The capacity of a continuous furnace refers to its ability to handle a continuous flow of workpieces or materials through its heating chamber, typically measured in terms of throughput (e.g., weight or volume per hour) or the size and quantity of workpieces it can process. Continuous furnaces are designed for high-volume production, operating at permanent temperature conditions and specialized for specific heat treatment processes like annealing, hardening, or carburizing. Their capacity is influenced by factors such as furnace length, conveyor speed, heating zone design, and the type of material being processed. While they excel in efficiency and consistency for large-scale operations, they are less flexible for small batches or complex geometries and require significant energy and maintenance resources.
Key Points Explained:
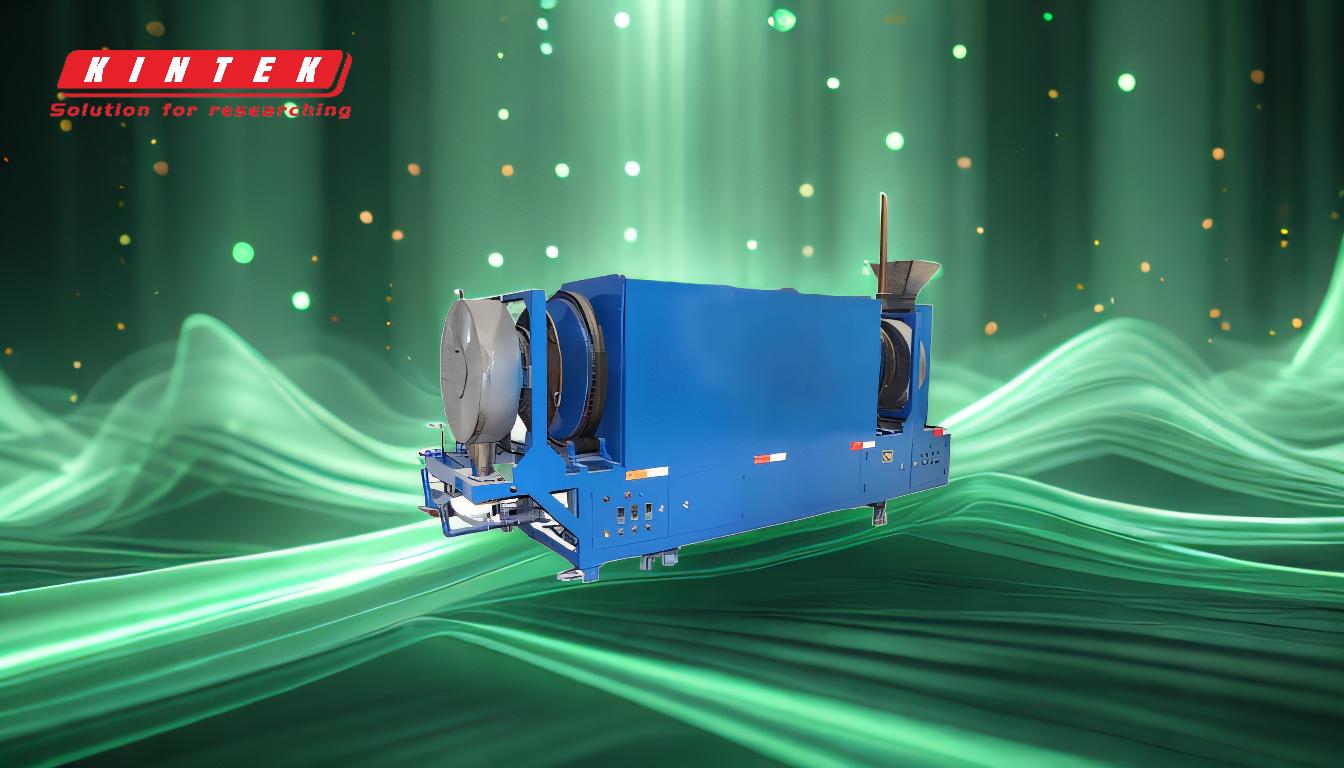
-
Definition and Function of Continuous Furnaces:
- Continuous furnaces are industrial heat treatment systems designed for uninterrupted processing of workpieces or materials.
- They use conveyor belts, rollers, or wire mesh to transport materials through the heating chamber at a constant speed or step-by-step.
- These furnaces are ideal for high-volume production, offering consistent and efficient heat treatment for processes like annealing, hardening, normalizing, and carburizing.
-
Factors Influencing Capacity:
- Throughput: The capacity is often measured in terms of throughput, such as weight (e.g., tons per hour) or volume (e.g., cubic meters per hour) of material processed.
- Furnace Length and Design: Longer furnaces with multiple heating zones can handle larger quantities of material or longer workpieces.
- Conveyor Speed: The speed at which the conveyor or roller system moves determines how quickly materials pass through the furnace, directly impacting throughput.
- Material Type: The size, shape, and thermal properties of the material being processed influence the furnace's capacity. For example, smaller or thinner materials may allow for higher throughput.
-
Specialization and Limitations:
- Continuous furnaces are specialized for specific processes and materials, making them highly efficient for repetitive, high-volume tasks.
- They have limited flexibility for small batches or complex geometries, as they are optimized for uniform, consistent processing.
- Their continuous operation requires higher energy consumption and specialized maintenance, which can affect overall operational capacity.
-
Applications and Examples:
- Continuous furnaces are commonly used in industries like automotive, aerospace, and manufacturing for heat treating metal components.
- Examples include reheating semi-finished products for hot forming or curing and drying medium to high-volume products.
-
Energy and Maintenance Considerations:
- Continuous operation demands significant energy resources, which can impact the furnace's capacity in terms of cost and sustainability.
- Maintenance complexity and the need for specialized knowledge can also influence the furnace's long-term capacity and efficiency.
By understanding these key points, purchasers can evaluate the capacity of a continuous furnace based on their specific production needs, material requirements, and operational constraints.
Summary Table:
Key Factors | Description |
---|---|
Throughput | Measured in weight (tons/hour) or volume (cubic meters/hour) of processed material. |
Furnace Length/Design | Longer furnaces with multiple heating zones handle larger quantities or longer workpieces. |
Conveyor Speed | Determines material flow rate, directly impacting throughput. |
Material Type | Size, shape, and thermal properties influence capacity (e.g., smaller materials allow higher throughput). |
Energy Consumption | Continuous operation requires significant energy resources. |
Maintenance | Specialized maintenance is needed to sustain long-term efficiency. |
Need a continuous furnace tailored to your production needs? Contact our experts today for a customized solution!