Spray pyrolysis is a versatile chemical deposition method used to create thin films or coatings by spraying a precursor solution onto a heated substrate. This technique is widely employed in materials science and engineering for producing high-quality films with controlled composition and microstructure. The process involves atomizing a solution into fine droplets, which are then transported to a heated surface where they undergo thermal decomposition to form the desired material. Spray pyrolysis is valued for its simplicity, scalability, and ability to produce uniform coatings over large areas. It is particularly useful in applications such as solar cells, sensors, and catalysts, where precise control over film properties is essential.
Key Points Explained:
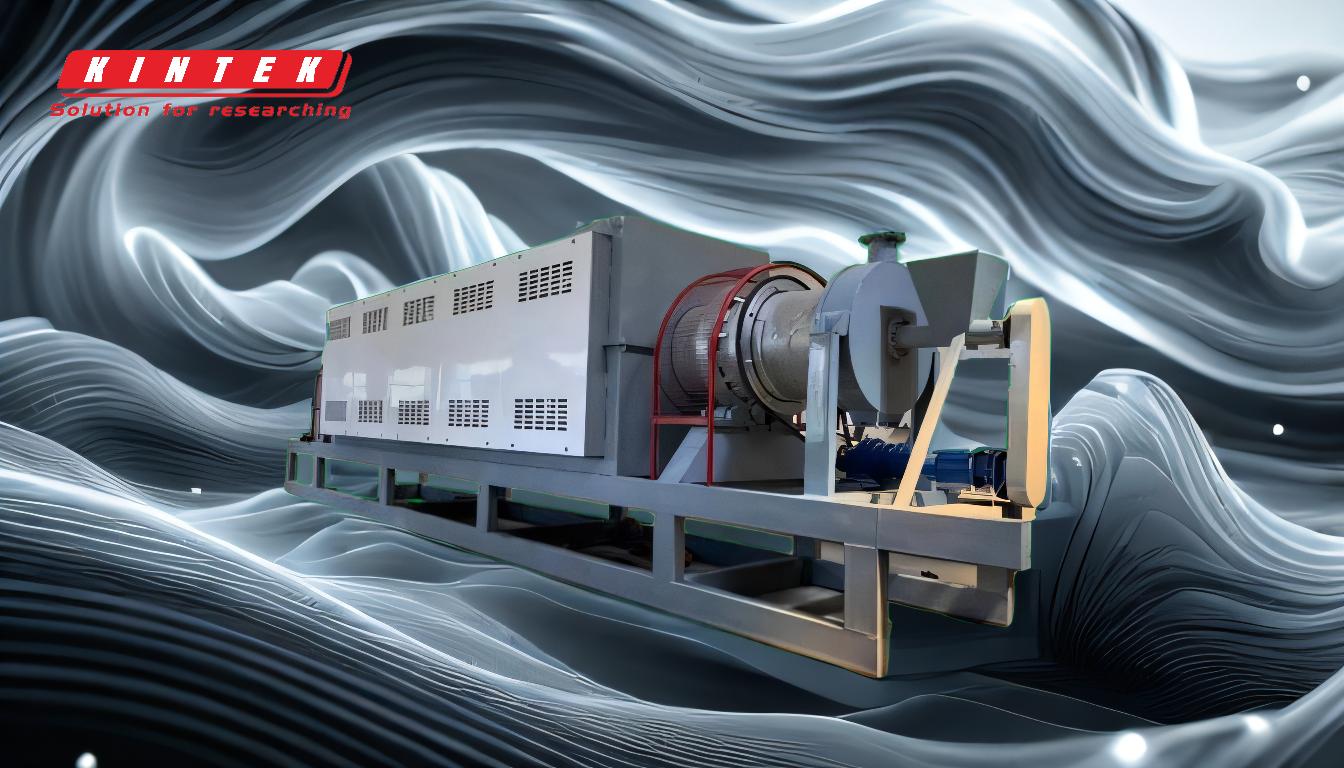
-
Definition and Process:
- Spray pyrolysis is a chemical deposition technique where a precursor solution is atomized into fine droplets and sprayed onto a heated substrate.
- The droplets undergo thermal decomposition upon contact with the hot surface, forming a thin film or coating.
-
Key Components:
- Precursor Solution: Contains the desired chemical compounds dissolved in a solvent.
- Atomizer: Converts the solution into fine droplets, typically using high-pressure nozzles or ultrasonic methods.
- Heated Substrate: Provides the thermal energy needed for decomposition and film formation.
- Reactor Chamber: Maintains controlled environmental conditions, such as temperature and gas flow.
-
Advantages:
- Scalability: Suitable for both laboratory-scale experiments and industrial production.
- Uniformity: Produces films with consistent thickness and composition over large areas.
- Versatility: Can be used to deposit a wide range of materials, including metals, oxides, and composites.
- Cost-Effectiveness: Requires relatively simple equipment and can operate at ambient pressure.
-
Applications:
- Solar Cells: Used to deposit transparent conductive oxides and absorber layers.
- Sensors: Produces thin films with tailored electrical and optical properties for gas and chemical sensing.
- Catalysts: Creates coatings with high surface area and controlled porosity for catalytic applications.
- Protective Coatings: Forms durable and corrosion-resistant layers on metals and ceramics.
-
Comparison with Other Pyrolysis Methods:
- Unlike conventional pyrolysis, which involves bulk heating of materials, spray pyrolysis focuses on localized thermal decomposition of droplets.
- It offers better control over film properties compared to methods like flash pyrolysis or ablative pyrolysis, which are more suited for bulk material processing.
-
Challenges and Considerations:
- Precursor Selection: The choice of precursor and solvent affects the quality and properties of the deposited film.
- Temperature Control: Precise control of substrate temperature is crucial to avoid defects and ensure uniform decomposition.
- Droplet Size and Distribution: Smaller droplets lead to finer films, but achieving consistent droplet size can be challenging.
-
Environmental and Economic Aspects:
- Spray pyrolysis is generally more energy-efficient than traditional pyrolysis methods, as it targets localized heating.
- It can be adapted to use eco-friendly solvents and precursors, reducing environmental impact.
- The modular design of spray pyrolysis systems allows for easy customization and integration into existing production lines.
By understanding these key points, equipment and consumable purchasers can evaluate the suitability of spray pyrolysis for their specific applications and make informed decisions about adopting this technology.
Summary Table:
Aspect | Details |
---|---|
Definition | Chemical deposition method for thin films via thermal decomposition. |
Key Components | Precursor solution, atomizer, heated substrate, reactor chamber. |
Advantages | Scalability, uniformity, versatility, cost-effectiveness. |
Applications | Solar cells, sensors, catalysts, protective coatings. |
Challenges | Precursor selection, temperature control, droplet size consistency. |
Environmental Impact | Energy-efficient, eco-friendly solvents, modular design. |
Discover how spray pyrolysis can enhance your material production—contact our experts today!