Sintering pressing force in ceramics refers to the external pressure applied during the sintering process to enhance densification and reduce porosity. This force aids in particle rearrangement and promotes better bonding between ceramic particles, leading to improved material properties such as strength and density. The application of pressure is particularly useful for materials that are difficult to sinter under standard conditions, as it provides an additional driving force for fusion. Factors like temperature, heating rate, and particle size also play crucial roles in the sintering process, but the pressing force is a key parameter that can significantly influence the final microstructure and properties of the ceramic material.
Key Points Explained:
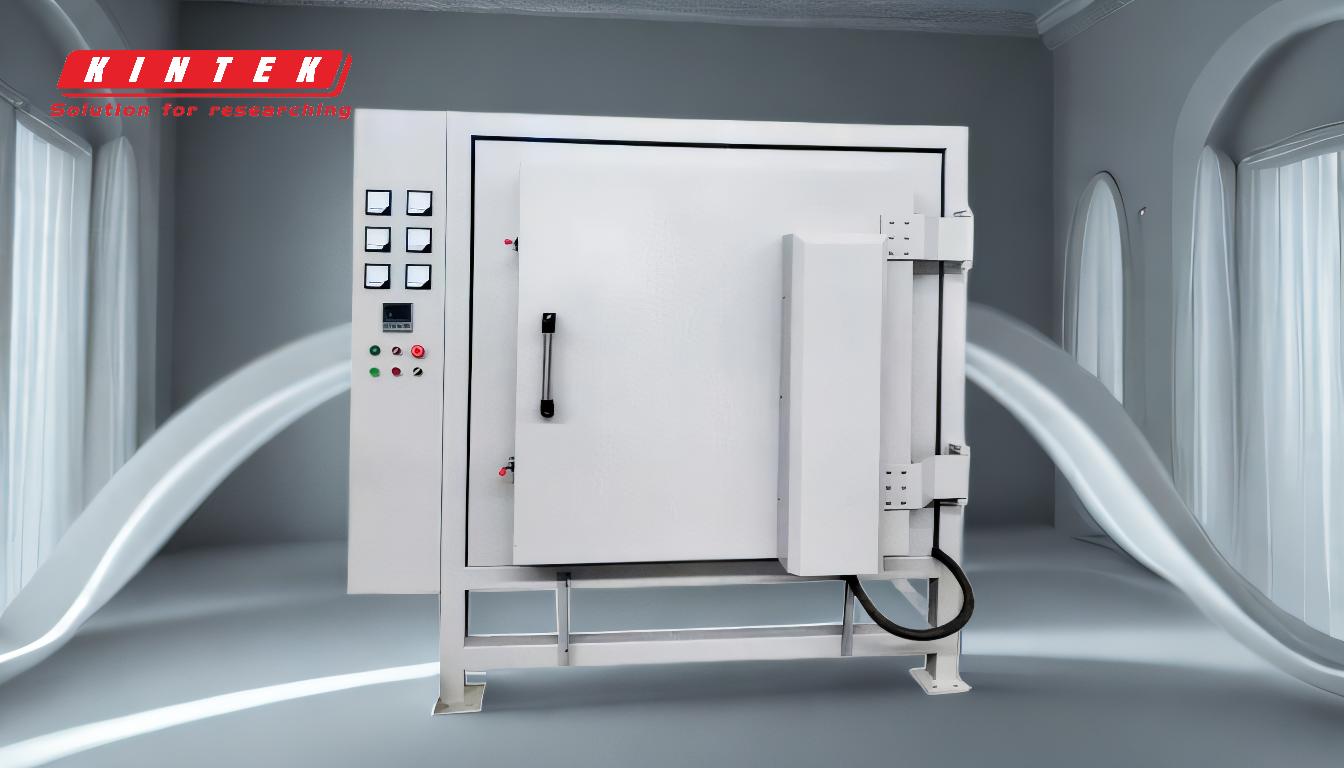
-
Definition of Sintering Pressing Force:
- Sintering pressing force is the external pressure applied during the sintering process to enhance the densification of ceramic materials.
- This force helps in reducing porosity and improving the mechanical properties of the final product.
-
Role of Pressure in Sintering:
- Particle Rearrangement: Pressure aids in the movement and rearrangement of ceramic particles, facilitating closer packing.
- Enhanced Bonding: The applied force promotes better bonding between particles, leading to a more uniform and dense microstructure.
- Reduction of Porosity: By applying pressure, the voids and pores within the ceramic material are minimized, resulting in a denser final product.
-
Techniques Involving Sintering Pressing Force:
- Hot Pressing: This technique involves applying pressure simultaneously with heat treatment. It is particularly useful for materials that are difficult to sinter under standard conditions.
- Spark Plasma Sintering (SPS): This method uses electrical currents and pressure to achieve rapid densification at lower temperatures compared to conventional sintering.
-
Factors Influencing Sintering Pressing Force:
- Temperature: Higher temperatures can enhance the effectiveness of the pressing force by increasing the mobility of atoms and facilitating diffusion.
- Heating Rate: A controlled heating rate ensures uniform densification and prevents defects such as cracks or warping.
- Particle Size: Smaller particles have a higher surface area to volume ratio, which can improve the effectiveness of the pressing force in promoting densification.
- Composition: Homogeneous compositions are more likely to achieve uniform densification under applied pressure.
-
Benefits of Optimized Sintering Pressing Force:
- Improved Mechanical Properties: Enhanced strength, hardness, and toughness due to reduced porosity and better particle bonding.
- Controlled Shrinkage: Application of pressure can help in controlling the shrinkage that occurs during sintering, leading to more precise final dimensions.
- Material Versatility: Allows for the sintering of materials that are otherwise difficult to densify, expanding the range of applications for ceramic materials.
-
Applications of Sintering Pressing Force:
- Advanced Ceramics: Used in the production of high-performance ceramics for applications in electronics, aerospace, and biomedical fields.
- Pottery and Traditional Ceramics: Enhances the strength and durability of ceramic objects like pottery.
- Composite Materials: Facilitates the densification of ceramic matrix composites, which require high strength and low porosity.
In summary, sintering pressing force is a critical parameter in the ceramic sintering process that significantly influences the densification, microstructure, and final properties of ceramic materials. By understanding and optimizing this force, manufacturers can produce high-quality ceramics with tailored properties for a wide range of applications.
Summary Table:
Aspect | Details |
---|---|
Definition | External pressure applied during sintering to enhance densification. |
Role of Pressure | Aids particle rearrangement, enhances bonding, and reduces porosity. |
Techniques | Hot Pressing, Spark Plasma Sintering (SPS). |
Influencing Factors | Temperature, heating rate, particle size, composition. |
Benefits | Improved mechanical properties, controlled shrinkage, material versatility. |
Applications | Advanced ceramics, pottery, composite materials. |
Optimize your ceramic sintering process—contact our experts today for tailored solutions!