SPS, or Spark Plasma Sintering, is an advanced sintering technique in materials science that enables the rapid consolidation of powders into dense, high-performance materials. It combines the application of pulsed electric current and uniaxial pressure, allowing for fast heating rates, precise control over sintering parameters, and the ability to process materials at lower temperatures compared to traditional methods. SPS is particularly advantageous for producing nanostructured ceramics, refractory metals, and composites with enhanced mechanical, thermal, and electrical properties. It minimizes grain growth and coarsening, making it ideal for creating fine-grained, high-density materials with superior performance.
Key Points Explained:
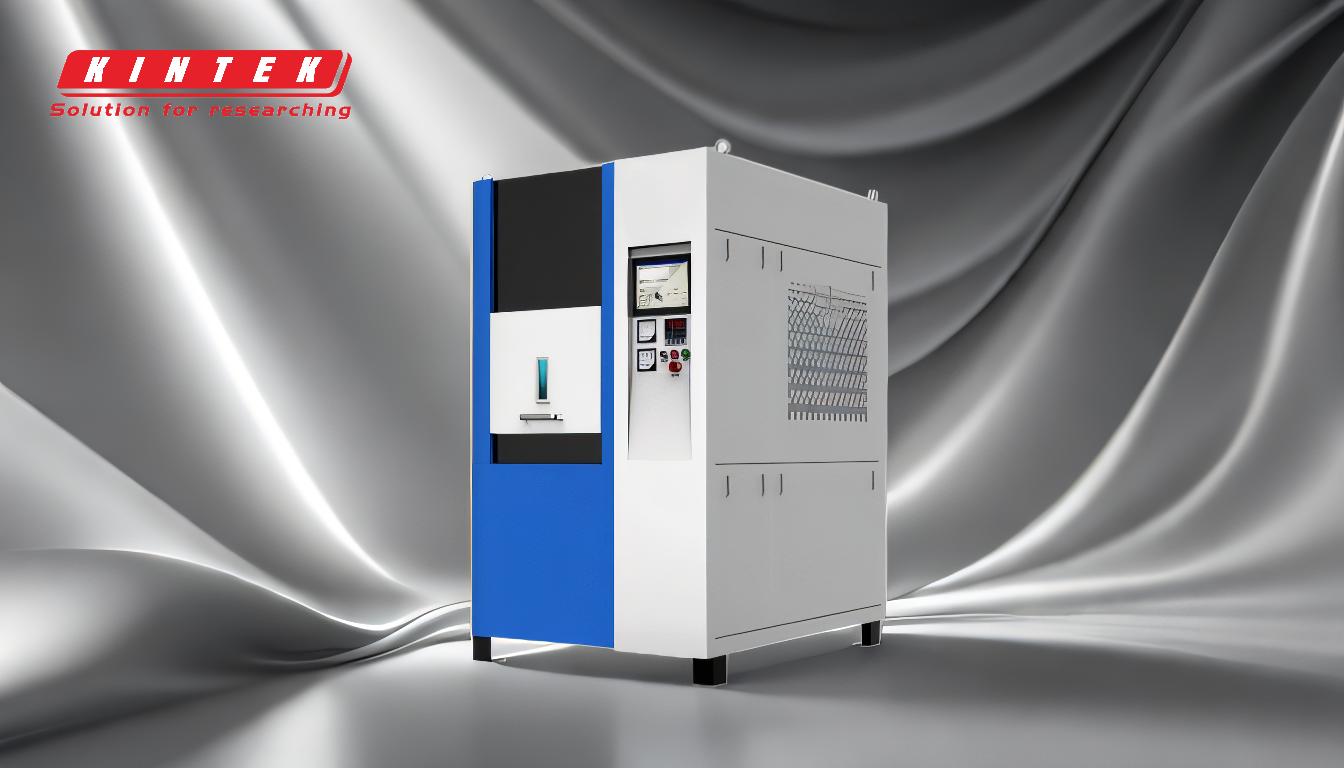
-
Definition and Mechanism of SPS:
- SPS stands for Spark Plasma Sintering, a sintering technique that uses pulsed electric current and mechanical pressure to consolidate powders into dense materials.
