A tube furnace is a versatile and efficient heating device, but it has limitations, particularly when dealing with heavy raw materials or processes requiring high-temperature, short residence times. Alternatives to a tube furnace depend on the specific application and requirements. For instance, a muffle furnace is a suitable alternative for calcination in air, as it ensures full contact with air for complete calcination. Other alternatives include box furnaces, rotary kilns, and crucible furnaces, each offering unique advantages depending on the material and process requirements. Understanding the strengths and weaknesses of a tube furnace helps in selecting the most appropriate alternative for specific use cases.
Key Points Explained:
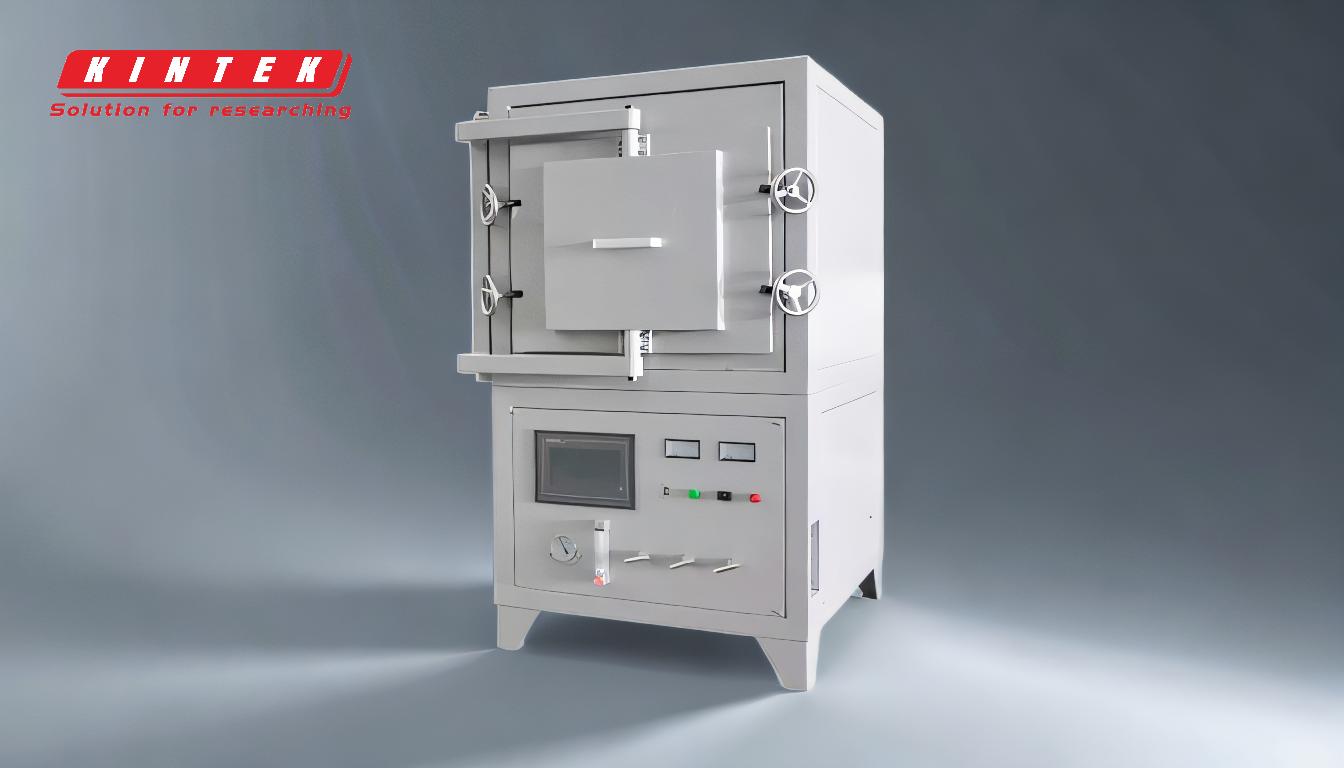
-
Advantages of a Tube Furnace
- Uniform Temperature Distribution: The adjustable heating devices arranged around the container ensure even heat distribution, which is crucial for consistent results in experiments or industrial processes.
- Space-Saving Design: Tube furnaces are compact and highly efficient, making them ideal for laboratories or facilities with limited space.
- Ease of Operation: Advanced control systems enable intelligent operation and remote monitoring, simplifying the user experience.
- Low Energy Consumption: Over time, the energy efficiency of tube furnaces can lead to significant cost savings.
-
Disadvantages of a Tube Furnace
- Limited Applicability to Heavy Raw Materials: Tube furnaces struggle with heavy raw materials, leading to issues like coking, which reduces production efficiency and increases maintenance costs.
- High-Temperature Requirements: The need for high temperatures and short residence times increases the thermal stress on furnace tubes, necessitating specialized materials like oil-resistant high-temperature alloy pipes.
-
Materials for Furnace Tubes
- Tube furnaces can use various materials for their furnace tubes, including heat-resistant steel, quartz glass, and ceramic tubes. The choice of material depends on the temperature range and chemical compatibility with the process.
-
When to Use a Tube Furnace
- Tube furnaces are ideal for processes requiring protective gas environments or programmed temperature control. However, for calcination in air, a muffle furnace is often a better choice due to its ability to ensure full air contact.
-
Alternatives to a Tube Furnace
- Muffle Furnace: Best for calcination in air, ensuring complete oxidation or decomposition of materials.
- Box Furnace: Suitable for batch processes and larger samples, offering uniform heating in a static environment.
- Rotary Kiln: Ideal for continuous processes and materials requiring tumbling or mixing during heating.
- Crucible Furnace: Useful for melting or heating small quantities of materials in a controlled environment.
-
Choosing the Right Alternative
- The choice of an alternative to a tube furnace depends on factors like the type of material, required temperature, process duration, and the need for protective atmospheres. For example, if the process involves heavy raw materials or requires high-temperature, short-duration heating, a rotary kiln or box furnace might be more suitable.
By evaluating the specific requirements of your application, you can determine the most appropriate alternative to a tube furnace, ensuring optimal performance and efficiency.
Summary Table:
Alternative | Best Use Case |
---|---|
Muffle Furnace | Calcination in air, ensuring complete oxidation or decomposition of materials. |
Box Furnace | Batch processes and larger samples, offering uniform heating in a static environment. |
Rotary Kiln | Continuous processes, ideal for materials requiring tumbling or mixing during heating. |
Crucible Furnace | Melting or heating small quantities of materials in a controlled environment. |
Need help choosing the right furnace for your application? Contact our experts today for personalized advice!