Carbon nanotubes (CNTs) are grown using catalysts, which are crucial for controlling their structure, quality, and properties. The catalyst plays a pivotal role in the synthesis process, influencing the nucleation, growth mechanism, and alignment of CNTs. Common catalysts include transition metals such as iron (Fe), cobalt (Co), nickel (Ni), and their alloys, which are often supported on substrates like silica, alumina, or magnesium oxide. These catalysts facilitate the decomposition of carbon-containing gases (e.g., methane, ethylene, or acetylene) at high temperatures, enabling the formation of CNTs through chemical vapor deposition (CVD) or other synthesis methods. The choice of catalyst and its properties, such as particle size, composition, and support material, significantly impact the growth kinetics, diameter, and chirality of the resulting CNTs.
Key Points Explained:
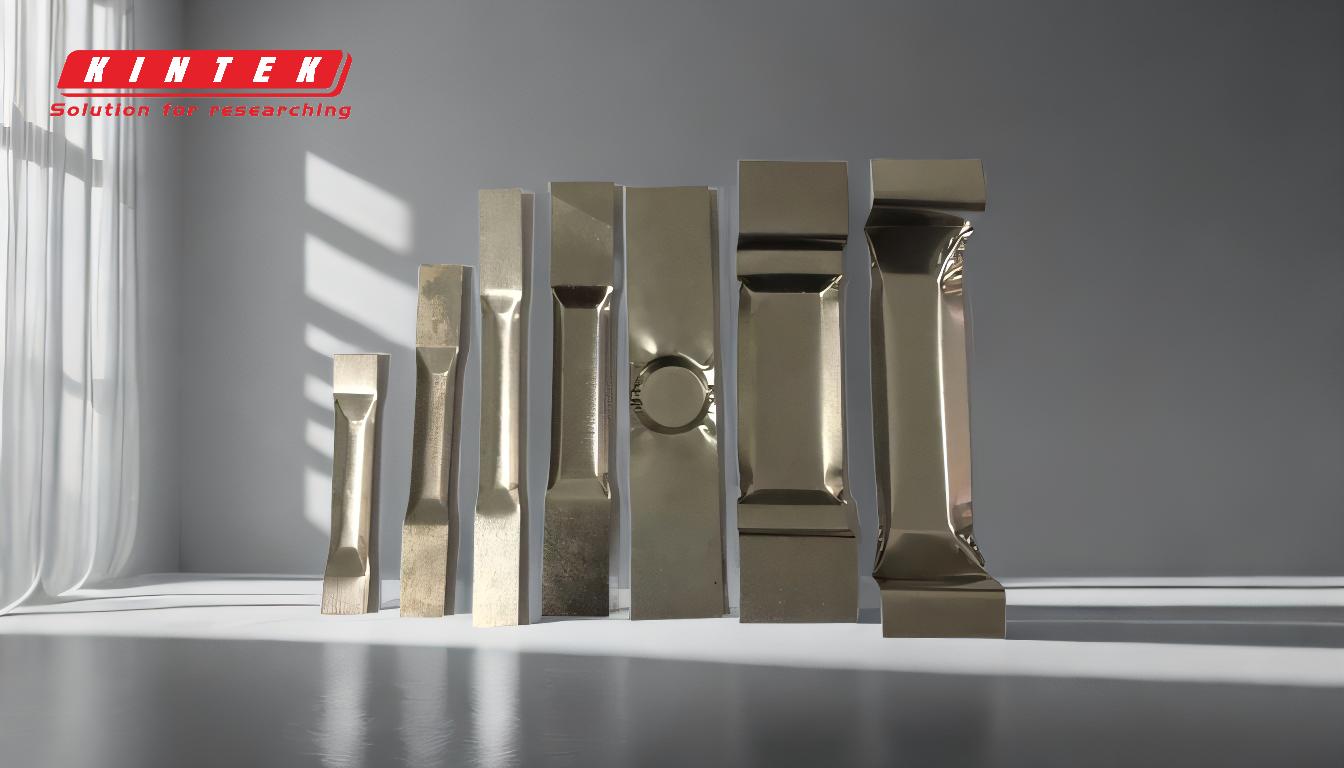
-
Role of Catalysts in CNT Growth:
- Catalysts are essential for initiating and sustaining the growth of carbon nanotubes. They act as nucleation sites where carbon atoms assemble into tubular structures.
