Sintering is a versatile manufacturing process with applications across multiple industries. It is primarily used to join metal particles, especially those with high melting points, and to create custom metal shapes through 3D printing, offering energy efficiency compared to melting. Sintering reduces material porosity, enhancing properties like strength and durability. It is widely applied in industries such as aerospace, automotive, healthcare, battery manufacturing, and research laboratories. Additionally, sintering is used in traditional ceramic production, powder metallurgy, and additive manufacturing, making it essential for creating complex, high-performance components and materials.
Key Points Explained:
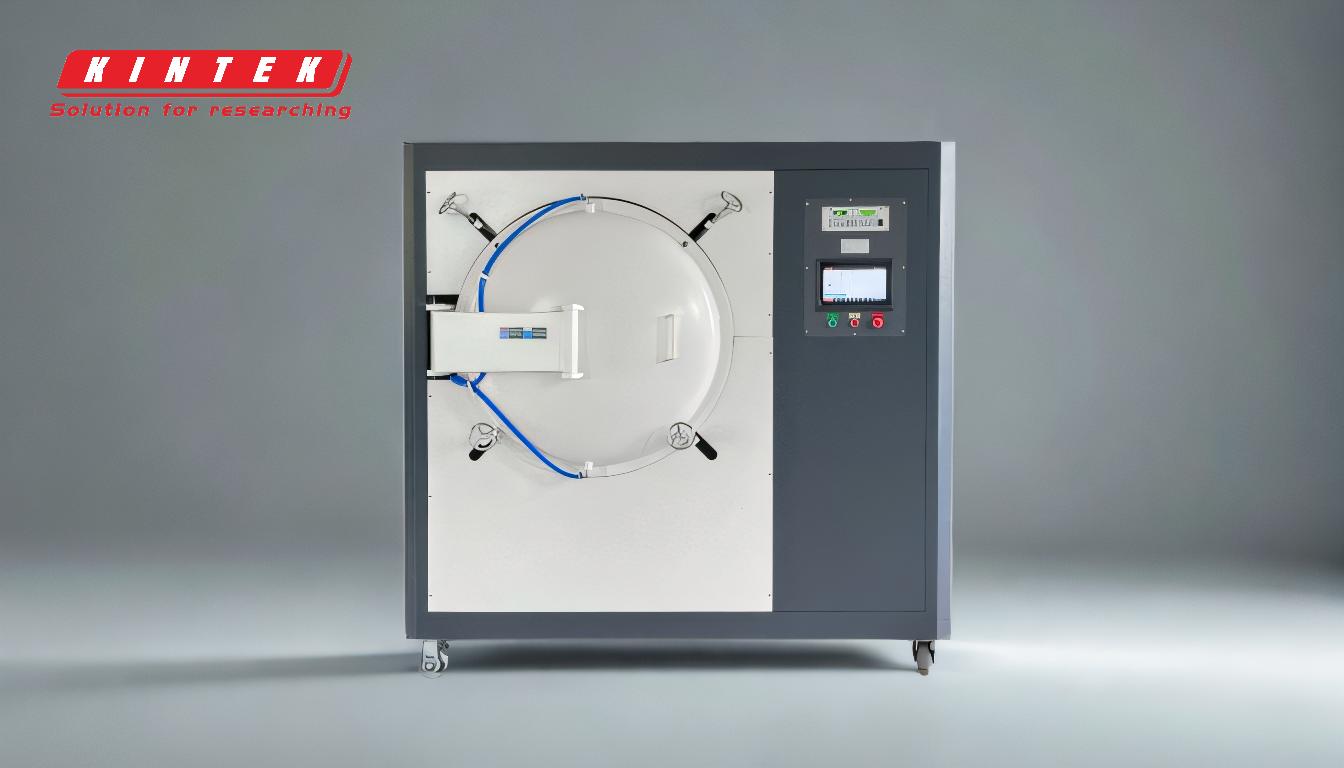
-
Joining Metal Particles and High-Melting-Point Metals
- Sintering is particularly useful for metals with high melting points, such as tungsten and molybdenum, which are difficult to melt using conventional methods.
- The process involves heating metal particles below their melting point, allowing them to bond without liquefaction. This is energy-efficient and preserves the material's structural integrity.
- Applications include the production of refractory metals used in extreme environments, such as aerospace and industrial machinery.
-
Additive Manufacturing and 3D Printing
- Sintering is integral to additive manufacturing, enabling the creation of custom metal shapes layer by layer.
- In 3D metal printing, sintering allows for precise control over the final product's geometry and properties, making it ideal for prototyping and small-batch production.
- Industries like aerospace, healthcare, and automotive benefit from this technology for producing lightweight, durable, and complex components.
-
Reducing Porosity and Enhancing Material Properties
- Sintering decreases the porosity of materials, leading to improved mechanical properties such as strength, hardness, and wear resistance.
- This is particularly important for components subjected to high stress or corrosive environments, such as engine parts, dental implants, and battery electrodes.
- The process also enhances thermal and electrical conductivity, making it valuable for electronic and energy storage applications.
-
Applications in Powder Metallurgy
- Powder metallurgy relies on sintering to form metal powders into solid parts. This method is cost-effective and allows for the production of intricate shapes with minimal waste.
- Common products include gears, bearings, and filters, which are used in automotive, engineering, and industrial applications.
- The ability to combine different metals and alloys during sintering expands the range of possible materials and applications.
-
Use in Ceramic Production
- Sintering is traditionally used in ceramic manufacturing to create durable and heat-resistant objects, such as tiles, insulators, and cutting tools.
- The process strengthens ceramic materials by reducing voids and improving density, making them suitable for high-temperature and high-stress environments.
- Applications include aerospace components, medical devices, and industrial machinery.
-
Industrial and Laboratory Applications
- Sintering furnaces are widely used in laboratories, industrial facilities, and research units for tasks such as element analysis, heat treatment, and metal-ceramic sintering.
- These furnaces enable precise control over temperature and atmosphere, ensuring consistent results for high-performance materials.
- Applications include small-scale steel hardening, annealing, tempering, and the production of advanced materials for scientific research.
-
Expanding Applications in Emerging Industries
- Sintering is increasingly used in battery manufacturing, where it helps produce electrodes with improved conductivity and durability.
- The healthcare industry utilizes sintering for creating custom dental and orthopedic implants with precise dimensions and biocompatibility.
- As sintering technologies advance, new applications continue to emerge in fields like renewable energy, electronics, and advanced materials research.
In summary, sintering is a critical process for creating high-performance materials and components across a wide range of industries. Its ability to join metals, reduce porosity, and enable precise manufacturing makes it indispensable for applications requiring durability, precision, and efficiency.
Summary Table:
Key Aspect | Details |
---|---|
Joining High-Melting Metals | Bonds metals like tungsten and molybdenum without melting, preserving integrity. |
Additive Manufacturing | Enables 3D printing of custom metal shapes for lightweight, durable components. |
Reduced Porosity | Improves strength, hardness, and wear resistance for high-stress applications. |
Powder Metallurgy | Forms intricate shapes with minimal waste, used in gears, bearings, and filters. |
Ceramic Production | Creates durable, heat-resistant ceramics for aerospace and medical devices. |
Industrial Applications | Used in labs and industries for heat treatment, element analysis, and research. |
Emerging Industries | Expands into battery manufacturing, healthcare implants, and renewable energy. |
Unlock the potential of sintering for your industry—contact our experts today!