Sintering metallurgy is a manufacturing process that involves compacting and fusing metal powders into a solid mass using heat and pressure, without reaching the material's melting point. This process enhances the mechanical properties of the final product, such as strength and durability, while allowing for precise control over dimensions and material characteristics. Sintering is widely used in producing metal components like gears, bearings, and automotive parts, leveraging materials such as iron, aluminum, and stainless steel. The process includes steps like lubricant removal, oxide reduction, particle bonding, and controlled cooling, making it a versatile and efficient method for creating high-performance metal parts.
Key Points Explained:
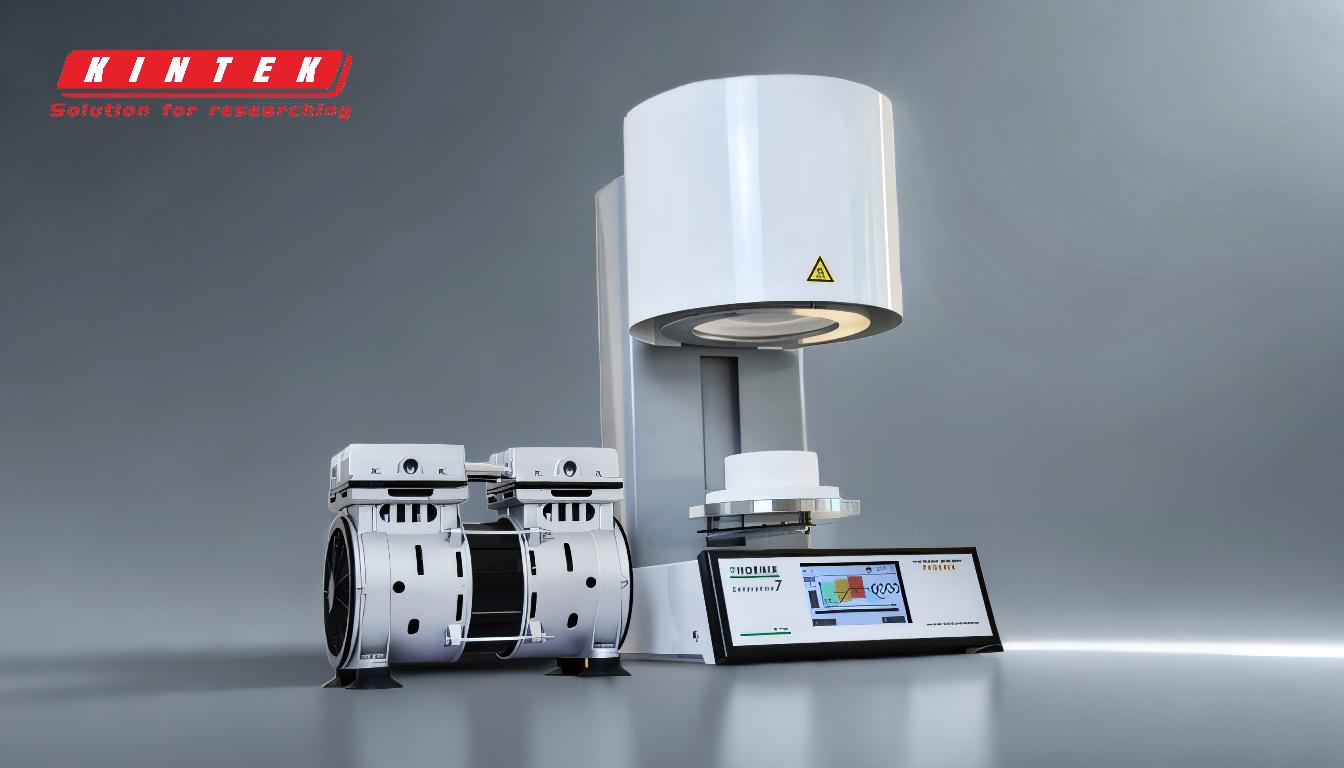
-
Definition of Sintering Metallurgy:
- Sintering is a heat treatment process that bonds metal powder particles into a solid mass without melting the material.
- It involves applying heat and pressure below the material's melting point to fuse particles, creating a structurally sound component.
-
Mechanism of Sintering:
- Diffusion of Atoms: Atoms diffuse across particle boundaries, causing them to bond and form a single solid piece.
- Temperature Control: The process occurs at temperatures below the melting point of the metal, ensuring the material remains solid.
- Pressure Application: Pressure is often applied to compact the powder, enhancing particle bonding and reducing porosity.
-
Steps in the Sintering Process:
- Compaction: Metal powders are pressed into a "green" part with a specific shape.
- Lubricant Removal: Any lubricants used during compaction are removed to prevent contamination.
- Oxide Reduction: Oxide layers on the powder particles are reduced to improve bonding.
- Particle Bonding: Heat is applied to fuse the particles, creating a dense and strong structure.
- Cooling: The part is cooled at a controlled rate to fine-tune its mechanical properties.
-
Materials Used in Sintering:
- Common metals include iron, aluminum, stainless steel, tungsten, and molybdenum.
- Alloying elements can be added to enhance specific properties like hardness or corrosion resistance.
-
Applications of Sintering Metallurgy:
- Automotive Industry: Used to manufacture gears, bearings, and bushings.
- Structural Components: Produces high-strength parts for machinery and equipment.
- Custom Parts: Enables the production of complex shapes with precise dimensions.
-
Advantages of Sintering:
- Material Efficiency: Minimizes waste by using precise amounts of metal powder.
- Cost-Effective: Reduces machining and finishing requirements.
- Versatility: Suitable for a wide range of metals and alloys.
- Enhanced Properties: Improves mechanical properties like strength, wear resistance, and durability.
-
Challenges and Considerations:
- Porosity: Sintered parts may have residual porosity, which can affect strength.
- Dimensional Control: Shrinkage during sintering must be accounted for during the design phase.
- Material Selection: The choice of metal powder and alloying elements is critical for achieving desired properties.
-
Industrial Relevance:
- Sintering is a cornerstone of powder metallurgy, enabling the production of high-performance components for industries like aerospace, automotive, and manufacturing.
- It is particularly valuable for materials with high melting points, where traditional melting and casting methods are impractical.
By understanding these key points, equipment and consumable purchasers can better evaluate the suitability of sintered metal components for their specific applications, ensuring optimal performance and cost-effectiveness.
Summary Table:
Aspect | Details |
---|---|
Definition | Bonds metal powders using heat and pressure without melting. |
Mechanism | Diffusion of atoms, temperature control, and pressure application. |
Steps | Compaction, lubricant removal, oxide reduction, particle bonding, cooling. |
Materials | Iron, aluminum, stainless steel, tungsten, molybdenum. |
Applications | Gears, bearings, automotive parts, structural components, custom parts. |
Advantages | Material efficiency, cost-effectiveness, versatility, enhanced properties. |
Challenges | Porosity, dimensional control, material selection. |
Industrial Relevance | Key for aerospace, automotive, and manufacturing industries. |
Discover how sintering metallurgy can optimize your production process—contact us today for expert advice!