Sintering with hydrogen is a specialized pyrometallurgical process where powdered materials, typically metals or ceramics, are heated below their melting point in a hydrogen-rich atmosphere to form a dense, solid mass. This process leverages hydrogen's unique properties to enhance material purity, reduce surface oxides, and remove impurities like silica, resulting in high-quality sintered products. It is particularly useful for materials with high melting points, such as tungsten and molybdenum, and is widely applied in industries like powder metallurgy and ceramics. The hydrogen atmosphere ensures a controlled, reducing environment, which improves the density, corrosion resistance, and overall performance of the final product.
Key Points Explained:
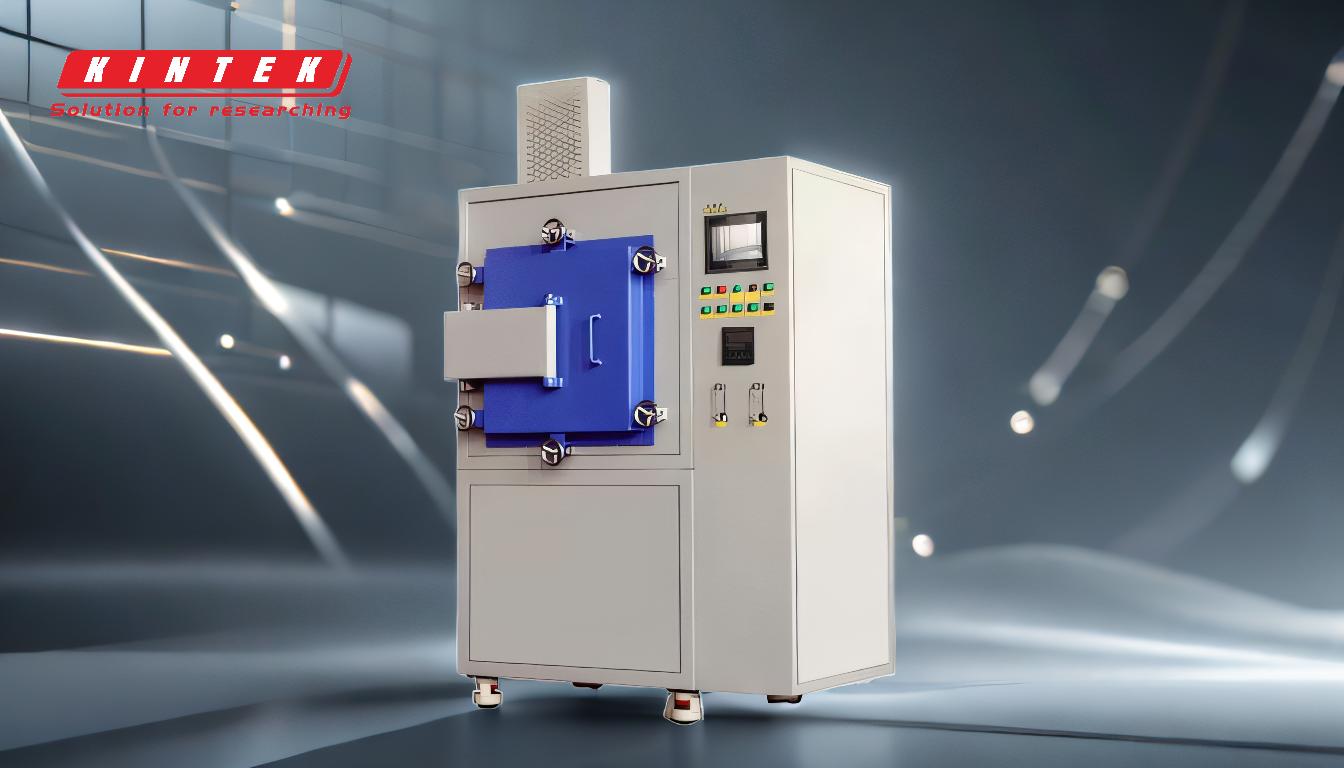
-
Definition of Sintering with Hydrogen:
- Sintering is a process where powdered materials are heated below their melting point to form a solid mass without liquefaction.
- Hydrogen sintering involves performing this process in a hydrogen-rich atmosphere, such as pure hydrogen, a hydrogen/nitrogen mixture, or dissociated ammonia.
- This method is particularly effective for materials with high melting points, like tungsten and molybdenum.
-
Purpose and Benefits of Hydrogen Sintering:
- Density and Corrosion Resistance: Hydrogen sintering maximizes key properties like density and corrosion resistance in the final product.
- Surface Oxide Reduction: Hydrogen helps reduce surface oxides, which is critical for achieving high-quality sintered parts.
- Impurity Removal: It strips impurities, such as silica (SiO2), from alloys, enhancing material purity and performance.
- High Purity Atmosphere: Hydrogen provides a high-purity environment (>99.9995%), which is suitable for a wide range of materials, including stainless steel.
-
Applications of Hydrogen Sintering:
- Powder Metallurgy: Used to produce complex shapes, gears, bearings, and other components in industries like automotive and aerospace.
- Ceramics: Applied in the production of pottery and other ceramic products to achieve densification without melting.
- High-Melting-Point Metals: Ideal for materials like tungsten and molybdenum, which are challenging to process using traditional methods.
-
Process Mechanics:
- Solid-State Diffusion: During sintering, atoms diffuse across particle boundaries, fusing them into a single solid piece.
- Temperature Control: The process occurs below the material's melting point, ensuring the material retains its structural integrity.
- Atmosphere Control: The hydrogen atmosphere ensures a reducing environment, which prevents oxidation and enhances material properties.
-
Advantages Over Other Sintering Methods:
- Cost-Effectiveness: Hydrogen sintering is efficient and cost-effective compared to other high-temperature processes.
- Versatility: It can be applied to a wide range of materials and industries, from metals to ceramics.
- Improved Furnace Performance: The use of hydrogen lowers the dew point, enhancing reducing conditions and improving furnace efficiency.
-
Industrial Relevance:
- Steel Manufacturing: Used to remove internal stresses and produce high-quality steel products.
- Alloy Production: Essential for creating alloys with specific properties, such as increased strength or corrosion resistance.
- Complex Shapes: Enables the production of intricate components that would be difficult to achieve through other methods.
By leveraging hydrogen's unique properties, sintering with hydrogen offers a highly effective and versatile method for producing high-quality, dense, and corrosion-resistant materials across various industries.
Summary Table:
Key Aspect | Details |
---|---|
Process Definition | Heating powdered materials below melting point in a hydrogen-rich atmosphere. |
Key Benefits | - Enhanced material purity - Reduced surface oxides - Impurity removal |
Applications | - Powder metallurgy - Ceramics - High-melting-point metals |
Advantages | - Cost-effective - Versatile - Improved furnace performance |
Industrial Relevance | - Steel manufacturing - Alloy production - Complex shapes |
Learn how hydrogen sintering can optimize your production process—contact us today!