A sintering machine, often referred to as a sintering furnace, is a specialized piece of equipment used in the sintering process, which involves heating powdered materials to a temperature below their melting point to bond particles together without liquefaction. This process is widely used in industries such as ceramics, metals, and plastics to create durable, high-strength products like gears, bearings, and electrical components. Sintering machines are designed with specific zones for pre-heating, heating, and cooling, along with advanced control systems to maintain precise atmospheric conditions. The process is cost-effective, efficient, and versatile, making it essential for producing complex shapes and high-performance materials.
Key Points Explained:
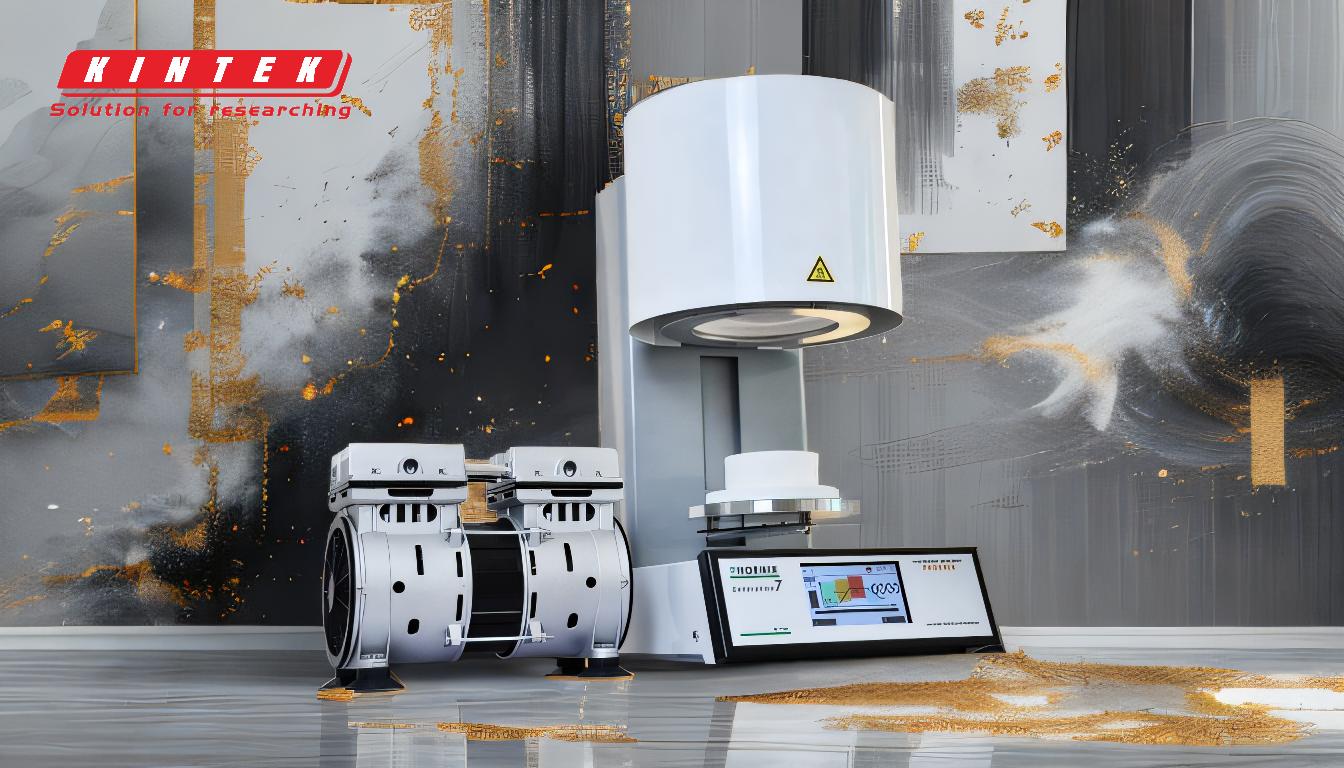
-
Definition and Purpose of Sintering:
- Sintering is a manufacturing process where powdered materials are heated to a temperature below their melting point, causing particles to bond through atomic diffusion.
