To determine which joining technique—welding, brazing, or soldering—is stronger, it is essential to understand the fundamental differences in their processes, the temperatures involved, and the resulting joint strength. Brazing and soldering both use filler metals to join components without melting the base materials, but brazing occurs at higher temperatures (above 840°F) compared to soldering (below 840°F). Welding, on the other hand, involves melting the base materials to form a joint. While brazed joints are as strong as the base metals and are widely used in industries like cookware, automotive, and HVAC systems, welding typically produces the strongest joints due to the fusion of base materials. However, welding can cause thermal distortion, whereas brazing offers a more uniform heating process, reducing the risk of warping or distortion.
Key Points Explained:
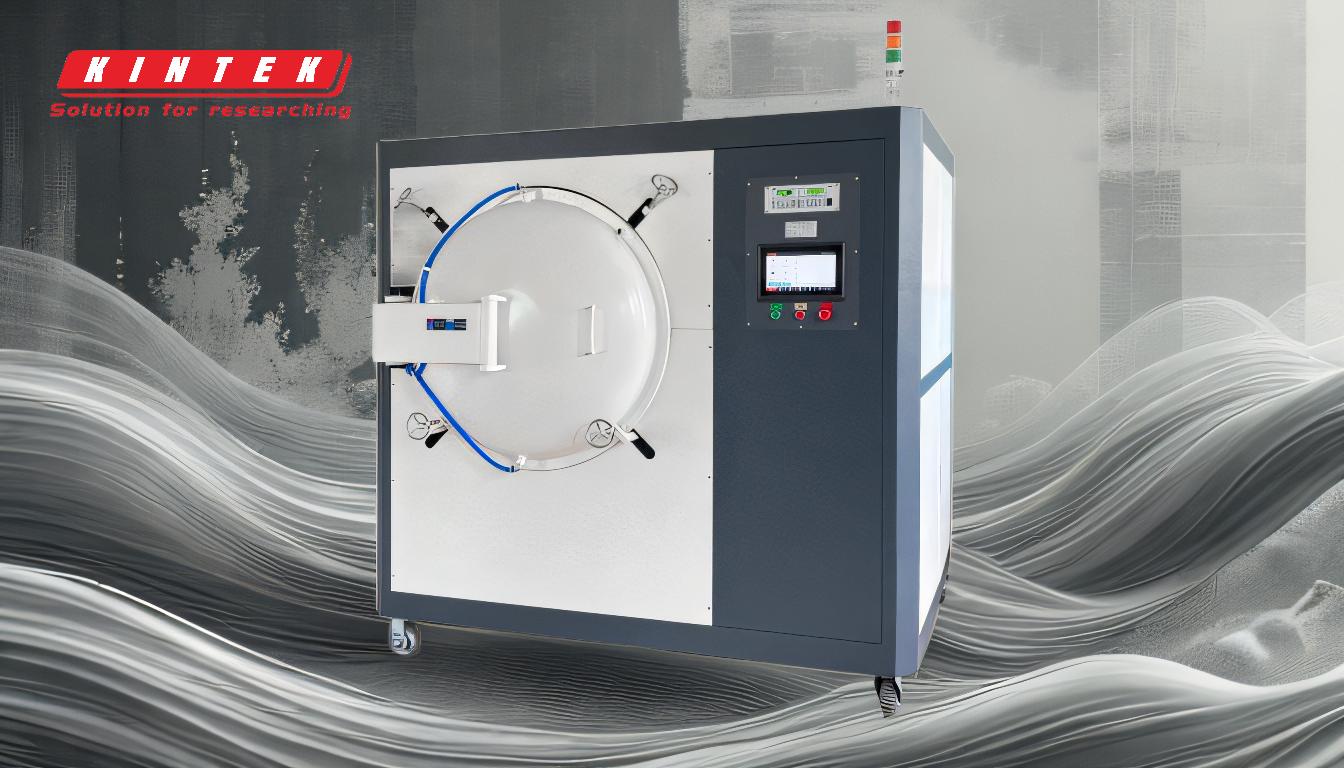
-
Temperature Differences:
- Brazing: Occurs at higher temperatures, typically above 840°F. This high-temperature process allows the filler metal to flow into the joint by capillary action, creating a strong bond.
- Soldering: Uses lower temperatures, below 840°F, making it suitable for delicate materials or components that cannot withstand high heat.
- Welding: Involves melting the base materials, requiring even higher temperatures than brazing. This process creates a joint by fusing the materials together.
-
Joint Strength:
- Brazing: Produces joints that are as strong as the base metals. The filler metal used in brazing bonds well with the base materials, resulting in a durable joint.
- Soldering: Creates weaker joints compared to brazing and welding. The lower temperatures and softer filler metals used in soldering make it less suitable for high-strength applications.
- Welding: Typically produces the strongest joints because it involves the fusion of base materials. The resulting joint is often as strong as or stronger than the original materials.
-
Thermal Effects:
- Brazing: Produces less thermal distortion compared to welding. The uniform heating process in brazing avoids localized high temperatures that can cause warping or distortion in the base metal.
- Soldering: Also minimizes thermal distortion due to the lower temperatures involved. This makes soldering ideal for delicate components.
- Welding: Can cause significant thermal distortion, especially in thin or heat-sensitive materials, due to the high temperatures and localized heat input.
-
Applications:
- Brazing: Widely used in industries such as cookware, automotive, and HVAC systems due to its strength and ability to join dissimilar metals.
- Soldering: Commonly used in electronics, plumbing, and jewelry making, where lower temperatures and precision are required.
- Welding: Preferred for structural applications, heavy machinery, and construction, where the highest joint strength is necessary.
-
Material Compatibility:
- Brazing: Can join dissimilar metals effectively, making it versatile for various industrial applications.
- Soldering: Best suited for joining similar or compatible metals, especially in low-stress applications.
- Welding: Requires compatible base materials to achieve a strong joint. It is less versatile for joining dissimilar metals compared to brazing.
In conclusion, while brazing offers strong joints with minimal thermal distortion and is suitable for a wide range of applications, welding generally produces the strongest joints due to the fusion of base materials. Soldering, on the other hand, is best for low-strength applications where precision and low temperatures are critical. The choice between welding, brazing, or soldering depends on the specific requirements of the application, including the desired joint strength, material compatibility, and thermal considerations.
Summary Table:
Aspect | Welding | Brazing | Soldering |
---|---|---|---|
Temperature | Highest (melts base materials) | Above 840°F | Below 840°F |
Joint Strength | Strongest (fuses base materials) | As strong as base metals | Weaker, suitable for low-strength |
Thermal Effects | High risk of distortion | Minimal distortion | Minimal distortion |
Applications | Structural, heavy machinery | Cookware, automotive, HVAC | Electronics, plumbing, jewelry |
Material Compatibility | Requires compatible materials | Can join dissimilar metals | Best for similar or compatible metals |
Still unsure which joining technique is best for your project? Contact our experts today for personalized advice!