Protective coatings are widely used across various industries to enhance the properties of materials, reduce costs, and extend the lifespan of components. They provide benefits such as corrosion and wear resistance, improved surface hardness, thermal and electrical insulation, and modified surface textures. These coatings are applied in industries like automotive and aerospace for purposes ranging from protection and decoration to functional improvements, such as reducing fuel consumption and preventing debris accumulation. By offering a thin yet effective layer of protection, coatings help mitigate material scarcity and reduce the need for frequent part replacement, making them a cost-effective and sustainable solution.
Key Points Explained:
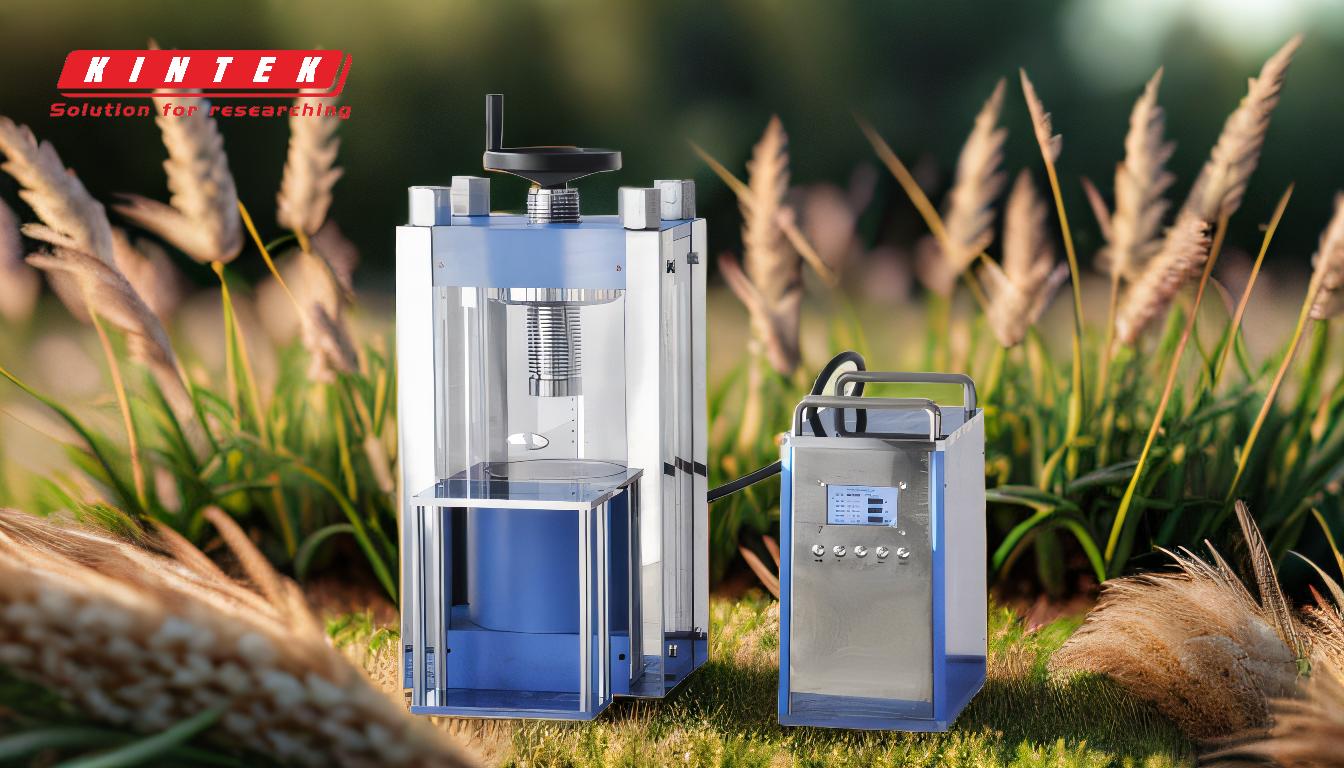
-
Enhancing Material Properties:
- Protective coatings improve the performance of materials by providing corrosion resistance, wear resistance, and increased surface hardness. This makes coated materials more durable and suitable for harsh environments.
- They also modify surface textures, enhancing properties like wettability or hydrophobicity, which are critical in applications such as water-repellent surfaces or improved adhesion.
-
Cost Efficiency:
- Coatings reduce the need for frequent replacement of parts by extending their lifespan. This is particularly beneficial in industries where components are exposed to extreme conditions, such as high temperatures or corrosive environments.
- By applying a thin layer (micrometers thick), coatings minimize material usage, addressing scarcity concerns and lowering overall manufacturing costs.
-
Versatility in Applications:
- Protective coatings are used for decoration, protection, and functional purposes. For example, in the automotive industry, they enhance corrosion resistance, improve aesthetics, and protect electronic equipment.
- In the aerospace sector, coatings reduce resistance, prevent debris accumulation, and contribute to fuel efficiency, showcasing their adaptability to diverse industrial needs.
-
Wide Range of Coating Materials:
- Coatings can be made from various materials, including metallic alloys, ceramics, bio-glasses, polymers, and engineered plastics. This variety allows designers to select the most suitable coating for specific applications, ensuring optimal performance and durability.
-
Sustainability and Resource Management:
- By extending the life of existing parts and reducing the need for new materials, protective coatings contribute to sustainable manufacturing practices. This aligns with global efforts to minimize resource consumption and environmental impact.
-
Industry-Specific Benefits:
- Automotive Industry: Coatings improve corrosion resistance, enhance decorative finishes, and protect sensitive components like electronics.
- Aerospace Industry: Coatings help reduce drag, prevent debris buildup, and improve fuel efficiency, making them essential for high-performance applications.
In summary, protective coatings are a critical technology that enhances material performance, reduces costs, and supports sustainability across multiple industries. Their versatility and ability to address specific industrial challenges make them indispensable in modern manufacturing and engineering.
Summary Table:
Key Benefits | Description |
---|---|
Enhanced Material Properties | Improves corrosion resistance, wear resistance, and surface hardness. |
Cost Efficiency | Extends part lifespan, reduces material usage, and lowers manufacturing costs. |
Versatility | Used for decoration, protection, and functional improvements in various industries. |
Wide Range of Materials | Includes metallic alloys, ceramics, polymers, and more for tailored applications. |
Sustainability | Reduces resource consumption and supports eco-friendly manufacturing practices. |
Learn how protective coatings can benefit your industry—contact our experts today!