- The primary goal is to create a solid, dense material with improved mechanical strength, density, and translucency without melting the material entirely.
- This process is used across various industries, including ceramics, metals, and plastics, to produce components like gears, bearings, and electrical contacts.
-
How Sintering Works:
- The process involves three main stages:
- Forming the Green Part: A powder blend mixed with a temporary bonding agent (e.g., wax or polymer) is molded into the desired shape.
- Binder Removal: During heating, the bonding agent evaporates or burns away.
- Particle Fusion: The temperature is increased to a point where particles begin to fuse at their surfaces or an intermediate bonding agent (e.g., bronze) melts, coupling the particles together.
- The result is a solid piece with reduced porosity and enhanced mechanical properties.
- The process involves three main stages:
-
Components of a Sintering Machine:
- Sintering furnaces are equipped with several key components:
- Pre-Heat Zone: Prepares the material for the sintering process.
- Hot Zone: Maintains the high temperatures required for particle fusion.
- Jacketed Water Cooling Zone: Cools the material after sintering.
- Feeding and Exit Doors: Allow for the loading and unloading of materials.
- Flame Curtains: Prevent atmospheric contamination.
- Control Panel: Ensures precise regulation of temperature and atmosphere.
- Modern sintering machines, such as Sinter-HIP furnaces, also include vacuum systems and high-pressure capabilities for enhanced efficiency.
- Sintering furnaces are equipped with several key components:
-
Applications of Sintering Machines:
- Sintering is used to produce a wide range of industrial and consumer products, including:
- Mechanical Components: Gears, couplings, bearings, pulleys, and sprockets.
- Electrical Components: Contacts, armatures, and rotors.
- Ceramics and Metals: High-performance materials for aerospace, automotive, and medical industries.
- The versatility of sintering makes it suitable for creating complex shapes and high-strength materials.
- Sintering is used to produce a wide range of industrial and consumer products, including:
-
Advantages of Sintering:
- Cost-Effectiveness: Sintering is a low-energy process compared to melting and casting.
- Material Efficiency: It minimizes waste by using powdered materials.
- Versatility: Suitable for a wide range of materials and applications.
- Improved Properties: Produces materials with high density, strength, and durability.
-
Types of Sintering Machines:
- Standard Sintering Furnaces: Used for basic sintering processes with controlled heating and cooling zones.
- Sinter-HIP Furnaces: Advanced machines that combine sintering with Hot Isostatic Pressing (HIP) to achieve higher density and strength. These furnaces can create a vacuum environment and apply high pressure simultaneously, improving product quality and production efficiency.
-
Role of Sintering in Manufacturing:
- Sintering is a critical step in the production of many industrial components, enabling the creation of complex geometries and high-performance materials.
- It is particularly important in industries where precision, durability, and material properties are paramount, such as aerospace, automotive, and medical device manufacturing.
In summary, a sintering machine is an essential tool in modern manufacturing, enabling the production of high-quality, durable materials through a controlled heating process. Its versatility, cost-effectiveness, and ability to produce complex shapes make it indispensable across various industries.
Summary Table:
Key Aspect | Details |
---|---|
Definition | A sintering machine heats powdered materials below their melting point to bond particles. |
Process Stages | 1. Forming the green part |
- Binder removal
- Particle fusion | | Key Components | Pre-heat zone, hot zone, cooling zone, feeding/exit doors, flame curtains, control panel | | Applications | Gears, bearings, electrical components, aerospace, automotive, and medical materials | | Advantages | Cost-effective, material-efficient, versatile, and produces high-density materials | | Types of Machines | Standard sintering furnaces, Sinter-HIP furnaces |
Ready to enhance your manufacturing process with a sintering machine? Contact us today to learn more!