In Physical Vapor Deposition (PVD), the substrate is the material or surface onto which a thin film or coating is deposited. The substrate plays a crucial role in determining the quality, adhesion, and performance of the deposited layer. It must be compatible with the vacuum environment and often undergoes pre-treatment to ensure proper bonding and surface preparation. Common substrate materials include metals, ceramics, plastics, and glass, each chosen based on the intended application and desired properties of the final product. The substrate's surface condition, crystallographic orientation, and compatibility with the coating material are critical factors in achieving optimal results.
Key Points Explained:
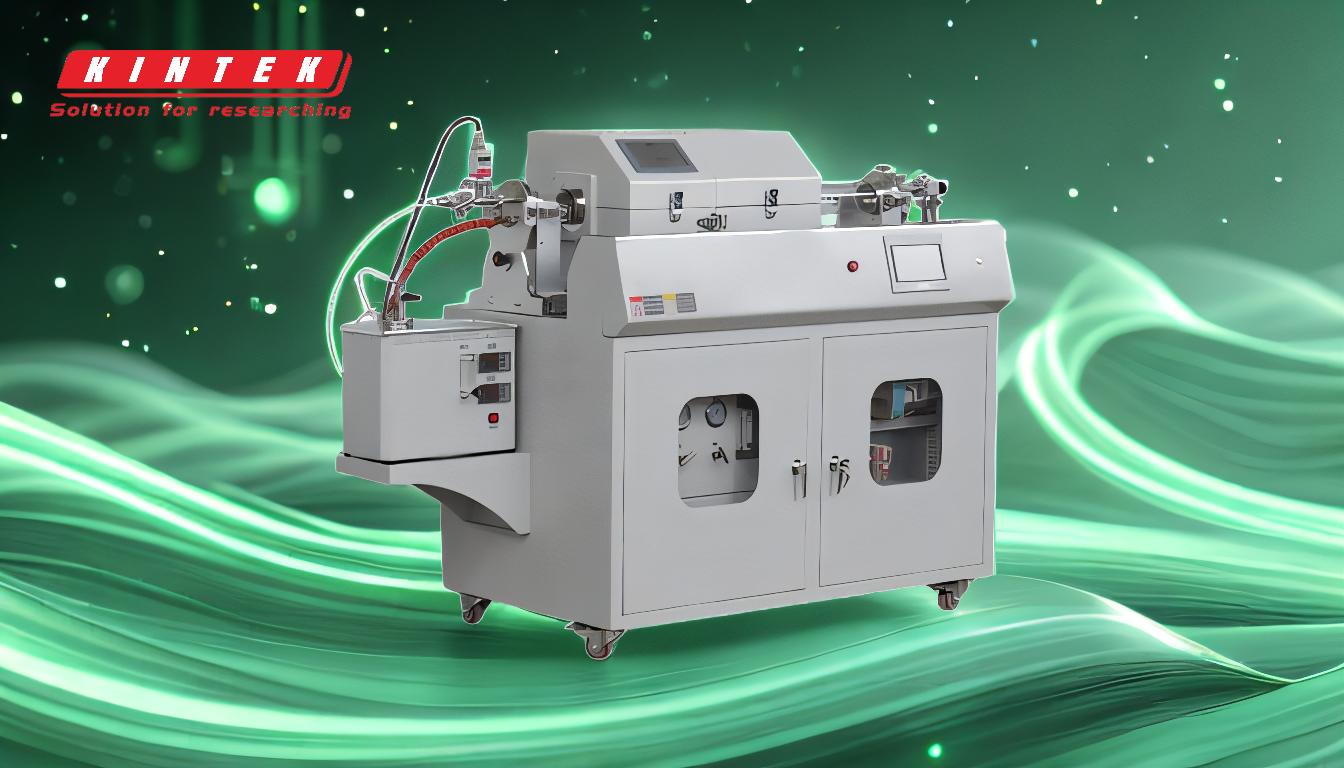
-
Definition of Substrate in PVD:
- The substrate is the base material or surface onto which the PVD coating is applied. It serves as the foundation for the deposition process, and its properties significantly influence the quality and performance of the final coating.
