Hydraulic presses are widely used in various industries for applications such as molding, forging, and compression. However, there are several alternatives to hydraulic presses that can be used depending on the specific requirements of the task. These alternatives include mechanical presses, pneumatic presses, electric presses, and servo presses. Each alternative has its own set of advantages and disadvantages, making them suitable for different applications. The choice of an alternative depends on factors such as the required force, precision, speed, and cost. Below, we will explore these alternatives in detail, highlighting their key features and applications.
Key Points Explained:
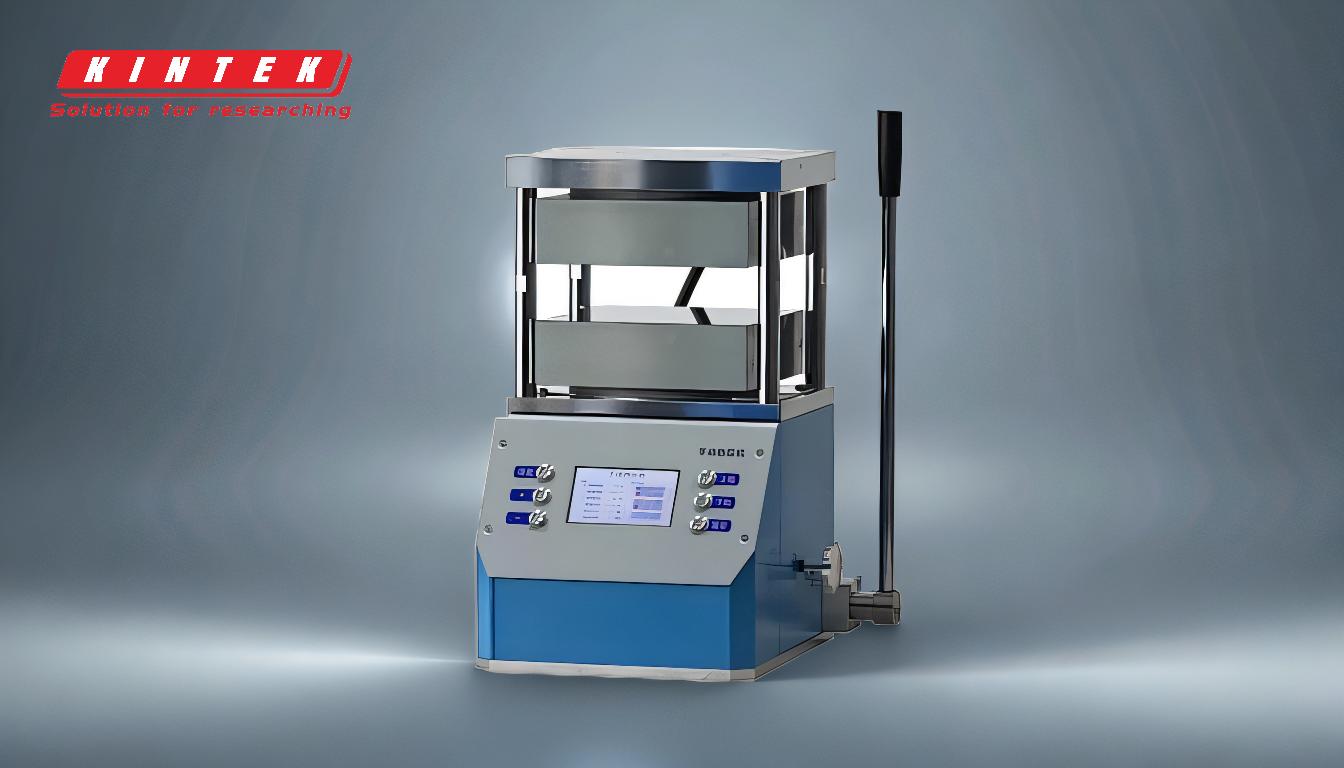
-
Mechanical Presses:
- How They Work: Mechanical presses use a motor to drive a flywheel, which stores energy. This energy is then transferred to a ram through a mechanical linkage, such as a crank or eccentric gear.
-
Advantages:
- High speed and efficiency.
- Consistent force application.
- Suitable for high-volume production.
-
Disadvantages:
- Limited control over force and speed.
- Higher maintenance due to mechanical wear and tear.
- Applications: Commonly used in stamping, punching, and blanking operations.
-
Pneumatic Presses:
- How They Work: Pneumatic presses use compressed air to generate force. The air pressure is controlled to move a piston, which in turn moves the ram.
