Graphite furnace atomic absorption spectroscopy (GFAAS) is a highly sensitive analytical technique used to measure trace metal concentrations in samples. It operates on the principle that free atoms in the gaseous state can absorb light at specific wavelengths, corresponding to the energy required to excite their outer electrons. The absorption of light is quantified using Beer-Lambert's Law, where absorbance (A) is directly proportional to the concentration (C) of the element in the sample. GFAAS uses a graphite furnace to atomize the sample, providing a controlled environment for generating free atoms. This method is known for its high sensitivity, precision, and ability to detect elements at very low concentrations (ppm to ppb levels).
Key Points Explained:
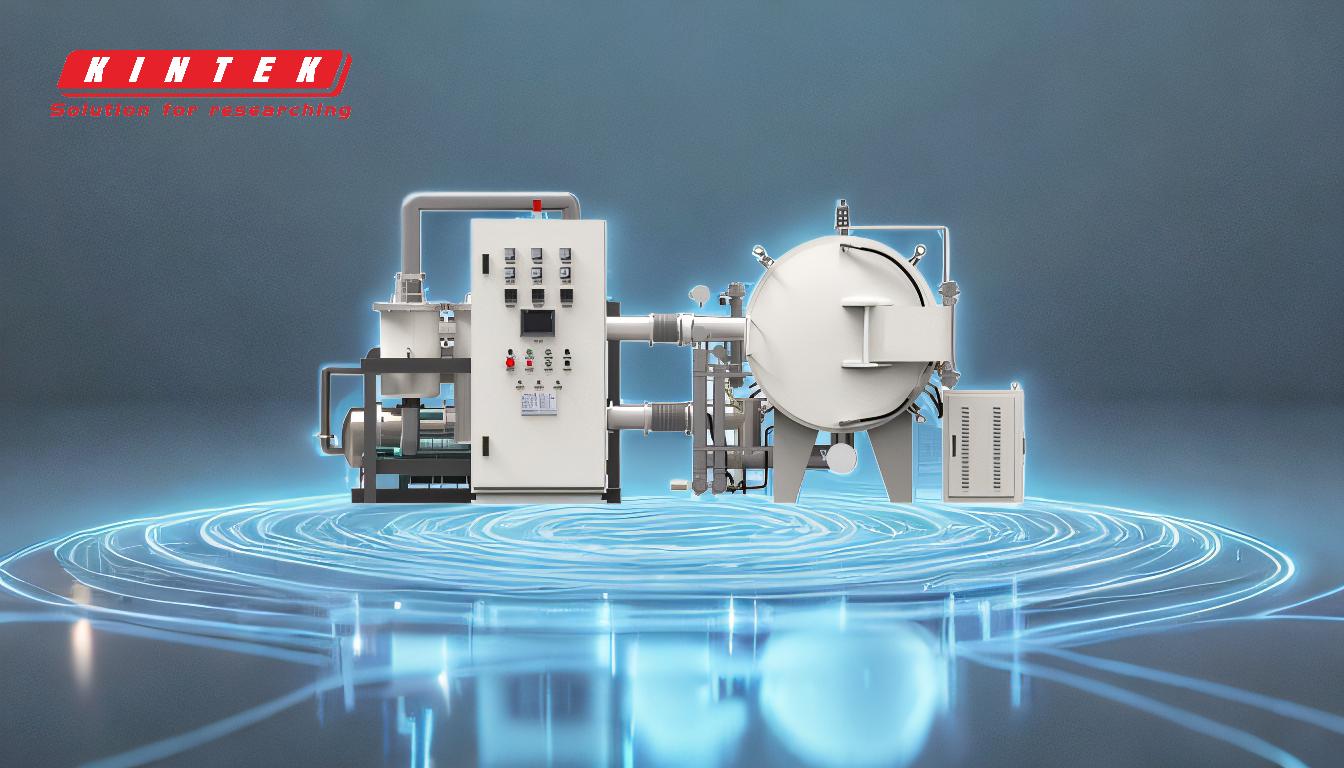
-
Principle of Atomic Absorption Spectroscopy (AAS):
- AAS is based on the absorption of light by free atoms in the gaseous state. When light of a specific wavelength passes through a sample, the atoms absorb energy, causing their outer electrons to transition from the ground state to an excited state.
- The amount of light absorbed is proportional to the concentration of the element in the sample, as described by Beer-Lambert's Law: ( A = KC ), where ( A ) is absorbance, ( K ) is a constant, and ( C ) is the concentration.
-
Role of the Graphite Furnace:
- The graphite furnace serves as the atomizer in GFAAS. It heats the sample to extremely high temperatures (up to 3000°C) in a controlled manner, converting the sample into free atoms.
- The furnace provides a stable environment for atomization, ensuring that the atoms remain in the gaseous state long enough to absorb light and produce accurate measurements.
-
Beer-Lambert's Law in GFAAS:
- Beer-Lambert's Law states that the absorbance of light is directly proportional to the concentration of the absorbing species in the sample.
- In GFAAS, this law is applied to quantify the concentration of trace metals by measuring the amount of light absorbed at a specific wavelength.
-
High Sensitivity and Precision:
- GFAAS is capable of detecting elements at very low concentrations, typically in the parts per million (ppm) to parts per billion (ppb) range.
- The technique offers excellent precision due to the controlled conditions of the graphite furnace and the ability to measure specific wavelengths of light.
-
Applications and Advantages:
- GFAAS is widely used in environmental testing, clinical analysis, and industrial quality control due to its ability to measure over 70 elements.
- Its advantages include high sensitivity, good selectivity, and the ability to analyze small sample volumes with minimal preparation.
-
Comparison to Flame AAS:
- Unlike flame AAS, which uses a flame to atomize the sample, GFAAS uses a graphite furnace. This allows for higher sensitivity and lower detection limits.
- GFAAS is particularly useful for analyzing samples with very low analyte concentrations or when only a small sample volume is available.
By combining the principles of atomic absorption with the precision of the graphite furnace, GFAAS provides a powerful tool for trace metal analysis in various fields. Its ability to deliver accurate and reliable results makes it a preferred choice for laboratories requiring high sensitivity and precision.
Summary Table:
Key Aspect | Description |
---|---|
Principle | Absorbs light at specific wavelengths using free atoms in the gaseous state. |
Graphite Furnace Role | Atomizes samples at up to 3000°C, ensuring stable and precise measurements. |
Beer-Lambert's Law | Absorbance (A) is proportional to concentration (C) of the element in the sample. |
Sensitivity & Precision | Detects elements at ppm to ppb levels with high accuracy. |
Applications | Used in environmental testing, clinical analysis, and industrial quality control. |
Advantages | High sensitivity, good selectivity, and minimal sample preparation required. |
Discover how GFAAS can enhance your lab's trace metal analysis—contact our experts today!