Sputtering is a widely used thin-film deposition technique in which atoms are ejected from a solid target material due to bombardment by high-energy ions, typically from an inert gas like argon. These ejected atoms then deposit onto a substrate to form a thin film. The process occurs in a vacuum chamber where a plasma is generated by applying a high voltage, causing gas atoms to ionize and accelerate toward the target. The collision of these ions with the target dislodges atoms, which then travel and adhere to the substrate, creating a uniform and durable coating. Sputtering is versatile, applicable to various materials, and is used in industries ranging from electronics to automotive.
Key Points Explained:
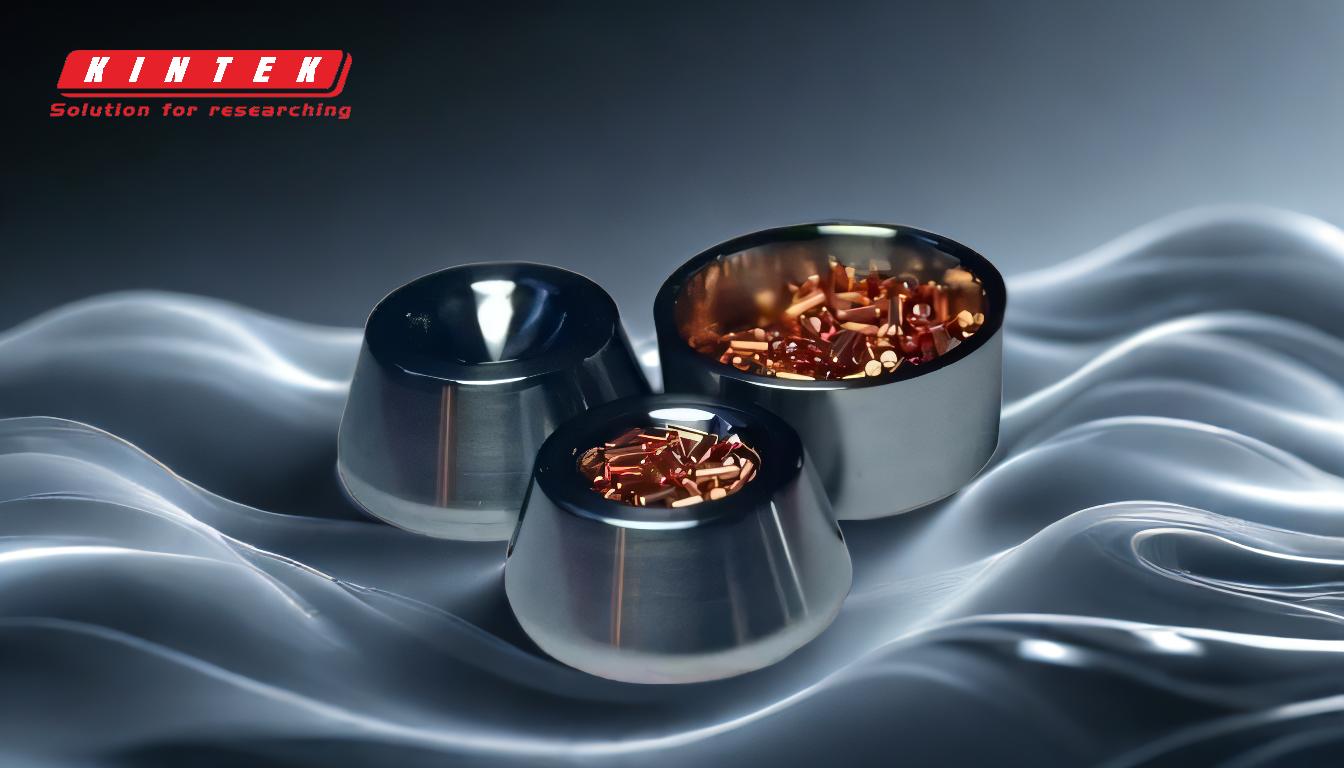
-
Basic Principle of Sputtering:
- Sputtering involves bombarding a target material with high-energy ions, typically from an inert gas like argon, in a vacuum chamber. These ions dislodge atoms from the target, which then deposit onto a substrate to form a thin film.
