SPS (Spark Plasma Sintering) is an advanced sintering method that utilizes electrical current to rapidly heat and densify powdered materials. Unlike conventional sintering, SPS employs a pulsed direct current (DC) that passes through a conductive graphite die and, if applicable, the material itself. This technique enables extremely fast heating and cooling rates, short holding times, and densification at significantly lower temperatures compared to traditional methods. The process generates plasma at the particle surfaces, enhancing diffusion and bonding, which results in high-density materials with fine microstructures. SPS is particularly effective for ceramics, metals, and composites, offering precise control over material properties.
Key Points Explained:
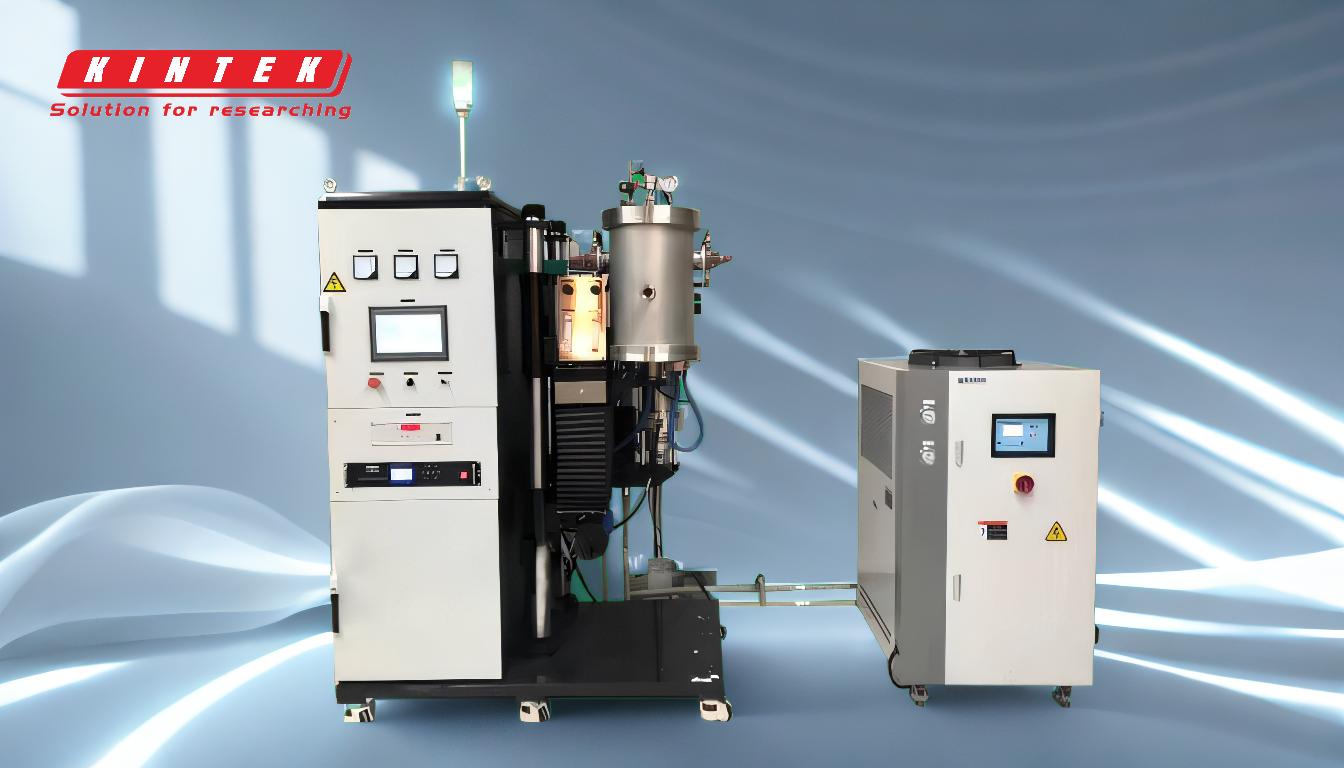
-
Principle of SPS Sintering:
- SPS uses an electrical current (pulsed DC) passed through a conductive graphite die and, in some cases, the material itself. This current acts as both an internal and external heat source, enabling rapid heating and cooling.
- The process generates plasma at the particle surfaces, which enhances atomic diffusion and bonding between particles. This leads to densification at much lower temperatures than conventional sintering methods.
-
Equipment and Setup:
- The SPS system consists of a graphite mold placed between upper and lower electrodes. The mold is pressurized using an oil pressure system, and the cavity is evacuated to create a vacuum.
- Once the desired vacuum is achieved, a pulsed current is applied directly to the mold and sample. This setup allows for precise control over temperature, pressure, and sintering time.
-
Advantages of SPS:
- Rapid Processing: SPS achieves high heating and cooling rates, reducing processing time significantly.
- Lower Sintering Temperatures: Densification occurs at temperatures several hundred degrees lower than conventional methods, preserving material properties.
- Enhanced Material Properties: The process results in materials with high density, fine microstructures, and improved mechanical properties.
- Versatility: SPS is suitable for a wide range of materials, including ceramics, metals, and composites.
-
Mechanism of Densification:
- The pulsed current activates the surface of the powder particles, causing partial discharges between pores. This generates plasma, which heats the particles and promotes diffusion.
- Simultaneously, the graphite mold transfers heat to the sample, causing it to shrink and increase in density. The process continues until the desired sintering temperature and maximum density are achieved.
-
Applications of SPS:
- SPS is widely used in the production of advanced ceramics, such as alumina, zirconia, and silicon carbide, due to its ability to achieve high density and fine grain sizes.
- It is also employed in the fabrication of metal matrix composites, nanocrystalline materials, and functionally graded materials, where precise control over microstructure and properties is critical.
-
Comparison with Conventional Sintering:
- Conventional sintering relies on external heating in a furnace, which results in slower heating rates and higher temperatures. This can lead to grain growth and reduced material performance.
- SPS, on the other hand, uses internal heating through electrical current, enabling faster processing and better control over material properties. This makes it a superior choice for advanced material fabrication.
By combining rapid heating, plasma generation, and precise control, SPS offers a unique and efficient approach to sintering, making it a valuable technique for producing high-performance materials.
Summary Table:
Aspect | Details |
---|---|
Principle | Uses pulsed DC current to generate plasma, enhancing diffusion and bonding. |
Equipment | Graphite mold, electrodes, vacuum system, and pulsed current generator. |
Advantages | Rapid processing, lower sintering temperatures, enhanced material properties. |
Applications | Advanced ceramics, metal matrix composites, nanocrystalline materials. |
Comparison | Faster, lower temperatures, and better control than conventional sintering. |
Learn how SPS can transform your material fabrication process—contact our experts today!