- The catalyst's ability to decompose carbon-containing gases and promote carbon diffusion is critical for the growth process.
-
Common Catalyst Materials:
- Transition metals like iron (Fe), cobalt (Co), and nickel (Ni) are widely used due to their high catalytic activity and ability to form stable nanoparticles.
- Alloys of these metals, such as Fe-Co or Co-Ni, are also employed to enhance catalytic performance and control CNT properties.
-
Catalyst Support Materials:
- Catalysts are often deposited on support materials like silica (SiO2), alumina (Al2O3), or magnesium oxide (MgO) to stabilize the nanoparticles and prevent aggregation.
- The choice of support material influences the catalyst's dispersion, thermal stability, and interaction with the carbon source.
-
Catalyst Particle Size:
- The size of catalyst nanoparticles directly affects the diameter of the CNTs. Smaller particles typically yield narrower nanotubes.
- Precise control of particle size is achieved through techniques like chemical reduction, thermal decomposition, or sputtering.
-
Growth Mechanisms:
- The growth of CNTs can occur via two primary mechanisms: tip-growth and base-growth.
- In tip-growth, the catalyst particle remains at the tip of the growing nanotube.
- In base-growth, the catalyst particle stays anchored to the substrate while the nanotube grows upward.
- The mechanism depends on the adhesion strength between the catalyst and the substrate.
- The growth of CNTs can occur via two primary mechanisms: tip-growth and base-growth.
-
Influence of Catalyst on CNT Quality:
- The catalyst's composition and structure affect the crystallinity, defect density, and chirality of the CNTs.
- High-quality catalysts yield CNTs with fewer defects, better alignment, and enhanced electrical and mechanical properties.
-
Synthesis Techniques:
- Chemical vapor deposition (CVD) is the most common method for CNT growth, where the catalyst facilitates the decomposition of carbon precursors at elevated temperatures.
- Other techniques, such as arc discharge and laser ablation, also rely on catalysts but are less scalable compared to CVD.
-
Challenges and Innovations:
- Achieving uniform catalyst distribution and controlling particle size remain significant challenges in CNT synthesis.
- Advances in catalyst design, such as the use of bimetallic nanoparticles or patterned substrates, are being explored to improve CNT yield and quality.
In summary, the catalyst is a cornerstone of CNT growth, influencing every aspect of the synthesis process. By optimizing catalyst materials, particle size, and support systems, researchers can tailor CNT properties for specific applications, unlocking their full potential in fields like electronics, energy storage, and composites.
Summary Table:
Aspect | Details |
---|---|
Role of Catalysts | Initiate and sustain CNT growth; act as nucleation sites for carbon atoms. |
Common Materials | Iron (Fe), Cobalt (Co), Nickel (Ni), and their alloys. |
Support Materials | Silica (SiO2), Alumina (Al2O3), Magnesium Oxide (MgO). |
Particle Size Impact | Smaller particles yield narrower CNTs; controlled via reduction techniques. |
Growth Mechanisms | Tip-growth and base-growth, depending on catalyst-substrate adhesion. |
Influence on CNT Quality | Affects crystallinity, defect density, chirality, and alignment. |
Synthesis Techniques | Chemical Vapor Deposition (CVD), arc discharge, laser ablation. |
Challenges | Uniform catalyst distribution and particle size control. |
Ready to optimize your CNT growth process? Contact our experts today for tailored solutions!