-
Advantages:
- Clean and easy to operate.
- Precise control over force and speed.
- Lower maintenance compared to hydraulic and mechanical presses.
-
Disadvantages:
- Limited force compared to hydraulic presses.
- Requires a constant supply of compressed air.
- Applications: Ideal for light-duty applications such as assembly, clamping, and light pressing.
-
Electric Presses:
- How They Work: Electric presses use an electric motor to generate force. The motor drives a screw or a belt, which moves the ram.
-
Advantages:
- High precision and control.
- Energy-efficient.
- Quiet operation.
-
Disadvantages:
- Higher initial cost.
- Limited force compared to hydraulic presses.
- Applications: Suitable for applications requiring high precision, such as electronics assembly and medical device manufacturing.
-
Servo Presses:
- How They Work: Servo presses use a servo motor to control the movement of the ram. The servo motor provides precise control over the position, speed, and force of the ram.
-
Advantages:
- Extremely high precision and control.
- Programmable for complex operations.
- Energy-efficient.
-
Disadvantages:
- High initial cost.
- Requires advanced control systems.
- Applications: Ideal for high-precision applications such as fine blanking, coining, and forming.
-
Hydraulic Hot Press Machine:
- How They Work: A hydraulic hot press machine uses hydraulic fluid to generate force, combined with heating elements to apply heat during the pressing process.
-
Advantages:
- High force capability.
- Ability to apply heat, making it suitable for processes like laminating and molding.
- Versatile for various materials.
-
Disadvantages:
- Slower operation compared to mechanical presses.
- Higher maintenance due to hydraulic system complexity.
- Applications: Used in applications requiring both pressure and heat, such as composite material molding and plastic lamination.
-
Manual Presses:
- How They Work: Manual presses rely on human force to generate pressure. They typically use a lever or screw mechanism to apply force.
-
Advantages:
- Simple and cost-effective.
- No need for power sources.
-
Disadvantages:
- Limited force and precision.
- Labor-intensive.
- Applications: Suitable for small-scale or low-force applications, such as jewelry making or small part assembly.
-
Hydraulic vs. Alternatives:
- Force and Precision: Hydraulic presses generally provide higher force and better precision compared to most alternatives, but electric and servo presses can offer superior precision for specific applications.
- Speed: Mechanical presses are faster, while hydraulic presses are slower but more versatile.
- Cost: Hydraulic presses are often more expensive to maintain due to the complexity of the hydraulic system, whereas pneumatic and electric presses may have lower maintenance costs.
- Application Suitability: The choice between hydraulic presses and their alternatives depends on the specific requirements of the application, such as the need for heat, force, precision, and speed.
In conclusion, while hydraulic presses are highly versatile and powerful, there are several alternatives available that may be more suitable depending on the specific needs of the application. Mechanical presses offer high speed and efficiency, pneumatic presses provide clean and precise operation, electric presses are energy-efficient and precise, and servo presses offer the highest level of control and precision. Additionally, manual presses are a cost-effective solution for low-force applications. Understanding the strengths and limitations of each type of press is crucial in selecting the right equipment for your needs.
Summary Table:
Type of Press | How It Works | Advantages | Disadvantages | Applications |
---|---|---|---|---|
Mechanical | Uses a motor-driven flywheel and mechanical linkage to transfer energy to the ram. | High speed, consistent force, suitable for high-volume production. | Limited control, higher maintenance due to mechanical wear. | Stamping, punching, blanking. |
Pneumatic | Uses compressed air to move a piston and ram. | Clean, precise control, lower maintenance. | Limited force, requires constant compressed air supply. | Light-duty tasks like assembly, clamping, and light pressing. |
Electric | Uses an electric motor to drive a screw or belt, moving the ram. | High precision, energy-efficient, quiet operation. | Higher initial cost, limited force compared to hydraulic. | Electronics assembly, medical device manufacturing. |
Servo | Uses a servo motor for precise control of ram position, speed, and force. | Extremely high precision, programmable, energy-efficient. | High initial cost, requires advanced control systems. | Fine blanking, coining, forming. |
Hydraulic Hot Press | Uses hydraulic fluid and heating elements for force and heat application. | High force, versatile, suitable for heat-based processes. | Slower operation, higher maintenance due to hydraulic system complexity. | Composite material molding, plastic lamination. |
Manual | Relies on human force via levers or screws. | Simple, cost-effective, no power source required. | Limited force and precision, labor-intensive. | Small-scale tasks like jewelry making or small part assembly. |
Need help choosing the right press for your application? Contact our experts today for personalized advice!