A steel induction furnace is a type of electric furnace used for melting and heating steel and other metals. It operates on the principle of electromagnetic induction, where an alternating current (AC) passes through a coil, generating a magnetic field that induces eddy currents within the metal. These eddy currents produce heat, melting the metal. The furnace is known for its efficiency, precise temperature control, and ability to produce uniform compositions. Key components include the inductor, furnace body, power supply, capacitor, and control system. Advanced features like IGBT induction furnace technology enhance performance, offering better energy efficiency and control.
Key Points Explained:
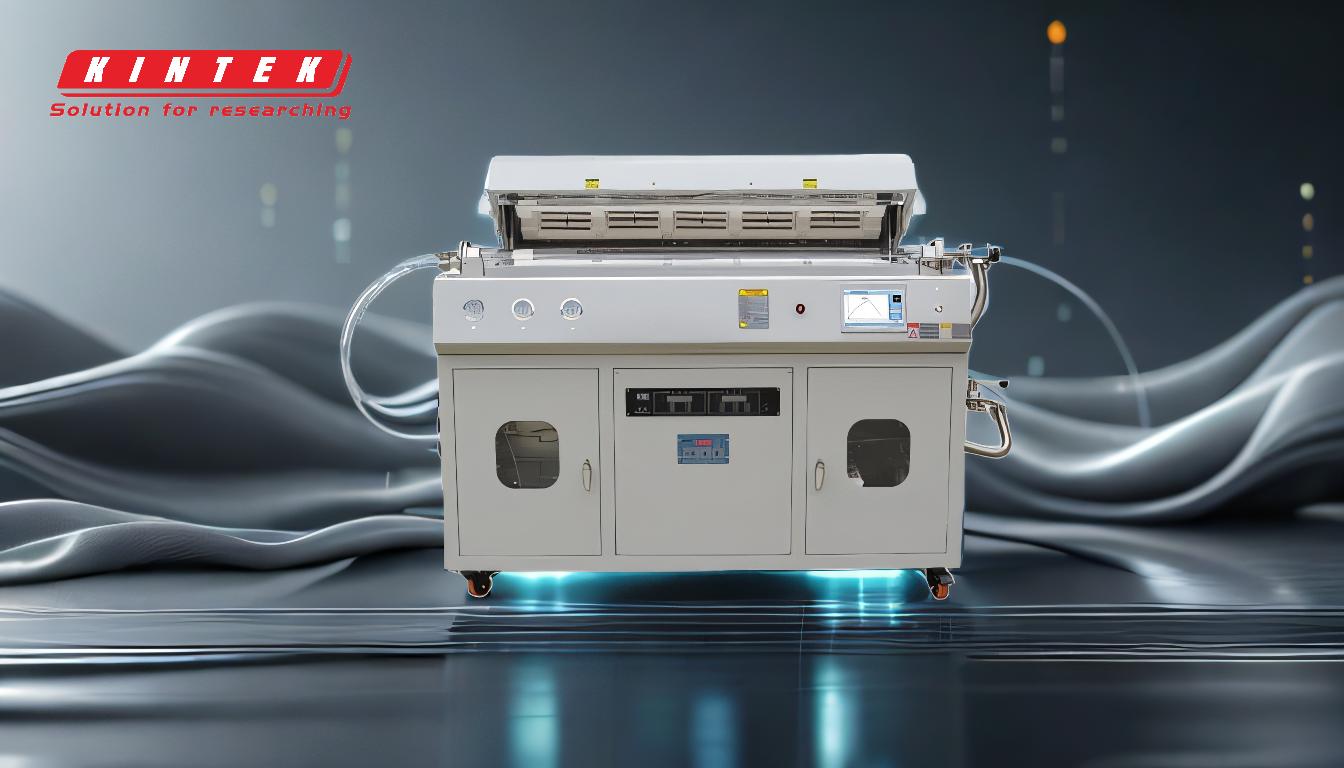
-
Working Principle:
- The steel induction furnace operates on electromagnetic induction. An alternating current passes through an induction coil, creating a magnetic field. This field induces eddy currents within the metal, generating heat and melting it. This method ensures uniform heating and precise temperature control, which is crucial for producing high-quality steel.
-
Key Components:
- Inductor (Coil): The coil generates the magnetic field necessary for induction heating. It is typically made of copper and is water-cooled to prevent overheating.
- Furnace Body: This is the structure that houses the metal to be melted. It is designed to withstand high temperatures and is often lined with refractory materials.
- Power Supply: Provides the alternating current needed for induction. Modern furnaces often use IGBT induction furnace technology for better efficiency and control.
- Capacitor: Helps in tuning the power supply to the optimal frequency for efficient induction heating.
- Control System: Manages the operation of the furnace, including temperature control, power regulation, and safety features.
-
Types of Induction Furnaces:
- Coreless Induction Furnace: Commonly used for melting steel, it has no core and relies solely on the induction coil for heating.
- Channel Induction Furnace: Features a core and is used for holding and superheating molten metal.
- Vacuum Induction Furnace: Operates under vacuum conditions, ideal for melting high-purity metals and alloys.
-
Advantages:
- Efficiency: Induction furnaces are highly efficient, converting electrical energy directly into heat with minimal losses.
- Precision: They offer precise temperature control, which is essential for producing high-quality steel with consistent properties.
- Uniformity: The induction process ensures uniform heating, leading to a homogeneous melt.
- Environmental Benefits: Induction furnaces produce fewer emissions compared to traditional fuel-based furnaces, making them more environmentally friendly.
-
Applications:
- Steel Production: Widely used in the steel industry for melting and refining steel.
- Foundries: Used for casting various metal parts and components.
- Alloy Production: Ideal for producing alloys with precise compositions.
- Research and Development: Used in labs for developing new materials and testing metal properties.
-
Maintenance and Operation:
- Ease of Maintenance: Modern induction furnaces, especially those with IGBT induction furnace technology, are designed for easy maintenance. Components like the induction coil and power supply are modular and can be replaced without extensive downtime.
- Safety Features: These furnaces come with comprehensive protection systems, including over-voltage, over-current, and under-voltage protections, ensuring safe and reliable operation.
- User-Friendly: High integrated circuit designs simplify debugging, operation, and learning, making it easier for operators to manage the furnace.
-
Technological Advancements:
- IGBT Technology: The use of IGBT induction furnace technology has revolutionized induction furnaces, offering better energy efficiency, faster response times, and improved control over the melting process.
- Automation: Advanced control systems with automatic frequency scanning and repeated starting functions ensure smooth and stable operation, reducing the need for manual intervention.
- Energy Efficiency: Constant power circuit control systems adjust voltage and current automatically based on the furnace charge, optimizing energy use and reducing operational costs.
In summary, a steel induction furnace is a versatile and efficient tool for melting and heating steel, offering precise control, uniformity, and environmental benefits. With advancements like IGBT induction furnace technology, these furnaces continue to evolve, providing even greater efficiency and ease of use.
Summary Table:
Aspect | Details |
---|---|
Working Principle | Electromagnetic induction with eddy currents for uniform heating. |
Key Components | Inductor, furnace body, power supply, capacitor, control system. |
Types | Coreless, channel, and vacuum induction furnaces. |
Advantages | High efficiency, precise temperature control, uniformity, eco-friendly. |
Applications | Steel production, foundries, alloy production, R&D. |
Maintenance | Easy maintenance, modular components, advanced safety features. |
Technological Advances | IGBT technology, automation, energy efficiency improvements. |
Ready to enhance your metal melting process? Contact us today to learn more about steel induction furnaces!