Spark plasma sintering (SPS) is a versatile and advanced powder metallurgy technology that enables the rapid and efficient sintering of various materials, including metals, ceramics, and composites. It operates at lower temperatures and shorter times compared to traditional sintering methods, making it cost-effective and energy-efficient. SPS is widely used in research and industrial applications, such as producing high-density ceramics, nanomaterials, bulk amorphous alloys, and gradient functional materials. Its ability to achieve near-100% densification and controlled microstructures without grain growth makes it ideal for applications in aerospace, defense, and advanced material synthesis.
Key Points Explained:
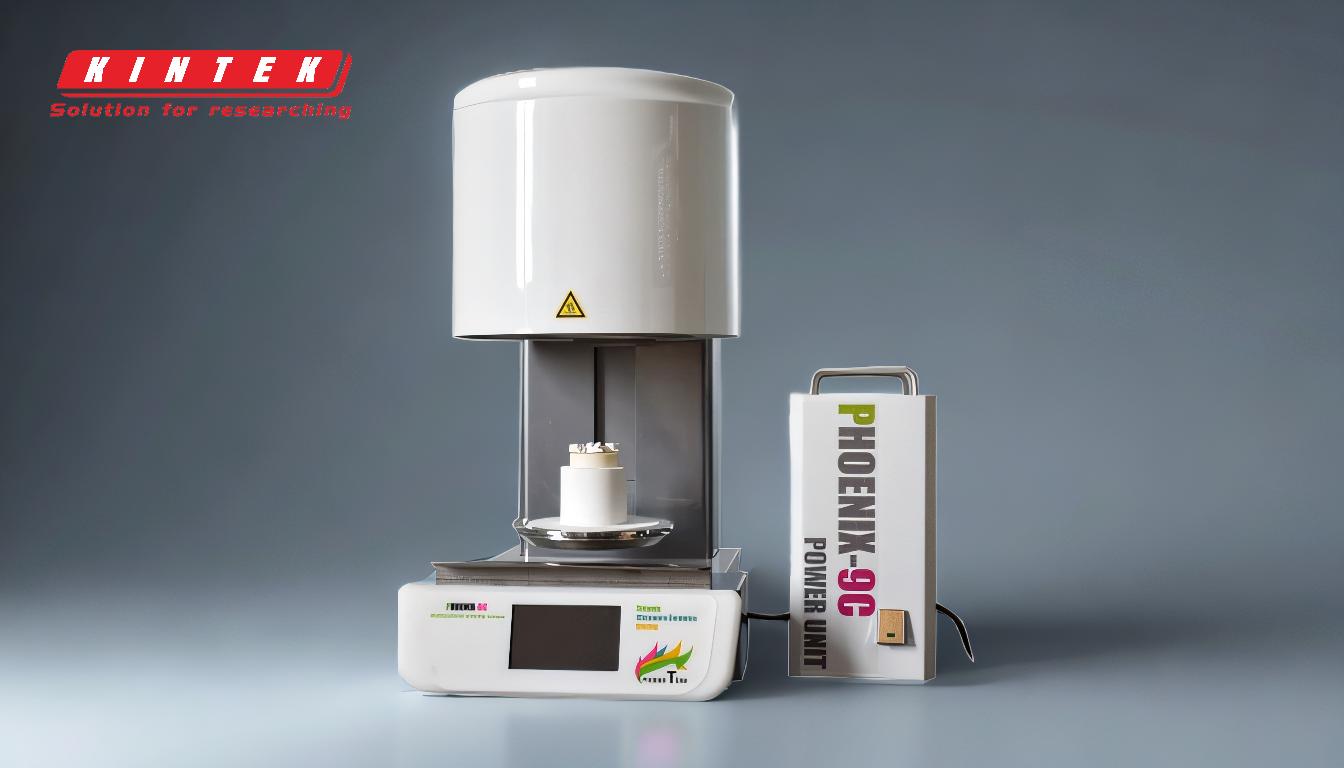
-
Fundamentals of Spark Plasma Sintering (SPS):
- SPS uses high-energy electric sparks to activate powder particles, removing impurities and adsorbed gases.
- The process operates at lower temperatures and shorter times compared to conventional sintering methods.
- It is suitable for metals, ceramics, nanostructured materials, and composites.
-
Key Advantages of SPS:
- Fast Processing: SPS typically completes sintering in less than 20 minutes.
- Cost-Effective: Low operating costs due to the use of pulsating currents and short cycle times.
- High Densification: Achieves near-100% densification, making it ideal for materials requiring high solid densities.
- Versatility: Can be used for both insulators and conductors, broadening its application range.
-
Applications in Material Synthesis:
- Nanomaterials: SPS is ideal for producing nanomaterials with controlled microstructures.
- Bulk Amorphous Alloys: Enables the creation of amorphous alloys with unique properties.
- Gradient Functional Materials: Used to synthesize materials with graded properties for specialized applications.
- High-Density Ceramics and Cermets: Produces fine-grained, high-density ceramics for demanding applications.
-
Industrial and Commercial Applications:
- Aerospace and Defense: Used to manufacture rocket nozzles, body armor, and other high-performance materials.
- Carbon Fiber Composites: SPS is employed in the production of lightweight, strong carbon fiber composites.
- Solid Electrolytes and Electric Thermal Materials: Ideal for research and development in energy storage and conversion technologies.
-
Research and Development:
- SPS is widely used in laboratories for synthesizing innovative materials with controlled microstructures.
- It is particularly suited for studying solid electrolytes and electric thermal materials, which are critical for advanced energy systems.
-
Operational Flexibility:
- SPS can operate under a wide range of conditions, including low temperature and high pressure (500–1000 MPa) or low pressure (20–30 MPa) and high temperature (1000–2000°C).
- This flexibility allows for the sintering of diverse materials with tailored properties.
-
Commercial Availability:
- SPS equipment is now commercially available, enabling its use beyond laboratory research.
- It is being adopted for large-scale production of hybrid materials and advanced components.
By leveraging its unique capabilities, SPS has become a critical technology in both academic research and industrial manufacturing, offering unparalleled efficiency, versatility, and material performance.
Summary Table:
Key Aspect | Details |
---|---|
Fundamentals | Uses high-energy electric sparks; operates at lower temperatures and times. |
Advantages | Fast processing (<20 mins), cost-effective, near-100% densification. |
Applications | Nanomaterials, bulk amorphous alloys, high-density ceramics, aerospace. |
Operational Flexibility | Works under low/high temperature and pressure conditions. |
Commercial Availability | Widely used in labs and industries for large-scale production. |
Learn how Spark Plasma Sintering (SPS) can transform your material synthesis process—contact our experts today!