
- Translucency and Surface Finish: In some cases, sintering can improve the translucency and surface quality of the material.
-
Stages of the Sintering Process:
- Compaction: Metal powders are first pressed into a specific shape using a die and hydraulic press.
- Heating: The compacted part is then heated in a sintering furnace to a temperature below the melting point of the primary material. This allows particles to bond through diffusion and grain boundary formation.
- Cooling: After sintering, the part is cooled gradually to prevent cracking or warping, ensuring it retains its structural integrity.
-
Applications of Sintering:
- Sintering is widely used in industries such as automotive, aerospace, and electronics to produce components like gears, bearings, and filters.
- It is also employed in the production of ceramics, composites, and advanced materials, where precise control over material properties is required.
-
Advantages of Sintering:
- Cost-Effective: Sintering allows for the production of complex shapes with minimal material waste, reducing manufacturing costs.
- Material Versatility: It can be applied to a wide range of materials, including metals, ceramics, and composites.
- High Precision: The process enables the creation of parts with tight tolerances and consistent quality.
-
Challenges and Considerations:
- Temperature Control: Precise control of the sintering temperature is critical to avoid melting or incomplete bonding.
- Material Selection: The properties of the powder, such as particle size and composition, must be carefully chosen to achieve the desired results.
- Equipment Requirements: High-quality sintering furnaces are essential for consistent and reliable outcomes.
By understanding the principles and applications of sintering, manufacturers can optimize their processes to produce high-quality components efficiently and cost-effectively.
Summary Table:
Aspect | Details |
---|---|
Definition | Heat treatment process bonding metal particles without melting. |
Purpose | Enhances strength, density, and dimensional stability. |
Stages | Compaction → Heating → Cooling. |
Applications | Automotive, aerospace, electronics, ceramics, and composites. |
Advantages | Cost-effective, versatile, and high precision. |
Challenges | Requires precise temperature control, material selection, and quality equipment. |
Discover how sintering can revolutionize your manufacturing process—contact our experts today!