- The process involves applying a high-intensity electric current directly to the powder material, generating heat through Joule heating and enabling rapid densification.
- Simultaneously, uniaxial pressure is applied to facilitate particle rearrangement and bonding, resulting in high-density materials with minimal grain growth.
-
Key Advantages of SPS:
- Fast Heating Rates: SPS can achieve heating rates of up to 1000°C/min, significantly reducing sintering time compared to conventional methods.
- Low-Temperature Processing: SPS can operate at lower temperatures (e.g., 500–1000°C) while still achieving full densification, which is particularly beneficial for temperature-sensitive materials.
- Precise Control: The process allows for precise control over temperature, pressure, and heating rate, enabling tailored material properties.
- Minimized Grain Growth: The rapid sintering process prevents coarsening and grain growth, preserving nanostructures and resulting in fine-grained materials with enhanced mechanical properties.
-
Applications of SPS:
- Nanomaterials: SPS is widely used to prepare nanostructured ceramics, nanocomposites, and bulk amorphous alloys with high density and minimal defects.
- Refractory Metals: It is particularly effective for sintering high-melting-point metals like tungsten, vanadium, niobium, and their alloys, producing materials with finer grains and improved mechanical properties.
- Gradient Functional Materials: SPS enables the fabrication of materials with graded compositions and properties, which are challenging to achieve with traditional methods.
- High-Density Ceramics and Cermets: The technique is ideal for producing dense, fine-grained ceramics and cermets with superior strength, hardness, and wear resistance.
-
Performance Benefits:
- Enhanced Mechanical Properties: Materials produced via SPS exhibit higher strength, hardness, and flexural strength compared to those sintered using conventional methods.
- Improved Thermal and Electrical Properties: The fine-grained microstructure and high density achieved through SPS result in materials with excellent thermal conductivity and electrical performance.
- Preservation of Nanostructures: SPS prevents grain growth during sintering, allowing for the retention of intrinsic nanostructures and unique chemistries.
-
Comparison with Traditional Sintering Methods:
- Time Efficiency: SPS significantly reduces sintering time. For example, a comparative study showed that SPS sintering of WCl2-Co cemented carbide took only 1/26 of the time required for vacuum sintering.
- Material Quality: SPS produces materials with finer grains and higher density, leading to superior mechanical properties. In the same study, SPS-sintered materials exhibited a 13% increase in flexural strength compared to vacuum-sintered counterparts.
- Versatility: SPS can consolidate materials that are difficult or impossible to process using traditional methods, such as ultra-high-temperature ceramics like ZrC.
-
Future Potential and Research Directions:
- Advanced Material Development: SPS is increasingly being used to develop engineered structures and unique chemistries that are preserved during sintering, making it a key technology for advanced materials research.
- Synthesis of Novel Powders: The technique is also being explored for synthesizing powders that are challenging to obtain through conventional methods, such as ultra-high-temperature materials.
- Sustainability: The ability to process materials at lower temperatures and shorter times makes SPS a more energy-efficient and environmentally friendly sintering method.
In summary, SPS is a transformative technology in materials science, offering unparalleled control over sintering processes and enabling the production of high-performance materials with unique properties. Its applications span a wide range of materials, from nanostructured ceramics to refractory metals, and its advantages over traditional sintering methods make it a critical tool for advancing material science and engineering.
Summary Table:
Aspect | Details |
---|---|
Definition | SPS uses pulsed electric current and uniaxial pressure for rapid sintering. |
Key Advantages | Fast heating rates (up to 1000°C/min), low-temperature processing, precise control, minimized grain growth. |
Applications | Nanomaterials, refractory metals, gradient functional materials, high-density ceramics. |
Performance Benefits | Enhanced mechanical, thermal, and electrical properties; preservation of nanostructures. |
Comparison | Faster, finer grains, higher density, and versatility vs. traditional methods. |
Future Potential | Advanced material development, novel powder synthesis, sustainability. |
Unlock the potential of Spark Plasma Sintering for your materials—contact us today to learn more!