Sintering of clay materials is a heat treatment process that transforms powdered clay into a dense, strong, and durable ceramic body. This process involves heating the clay below its melting point, allowing particles to bond through solid-state diffusion, resulting in reduced porosity, increased density, and improved mechanical properties. Sintering is critical for achieving the desired microstructure, dimensional stability, and functional characteristics of ceramic products. It is widely used in industries to create complex shapes, enhance material properties, and enable cost-effective mass production.
Key Points Explained:
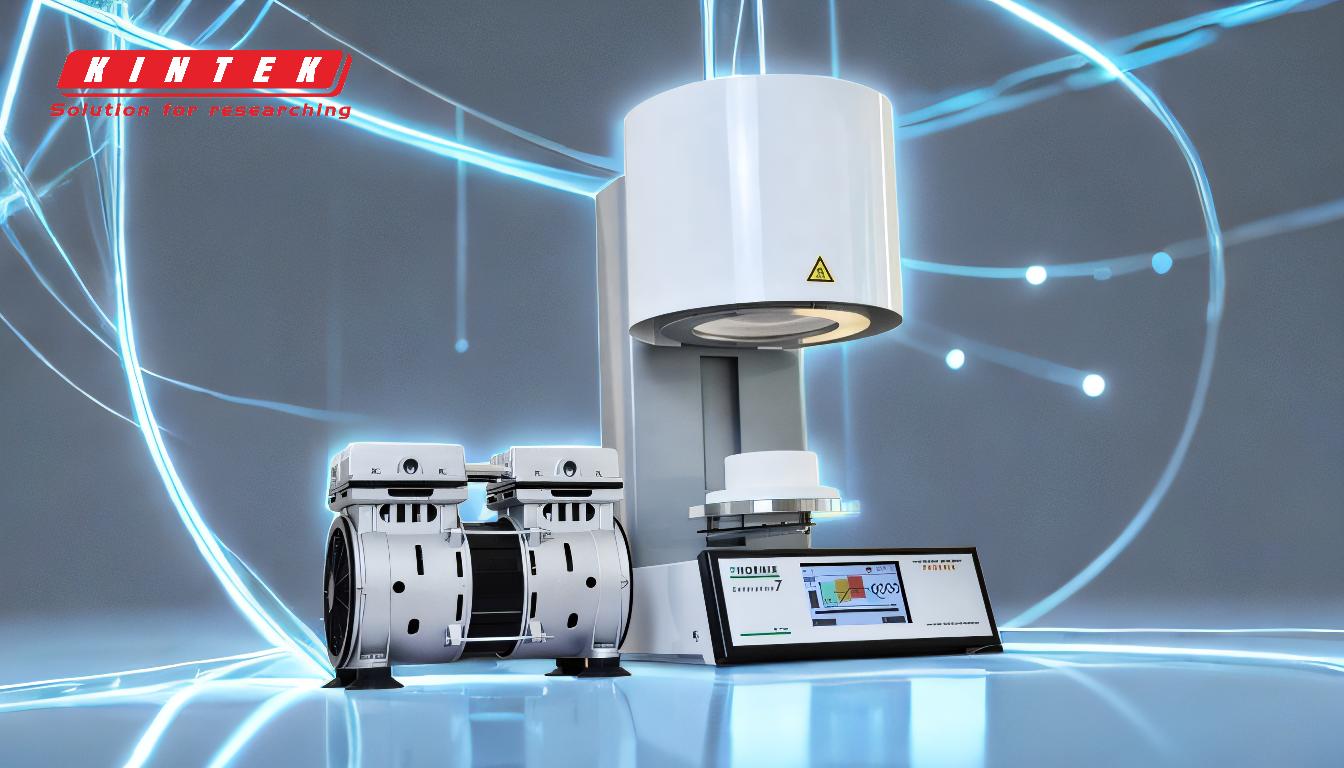
-
Definition of Sintering:
- Sintering is a thermal process used to densify powdered materials, such as clay, by heating them below their melting point. This process transforms loose particles into a solid, cohesive structure through particle bonding and pore elimination.
