Vacuum arc remelting (VAR) is a specialized metallurgical process used to refine and improve the quality of metals and alloys, particularly those used in high-performance applications like aerospace, medical implants, and power generation. The process involves melting a consumable electrode under vacuum conditions using an electric arc, which helps remove impurities, control the microstructure, and enhance the mechanical properties of the material. The benefits of VAR include improved material purity, reduced gas content, better homogeneity, and enhanced mechanical properties such as strength, fatigue resistance, and ductility. These advantages make VAR an essential process for producing high-integrity materials that meet stringent industry standards.
Key Points Explained:
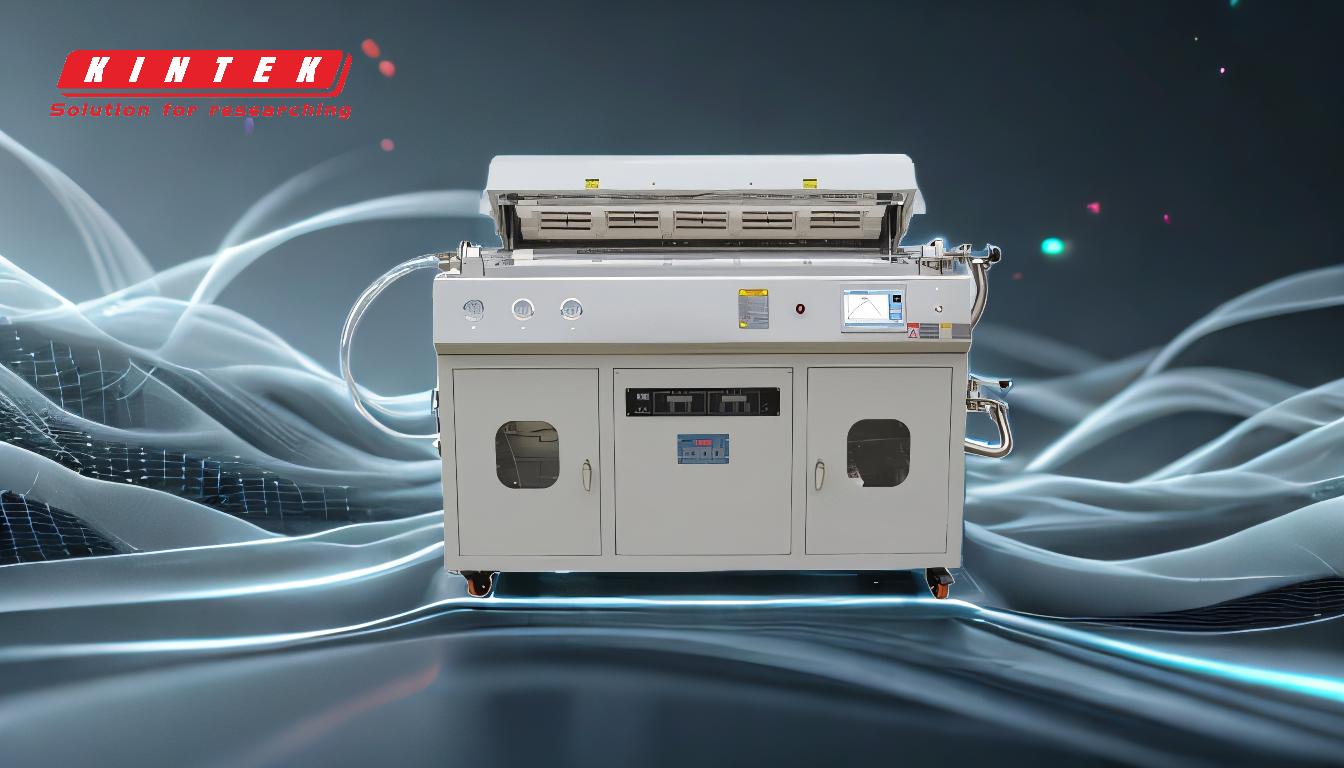
-
Improved Material Purity:
- VAR eliminates impurities such as oxides, sulfides, and other non-metallic inclusions by melting the metal in a vacuum environment. This results in a cleaner material with fewer defects, which is critical for applications requiring high reliability and performance.
-
Reduced Gas Content:
- The vacuum environment in VAR significantly reduces the levels of dissolved gases like hydrogen, oxygen, and nitrogen in the metal. Lower gas content minimizes the risk of porosity and improves the material's resistance to cracking and embrittlement.
-
Enhanced Microstructure Control:
- VAR allows for precise control over the solidification process, leading to a uniform and fine-grained microstructure. This uniformity enhances the material's mechanical properties, such as strength, toughness, and fatigue resistance.
-
Better Homogeneity:
- The remelting process ensures a consistent chemical composition throughout the material, reducing segregation and enhancing the overall quality of the alloy. This is particularly important for alloys used in critical applications where consistency is paramount.
-
Improved Mechanical Properties:
- The combination of reduced impurities, lower gas content, and controlled microstructure results in materials with superior mechanical properties. These include higher tensile strength, improved fatigue life, and enhanced ductility, making VAR-processed materials ideal for demanding environments.
-
Applications in High-Performance Industries:
- VAR is widely used in industries such as aerospace, medical, and power generation, where materials must withstand extreme conditions. For example, VAR-processed alloys are used in jet engine components, surgical implants, and turbine blades, where failure is not an option.
-
Compliance with Industry Standards:
- VAR helps manufacturers meet stringent industry standards and specifications, ensuring that the materials produced are of the highest quality and suitable for critical applications.
In summary, vacuum arc remelting offers significant benefits in terms of material purity, microstructure control, and mechanical properties, making it an indispensable process for producing high-performance alloys used in critical applications.
Summary Table:
Benefit | Description |
---|---|
Improved Material Purity | Eliminates impurities like oxides and sulfides, resulting in cleaner materials. |
Reduced Gas Content | Lowers dissolved gases, reducing porosity and improving crack resistance. |
Enhanced Microstructure | Ensures uniform, fine-grained microstructure for better mechanical properties. |
Better Homogeneity | Provides consistent chemical composition, reducing segregation. |
Superior Mechanical Properties | Increases tensile strength, fatigue resistance, and ductility. |
High-Performance Applications | Used in aerospace, medical, and power generation industries. |
Compliance with Standards | Meets stringent industry specifications for critical applications. |
Learn how vacuum arc remelting can elevate your material quality—contact our experts today!