Injection moulding machines are widely used in manufacturing to produce a vast array of plastic products. They are essential in industries such as automotive, packaging, consumer goods, and electronics due to their ability to produce high volumes of complex and precise parts efficiently. The process involves injecting molten plastic into a press mold, which then cools and solidifies into the desired shape. This method is cost-effective, scalable, and capable of producing items ranging from small components like bottle caps to larger items like automotive parts and furniture.
Key Points Explained:
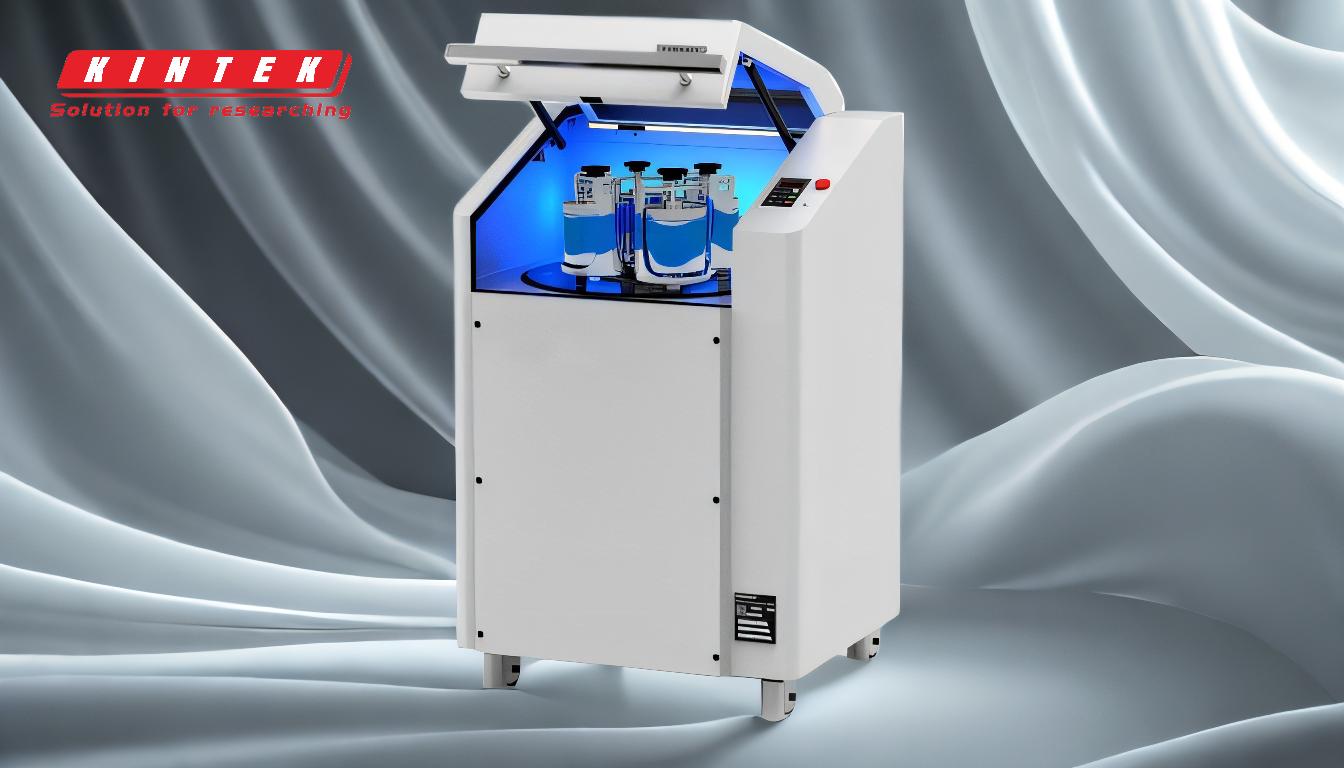
-
Versatility in Product Manufacturing:
- Injection moulding machines are used to create a wide variety of products, from small, intricate components to larger, more complex items.
- Examples include:
- Wire spools: Used in electrical and telecommunications industries.
- Bottle caps: Essential in the packaging industry for sealing beverages and other liquids.
- Automotive parts: Components like dashboards, bumpers, and interior trims are commonly produced using injection moulding.
- Toys and consumer goods: Items like pocket combs, storage containers, and small furniture pieces are often made using this method.
-
High Precision and Complexity:
- Injection moulding allows for the production of parts with high precision and intricate designs.
- This is particularly important in industries like electronics and mechanical engineering, where components such as gears and other mechanical parts must meet strict tolerances.
-
Cost-Effectiveness and Scalability:
- The process is highly efficient, making it cost-effective for large-scale production.
- Once the initial mould is created, the cost per unit decreases significantly with higher volumes, making it ideal for mass production.
-
Material Flexibility:
- Injection moulding can be used with a wide range of thermoplastic materials, allowing for flexibility in product design and functionality.
- Different materials can be chosen based on the required properties of the final product, such as strength, flexibility, or resistance to heat and chemicals.
-
Applications in Various Industries:
- Automotive: Injection moulding is crucial for producing durable and lightweight parts that meet the industry's stringent safety and performance standards.
- Packaging: The ability to produce high volumes of consistent, high-quality items like bottle caps and containers makes injection moulding indispensable in this sector.
- Consumer Goods: From toys to household items, injection moulding provides a reliable method for producing a wide range of products.
- Electronics: Precision components such as housings, connectors, and insulators are commonly manufactured using injection moulding.
-
Innovation and Customization:
- Advances in injection moulding technology have enabled greater customization and innovation in product design.
- This includes the ability to produce multi-material and multi-colour parts, as well as integrating features like snap-fits, living hinges, and textured surfaces directly into the moulded part.
In summary, injection moulding machines are a cornerstone of modern manufacturing, offering unparalleled versatility, precision, and efficiency. Their applications span across numerous industries, making them an essential tool for producing a wide range of plastic products that meet the demands of today's market.
Summary Table:
Key Benefits | Details |
---|---|
Versatility | Produces small to large, intricate to complex items across industries. |
High Precision | Ensures strict tolerances for parts like gears and electronics components. |
Cost-Effectiveness | Ideal for mass production with lower per-unit costs at higher volumes. |
Material Flexibility | Works with various thermoplastics for tailored product properties. |
Industry Applications | Automotive, packaging, consumer goods, electronics, and more. |
Innovation & Customization | Enables multi-material, multi-colour parts and advanced design features. |
Ready to enhance your production capabilities? Contact us today to learn more about injection moulding solutions!