The best type of crucible depends on the specific application, as crucibles are designed to meet unique operational requirements. Key factors include the material being processed, the furnace type, temperature requirements, and chemical compatibility. For scientific applications, inert materials like platinum or zirconium are ideal to avoid contamination. For melting precious metals, crucibles with non-wetting properties and durable protective glazes are preferred. Induction furnaces require crucibles with electrical resistivity matched to the furnace's operating frequency. Ultimately, the best crucible maximizes performance by aligning with the specific combination of furnace, alloy, and operational practices.
Key Points Explained:
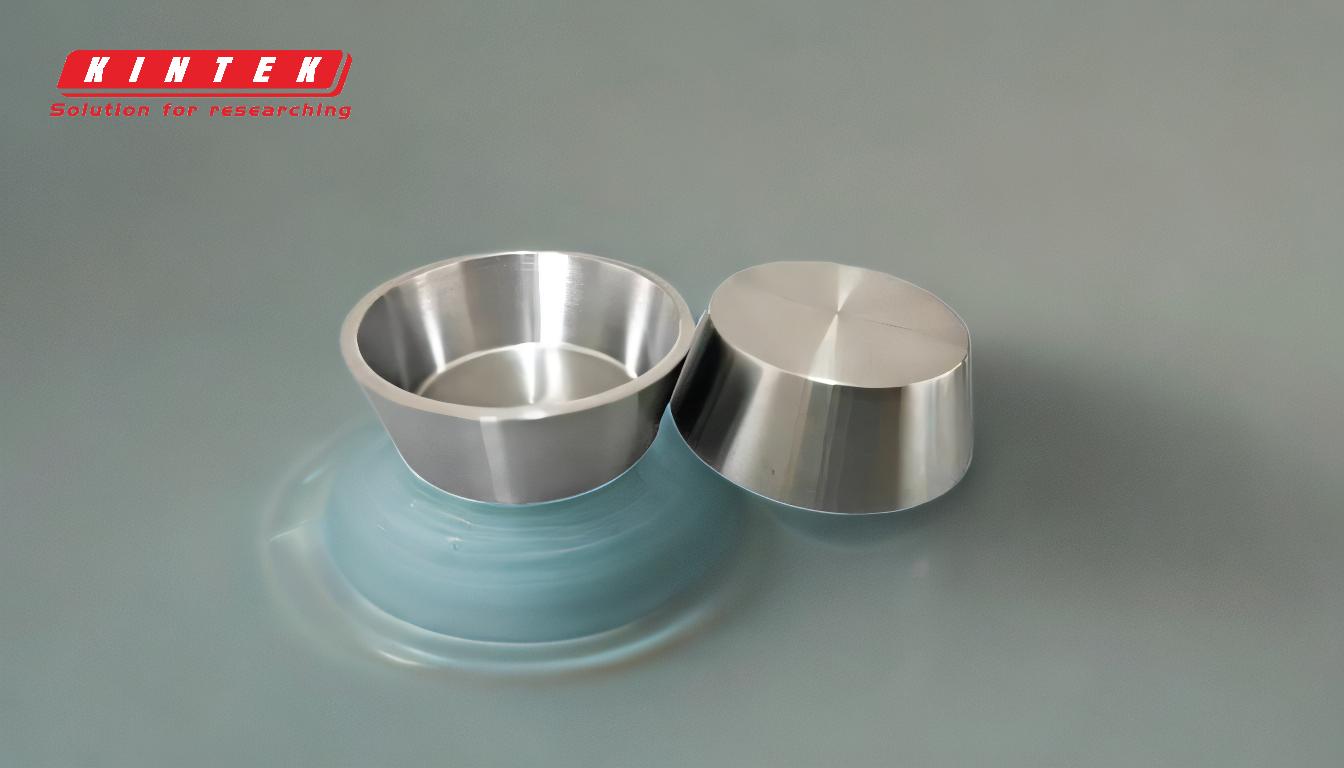
-
Material Compatibility:
- Crucibles must be chemically inert to the materials they contain to prevent contamination. For example, platinum or zirconium crucibles are ideal for scientific applications due to their inertness.
- In melting precious metals, non-wetting properties are critical to ensure clean metal output and prevent alloy cross-contamination.
-
Temperature Resistance:
- The crucible must withstand high temperatures and have a melting point higher than the materials being processed. This ensures durability and prevents failure during high-temperature operations.
- For induction furnaces, the crucible's electrical resistivity must match the furnace's operating frequency to avoid overheating.
-
Operational Requirements:
- The crucible's capacity, dimensions, and type must align with the furnace and the specific alloy being melted.
- Factors like melting and holding temperatures, temperature change rates, charging methods, and slag removal processes must be considered to ensure optimal performance.
-
Application-Specific Needs:
- Each operation is unique, requiring a crucible tailored to the specific combination of furnace, alloy, and working practices.
- For example, lower frequency induction furnaces may require crucibles with high silicon carbide content, while higher frequency furnaces may need crucibles with high clay content.
-
Durability and Stability:
- A dense material structure and durable protective glaze are essential for crucibles used in refining and melting precious metals to ensure long-term performance and resistance to wear.
By carefully evaluating these factors, the best crucible can be selected to meet the specific needs of the application, ensuring maximum performance and reliability.
Summary Table:
Key Factor | Description |
---|---|
Material Compatibility | Crucibles must be chemically inert to prevent contamination (e.g., platinum, zirconium). Non-wetting properties are critical for precious metals. |
Temperature Resistance | Crucibles must withstand high temperatures and match furnace operating frequency for induction furnaces. |
Operational Requirements | Capacity, dimensions, and type must align with furnace and alloy. Consider melting/holding temperatures, charging methods, and slag removal. |
Application-Specific Needs | Tailor crucibles to furnace type, alloy, and working practices (e.g., silicon carbide for low-frequency furnaces). |
Durability and Stability | Dense material structure and durable protective glazes ensure long-term performance for refining and melting. |
Need help selecting the right crucible for your application? Contact our experts today for personalized advice!