Brazing is a metal-joining process that involves heating a filler metal above its melting point and distributing it between two or more close-fitting parts by capillary action. The average temperature for brazing typically ranges between 450°C (842°F) and 900°C (1652°F), depending on the materials being joined and the type of filler metal used. This temperature range is chosen to ensure that the filler metal melts and flows properly without damaging the base materials. The process is widely used in industries such as automotive, aerospace, and HVAC due to its ability to create strong, leak-proof joints.
Key Points Explained:
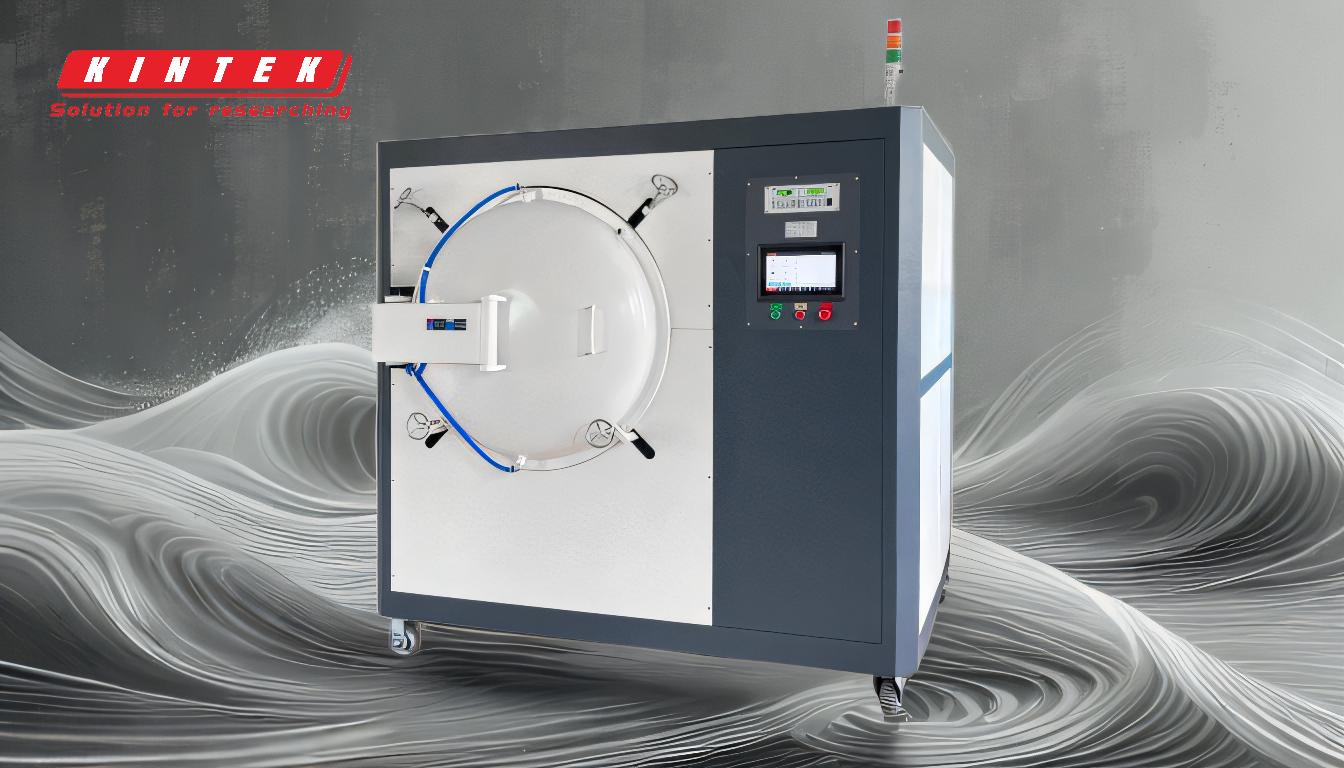
-
Definition of Brazing:
- Brazing is a joining process that uses a filler metal with a melting point above 450°C (842°F) but below the melting point of the base materials. This ensures that the base materials remain solid while the filler metal melts and flows into the joint.
-
Temperature Range:
- The average brazing temperature typically falls between 450°C (842°F) and 900°C (1652°F). This range is suitable for most common brazing applications and materials.
- The exact temperature depends on the filler metal and the base materials. For example, aluminum brazing typically occurs at the lower end of the range (around 600°C or 1112°F), while stainless steel brazing may require higher temperatures (up to 900°C or 1652°F).
-
Factors Influencing Brazing Temperature:
- Filler Metal Composition: Different filler metals have different melting points. Common filler metals include silver-based alloys, copper-based alloys, and aluminum-based alloys.
- Base Material Properties: The thermal conductivity and melting point of the base materials influence the required brazing temperature.
- Joint Design: The design of the joint, including the gap between parts, affects the flow of the filler metal and the necessary temperature.
-
Advantages of Brazing:
- Strong Joints: Brazing creates strong, durable joints that can withstand mechanical stress and thermal cycling.
- Versatility: It can join dissimilar metals, such as copper to stainless steel or aluminum to steel.
- Leak-Proof Seals: Brazed joints are often used in applications requiring leak-proof seals, such as in refrigeration or plumbing systems.
-
Common Applications:
- Automotive Industry: Brazing is used to join components like radiators, heat exchangers, and air conditioning systems.
- Aerospace Industry: It is employed in the fabrication of fuel systems, hydraulic systems, and structural components.
- HVAC Systems: Brazing is critical for assembling heat exchangers and refrigeration systems.
-
Equipment Used in Brazing:
- Torches: Often used for manual brazing, providing localized heat.
- Furnaces: Used for batch brazing, where multiple parts are heated uniformly.
- Induction Heating: Provides precise, rapid heating for high-volume production.
-
Safety Considerations:
- Proper ventilation is essential to avoid inhaling fumes from heated metals or fluxes.
- Protective gear, such as gloves and goggles, should be worn to prevent burns and eye injuries.
- The workspace should be free of flammable materials to reduce fire hazards.
By understanding the average temperature range and the factors that influence brazing, you can select the appropriate materials and equipment for your specific application, ensuring strong, reliable joints.
Summary Table:
Aspect | Details |
---|---|
Average Temperature | 450°C (842°F) to 900°C (1652°F) |
Filler Metals | Silver-based, copper-based, aluminum-based alloys |
Base Materials | Aluminum, stainless steel, copper, etc. |
Key Applications | Automotive, aerospace, HVAC systems |
Equipment | Torches, furnaces, induction heating |
Advantages | Strong joints, versatility, leak-proof seals |
Safety Considerations | Ventilation, protective gear, fire hazard prevention |
Need help selecting the right brazing equipment or materials? Contact our experts today for tailored solutions!