- The process relies on momentum transfer between the ions and the target atoms, ensuring efficient ejection and deposition.
-
Components of the Sputtering System:
- Vacuum Chamber: Provides a controlled environment to minimize contamination and ensure efficient plasma generation.
- Target Material: The source of atoms to be deposited, typically a metal or compound.
- Substrate: The surface onto which the thin film is deposited.
- Inert Gas (e.g., Argon): Ionized to create the plasma that bombards the target.
- Cathode and Anode: Electrodes used to generate the plasma and accelerate ions toward the target.
-
Plasma Generation and Ion Acceleration:
- A high voltage is applied between the cathode (target) and anode, creating a plasma in the presence of inert gas.
- The gas atoms become positively charged ions and are accelerated toward the negatively charged target.
- Upon collision, the ions transfer their energy to the target atoms, ejecting them into the gas phase.
-
Deposition Process:
- The ejected target atoms travel through the vacuum chamber and deposit onto the substrate.
- The deposited atoms form a thin, uniform film that adheres securely to the substrate.
- The process can be repeated to build up multiple layers of the desired material.
-
Types of Sputtering:
- DC Sputtering: Uses a direct current to generate the plasma, suitable for conductive materials.
- RF Sputtering: Uses radio frequency for non-conductive materials, preventing charge buildup on the target.
- Magnetron Sputtering: Enhances efficiency by using magnetic fields to confine electrons near the target, increasing ionization.
- Reactive Sputtering: Introduces reactive gases (e.g., oxygen or nitrogen) to form compound films (e.g., oxides or nitrides).
-
Advantages of Sputtering:
- Uniformity: Produces highly uniform and dense films.
- Versatility: Can deposit a wide range of materials, including metals, alloys, and compounds.
- Adhesion: Provides excellent adhesion between the film and substrate.
- Scalability: Suitable for large-scale industrial applications.
-
Applications of Sputtering:
- Electronics: Used in semiconductor manufacturing, thin-film transistors, and integrated circuits.
- Optics: Deposits anti-reflective and reflective coatings for lenses and mirrors.
- Automotive: Enhances durability and appearance of components through coatings.
- Decorative Coatings: Provides aesthetic finishes for consumer products.
- Energy: Used in solar cells and battery technologies.
-
Historical Context:
- Sputtering was first commercially used by Thomas Edison in 1904 to apply thin metal layers to wax phonograph recordings.
- Over time, the technique has evolved, with advancements like magnetron sputtering improving efficiency and expanding applications.
-
Challenges and Considerations:
- Cost: Requires expensive equipment and high vacuum conditions.
- Rate Control: Deposition rates can be slower compared to other techniques.
- Material Limitations: Some materials may be difficult to sputter due to low sputter yields or reactivity.
-
Future Trends:
- Development of high-power impulse magnetron sputtering (HiPIMS) for improved film quality and adhesion.
- Integration with other deposition techniques for hybrid processes.
- Exploration of new materials and applications in nanotechnology and renewable energy.
By understanding these key points, a purchaser can evaluate the suitability of sputtering for their specific needs, considering factors like material compatibility, desired film properties, and cost-effectiveness.
Summary Table:
Aspect | Details |
---|---|
Basic Principle | Bombardment of target material by high-energy ions in a vacuum chamber. |
Key Components | Vacuum chamber, target material, substrate, inert gas, cathode, and anode. |
Types of Sputtering | DC, RF, Magnetron, and Reactive Sputtering. |
Advantages | Uniformity, versatility, excellent adhesion, and scalability. |
Applications | Electronics, optics, automotive, decorative coatings, and energy sectors. |
Challenges | High cost, slower deposition rates, and material limitations. |
Future Trends | HiPIMS, hybrid processes, and new materials for nanotechnology and energy. |
Interested in sputtering for your applications? Contact our experts today to learn more!