-
Purpose of Sintering:
- Densification: Reduces porosity and increases the density of the material.
- Strength Enhancement: Improves mechanical properties like hardness, toughness, and durability.
- Microstructure Formation: Creates a uniform and stable microstructure with specific properties.
- Dimensional Stability: Accounts for minor shrinkage during the process to achieve precise final dimensions.
-
Mechanism of Sintering:
- Solid-State Diffusion: Atoms move across particle surfaces, necks, and grain boundaries, leading to bonding and densification.
- Grain Growth: Particles merge, and grains grow larger, reducing voids and grain boundaries.
- Material Transfer: Mass transfer mechanisms, such as surface diffusion and evaporation-condensation, contribute to densification.
-
Stages of Sintering:
- Initial Stage: Particle rearrangement and neck formation between particles.
- Intermediate Stage: Pores become interconnected, and densification accelerates.
- Final Stage: Pores become isolated, and the material reaches near-theoretical density.
-
Factors Influencing Sintering:
- Temperature: Higher temperatures enhance diffusion and bonding but must remain below the melting point.
- Time: Longer sintering durations allow for greater densification and grain growth.
- Atmosphere: Controlled environments (e.g., inert or reducing atmospheres) prevent oxidation and contamination.
- Particle Size: Smaller particles sinter more efficiently due to higher surface energy.
- Additives: Fluxes or sintering aids can lower the required temperature and improve densification.
-
Applications of Sintering in Clay Materials:
- Ceramics: Used to produce advanced ceramics with tailored properties for electronics, aerospace, and medical applications.
- Structural Products: Creates bricks, tiles, and pottery with enhanced strength and durability.
- Complex Shapes: Enables the production of intricate geometries that are difficult to achieve with other methods.
- Cost-Effective Manufacturing: Reduces tooling costs and supports rapid mass production.
-
Advantages of Sintering:
- Versatility: Suitable for a wide range of materials, including ceramics, metals, and composites.
- Precision: Achieves high dimensional accuracy and repeatability.
- Material Properties: Combines desirable properties like toughness, abrasion resistance, and thermal stability.
- Sustainability: Minimizes material waste and energy consumption compared to melting processes.
-
Challenges in Sintering:
- Shrinkage: Volume reduction must be carefully controlled to avoid defects.
- Microstructural Defects: Inhomogeneities or residual pores can weaken the final product.
- Process Optimization: Balancing temperature, time, and atmosphere requires precise control.
-
Comparison with Other Processes:
- Sintering vs. Melting: Sintering occurs below the melting point, preserving the material's original composition and shape.
- Sintering vs. Compaction: Compaction forms the green body, while sintering densifies and strengthens it.
-
Future Trends in Sintering:
- Advanced Materials: Development of nanocomposites and functionally graded materials.
- Energy Efficiency: Innovations in furnace technology to reduce energy consumption.
- Additive Manufacturing: Integration of sintering with 3D printing for complex, high-performance components.
In summary, sintering is a transformative process that plays a vital role in the production of clay-based ceramics and other materials. By understanding its mechanisms, stages, and influencing factors, manufacturers can optimize the process to achieve superior material properties and meet diverse industrial needs.
Summary Table:
Aspect | Details |
---|---|
Definition | Heat treatment process to densify powdered clay below its melting point. |
Purpose | Densification, strength enhancement, microstructure formation, stability. |
Mechanism | Solid-state diffusion, grain growth, material transfer. |
Stages | Initial, intermediate, and final stages of pore elimination. |
Influencing Factors | Temperature, time, atmosphere, particle size, additives. |
Applications | Ceramics, structural products, complex shapes, cost-effective manufacturing. |
Advantages | Versatility, precision, enhanced material properties, sustainability. |
Challenges | Shrinkage, microstructural defects, process optimization. |
Future Trends | Advanced materials, energy efficiency, additive manufacturing. |
Optimize your ceramic production with sintering—contact our experts today to learn more!