Spark plasma sintering (SPS) is an advanced sintering technique that combines the application of pressure and pulsed electric current to achieve rapid densification of materials at relatively lower temperatures compared to conventional sintering methods. This process is particularly effective for producing high-density, fine-grained materials with enhanced mechanical properties. The key advantage of SPS lies in its ability to achieve rapid heating and cooling rates, which minimizes grain growth and allows for the preservation of nanostructures. This makes it highly suitable for advanced materials such as ceramics, metals, and composites.
Key Points Explained:
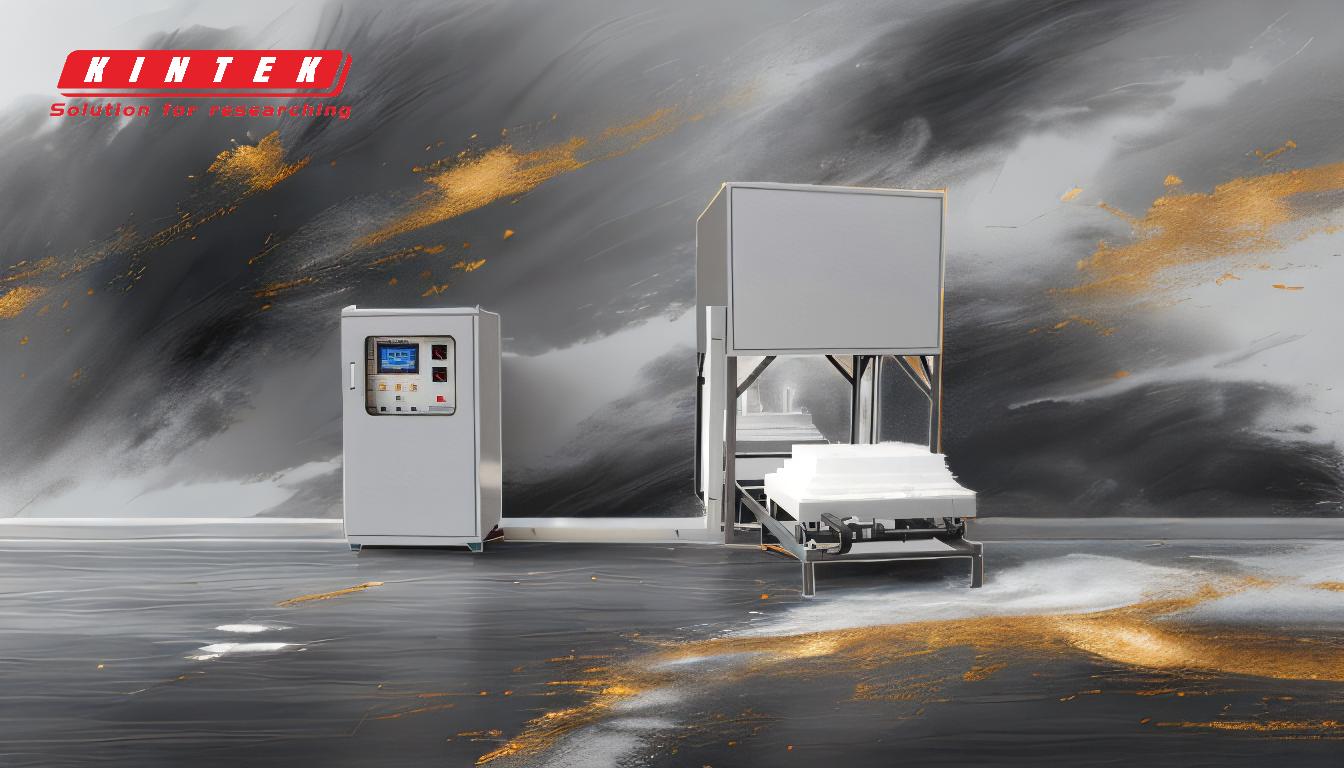
-
Basic Principles of Spark Plasma Sintering:
- SPS utilizes a pulsed direct current (DC) that passes through the material and the die, generating localized heating through Joule heating and spark plasma discharge.
- The simultaneous application of uniaxial pressure and electric current facilitates rapid particle bonding and densification.
- Unlike traditional sintering, SPS achieves densification at lower temperatures and shorter processing times, which helps in retaining the material's microstructural integrity.
-
Stages of the SPS Process:
- Powder Preparation: The raw material is prepared in the form of fine powder, which is then loaded into a graphite die.
- Compaction: The powder is compacted under moderate pressure to ensure uniform distribution and eliminate voids.
- Heating and Sintering: A pulsed DC current is applied, generating heat internally within the material. This rapid heating promotes particle bonding and densification.
- Cooling: After sintering, the material is cooled rapidly, which helps in maintaining the fine-grained structure and prevents grain growth.
-
Advantages of Spark Plasma Sintering:
- Rapid Processing: SPS can achieve full densification in a matter of minutes, compared to hours or even days required by conventional sintering methods.
- Lower Sintering Temperatures: The process operates at temperatures significantly lower than the melting point of the material, reducing the risk of thermal degradation.
- Enhanced Material Properties: SPS produces materials with high density, fine grain size, and improved mechanical properties such as hardness, strength, and wear resistance.
- Versatility: SPS is applicable to a wide range of materials, including ceramics, metals, composites, and even nanomaterials.
-
Applications of Spark Plasma Sintering:
- Advanced Ceramics: SPS is widely used for producing high-performance ceramics with superior mechanical and thermal properties.
- Metals and Alloys: The process is effective in sintering metals and alloys, particularly those that are difficult to densify using conventional methods.
- Nanomaterials: SPS is ideal for consolidating nanomaterials while preserving their nanostructure, which is crucial for applications in electronics, catalysis, and energy storage.
- Composites: SPS enables the production of composite materials with tailored properties by combining different materials in a single sintering step.
-
Comparison with Conventional Sintering:
- Conventional sintering relies on external heating sources and longer processing times, which can lead to grain growth and reduced material properties.
- SPS, on the other hand, utilizes internal heating through electric current, resulting in faster densification and better control over the microstructure.
- The ability to apply pressure during sintering in SPS further enhances densification and reduces porosity.
In summary, spark plasma sintering is a highly efficient and versatile sintering technique that offers significant advantages over traditional methods. Its ability to produce high-density, fine-grained materials with enhanced properties makes it a valuable tool in advanced materials manufacturing.
Summary Table:
Aspect | Details |
---|---|
Process | Combines pressure and pulsed electric current for rapid densification. |
Key Advantages | Rapid processing, lower sintering temperatures, enhanced material properties. |
Applications | Advanced ceramics, metals, alloys, nanomaterials, and composites. |
Comparison | Faster and more efficient than conventional sintering methods. |
Learn how spark plasma sintering can revolutionize your material production—contact our experts today!