Furnace brazing is a highly versatile and precise joining process used across various industries to create strong, leak-tight, and reliable bonds between metal components. It involves heating assemblies to a specific temperature in a controlled environment, such as a vacuum brazing furnace, to melt a filler metal without melting the base materials. This process is particularly advantageous for applications requiring high precision, cleanliness, and minimal oxidation. Key industries benefiting from furnace brazing include aerospace, automotive, medical, electronics, and energy, where it is used to join complex components like heat exchangers, turbine blades, and medical implants. The controlled environment of a vacuum furnace ensures high-quality results, making it indispensable for advanced manufacturing and research.
Key Points Explained:
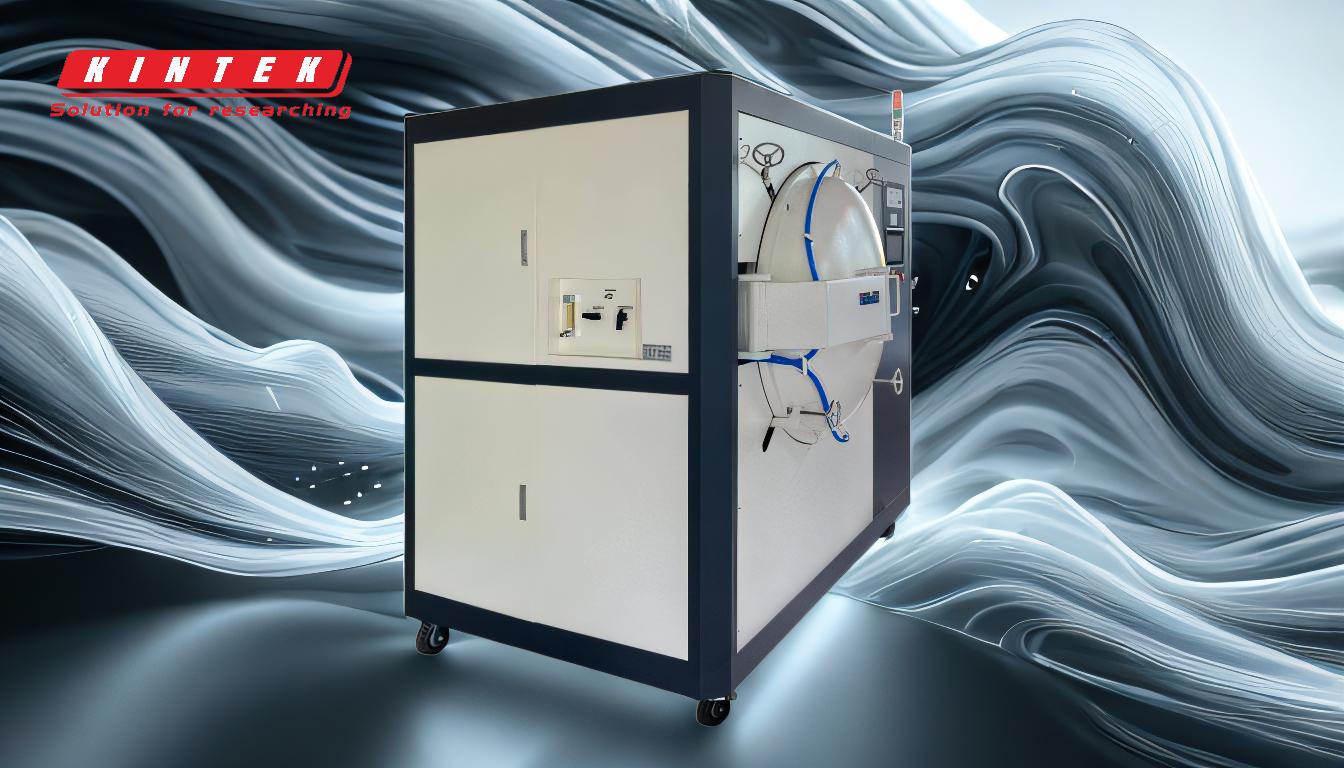
-
Aerospace Industry Applications:
- Furnace brazing is critical in the aerospace sector for joining lightweight and high-strength materials like titanium alloys and nickel-based superalloys.
- Applications include aircraft components such as engine parts, heat exchangers, and structural assemblies.
- The process ensures strong, durable, and oxidation-free joints, which are essential for the performance and safety of aerospace systems.
-
Automotive Industry Applications:
- In the automotive sector, furnace brazing is used to join components like gears, bearings, and engine parts.
- The process enhances the hardness, wear resistance, and durability of these components, improving overall vehicle performance.
- It is also used in the production of heating and cooling assemblies, such as radiators and air conditioning systems.
-
Medical and Pharmaceutical Applications:
- Furnace brazing is widely used in the medical industry to produce biocompatible and sterile devices like orthopedic implants, surgical instruments, and diagnostic equipment.
- The controlled environment of a vacuum furnace ensures that the joints are free from contaminants, making them suitable for medical applications.
- This process is also used in the production of micro-channel heat exchangers for medical devices.
-
Electronics and Semiconductor Applications:
- In the electronics industry, furnace brazing is used for processes like diffusion bonding and sintering in the production of high-performance electronic components.
- It is particularly useful for joining materials with different thermal expansion coefficients, such as ceramics and metals.
- Applications include sensors, semiconductor components, and electronic packaging.
-
Energy and Power Generation Applications:
- Furnace brazing is essential in the energy sector for producing components like turbine blades, heat exchangers, and nuclear reactor parts.
- The process ensures high temperature and corrosion resistance, which are critical for the longevity and efficiency of energy systems.
- It is also used in the production of components for renewable energy systems, such as solar panels and wind turbines.
-
Tool and Die Applications:
- In the tool and die industry, furnace brazing is used to join molds, dies, and cutting tools.
- The process enhances the hardness and wear resistance of these tools, extending their lifespan and improving manufacturing efficiency.
- It is also used for repairing and refurbishing worn-out tools.
-
Research and Development Applications:
- Furnace brazing is widely used in research and development to study material behavior under controlled thermal conditions.
- It enables the development of new materials and joining techniques for advanced applications.
- The process is also used in prototyping and testing new designs for various industries.
-
Advantages of Using a Vacuum Brazing Furnace:
- A vacuum brazing furnace provides a clean, oxidation-free environment, ensuring high-quality joints.
- It allows for precise temperature control, which is essential for joining materials with different melting points.
- The process is scalable and adaptable, making it suitable for both small-scale and large-scale production.
In summary, furnace brazing is a critical process in modern manufacturing, offering unparalleled precision, reliability, and versatility. Its applications span a wide range of industries, from aerospace and automotive to medical and energy, making it an indispensable tool for advanced manufacturing and research. The use of a vacuum brazing furnace further enhances the quality and consistency of the brazing process, ensuring that the final products meet the highest standards of performance and durability.
Summary Table:
Industry | Applications |
---|---|
Aerospace | Engine parts, heat exchangers, structural assemblies |
Automotive | Gears, bearings, radiators, air conditioning systems |
Medical | Orthopedic implants, surgical instruments, diagnostic equipment |
Electronics | Sensors, semiconductor components, electronic packaging |
Energy | Turbine blades, heat exchangers, nuclear reactor parts |
Tool and Die | Molds, dies, cutting tools |
Research & Development | Material behavior studies, prototyping, new designs |
Learn how furnace brazing can enhance your manufacturing process—contact our experts today!