- Example: In aerospace applications, substrates like titanium or stainless steel are coated with materials such as TiN or DLC to enhance durability and resistance to wear.
-
Role of the Substrate:
- The substrate acts as a catalyst for the deposition process, providing a surface for the coating material to nucleate and grow.
- Example: In diamond-like carbon (DLC) coatings, a silicon substrate is often used because its crystallographic orientation facilitates the growth of carbon atoms.
-
Pre-Treatment of Substrates:
- Substrates are often pre-treated to ensure proper adhesion and compatibility with the PVD process. Common pre-treatment methods include cleaning, electroplating, or applying organic coatings.
- Example: Tool steels may be electroplated with nickel or chromium before PVD coating to improve surface uniformity and adhesion.
-
Common Substrate Materials:
- Substrates for PVD are selected based on their compatibility with the coating material and the intended application. Common materials include:
- Metals (e.g., stainless steel, aluminum, titanium)
- Ceramics (e.g., glass, zirconia)
- Plastics (e.g., ABS, nylon)
- Example: Glass substrates are often coated with anti-reflective or scratch-resistant layers for optical applications.
- Substrates for PVD are selected based on their compatibility with the coating material and the intended application. Common materials include:
-
Vacuum Compatibility:
- The substrate must be vacuum-compatible, meaning it can withstand the low-pressure environment of the PVD process without degrading or releasing contaminants.
- Example: Plastics like ABS are treated to ensure they do not outgas or deform under vacuum conditions.
-
Surface Preparation:
- Proper surface preparation is critical for achieving high-quality coatings. This includes cleaning, polishing, and sometimes roughening the surface to enhance adhesion.
- Example: Silicon substrates used for diamond growth are cleaned with abrasive diamond powder to create an ideal surface for deposition.
-
Application-Specific Substrates:
- The choice of substrate depends on the application. For instance:
- Aerospace components often use titanium or stainless steel substrates.
- Automotive parts may use tool steels or aluminum.
- Electronics might use silicon or gold-coated substrates.
- Example: Gold-coated substrates are used in aerospace electronics for their excellent conductivity and corrosion resistance.
- The choice of substrate depends on the application. For instance:
-
Interaction with Coating Materials:
- The substrate material must be compatible with the coating material to ensure proper bonding and performance. This includes matching thermal expansion coefficients and chemical reactivity.
- Example: Titanium substrates are often paired with TiN or TiAlN coatings due to their chemical compatibility and similar thermal properties.
-
Substrate Impact on Coating Properties:
- The substrate's properties, such as hardness, thermal conductivity, and surface roughness, directly affect the performance of the PVD coating.
- Example: A polished steel substrate will result in a smoother and more uniform coating compared to a rough surface.
-
Future Trends in Substrate Materials:
- Advances in substrate materials and pre-treatment techniques are expanding the range of applications for PVD coatings. New materials and composites are being developed to meet the demands of emerging technologies.
- Example: The use of advanced ceramics and hybrid materials as substrates is increasing in industries like renewable energy and medical devices.
By understanding the role of the substrate in PVD, manufacturers can select the appropriate materials and pre-treatment methods to achieve coatings with superior performance and durability. This knowledge is essential for optimizing the PVD process and meeting the specific requirements of various industries.
Summary Table:
Key Aspect | Details |
---|---|
Definition | Base material for PVD coating; influences quality and performance. |
Role | Acts as a catalyst for deposition, enabling nucleation and growth. |
Pre-Treatment | Cleaning, electroplating, or organic coatings for better adhesion. |
Common Materials | Metals (e.g., titanium), ceramics (e.g., glass), plastics (e.g., ABS). |
Vacuum Compatibility | Must withstand low-pressure environments without degrading. |
Surface Preparation | Cleaning, polishing, or roughening to enhance adhesion. |
Application-Specific | Aerospace: titanium; Automotive: tool steels; Electronics: silicon. |
Interaction with Coatings | Compatibility in thermal expansion and chemical reactivity is critical. |
Impact on Coating | Hardness, thermal conductivity, and surface roughness affect performance. |
Future Trends | Advanced ceramics and hybrid materials for emerging technologies. |
Optimize your PVD process with the right substrate—contact our experts today!