Chemical vapor deposition (CVD) is a sophisticated manufacturing process used to create thin films on substrates through chemical reactions in a controlled environment. It involves transporting gaseous reactants to a heated substrate, where they undergo surface-mediated reactions to form a solid film. The process is widely used in industries such as semiconductors, optics, and coatings due to its ability to produce high-quality, uniform films. CVD is distinct from physical vapor deposition (PVD) as it relies on chemical reactions rather than physical processes like evaporation or sputtering. The steps in CVD include gas transport, adsorption, surface reactions, nucleation, film growth, and desorption of by-products.
Key Points Explained:
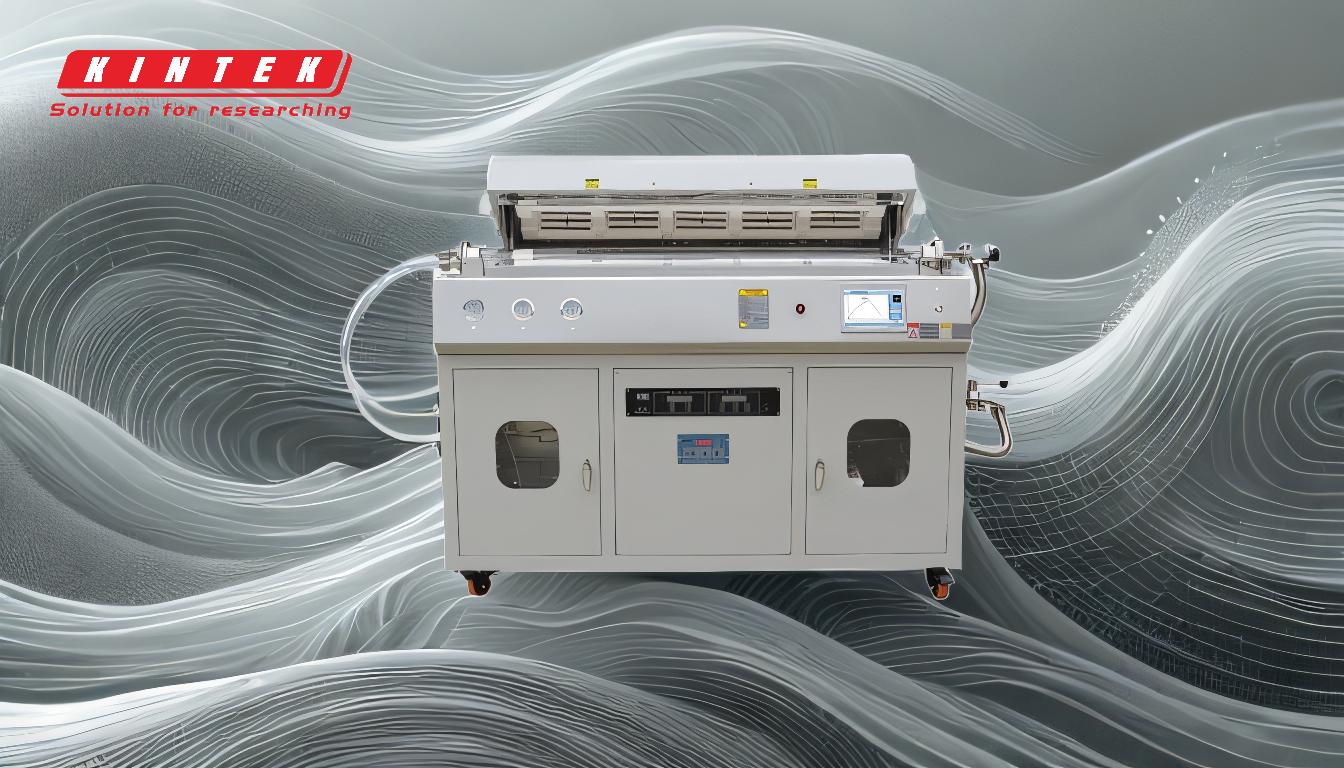
-
Definition of CVD:
- Chemical vapor deposition (CVD) is a process where thin solid films are formed on a substrate through chemical reactions of gaseous precursors. Unlike physical vapor deposition (PVD), which uses physical methods like evaporation or sputtering, CVD relies on chemical reactions to deposit materials.
-
Steps in the CVD Process:
- Transport of Reacting Gases: Gaseous reactants are transported to the substrate surface in a controlled environment, often under vacuum conditions.
- Adsorption: The gaseous species adsorb onto the substrate surface, preparing for the chemical reaction.
- Surface Reactions: Heterogeneous, surface-catalyzed reactions occur, leading to the formation of the desired thin film.
- Nucleation and Growth: The deposited species diffuse to growth sites, where they nucleate and grow into a continuous film.
- Desorption and Removal of By-products: Gaseous by-products and unreacted species desorb from the surface and are transported away from the reaction zone.
-
Applications of CVD:
- CVD is widely used in the semiconductor industry to deposit thin films of materials like silicon dioxide, silicon nitride, and polycrystalline silicon.
- It is also used in the production of optical coatings, wear-resistant coatings, and advanced materials like graphene.
-
Advantages of CVD:
- High-Quality Films: CVD produces uniform, high-purity films with excellent adhesion to the substrate.
- Conformal Coatings: The process can coat complex geometries evenly, making it suitable for intricate components.
- Versatility: CVD can deposit a wide range of materials, including metals, ceramics, and polymers.
-
Types of CVD:
- Atmospheric Pressure CVD (APCVD): Conducted at atmospheric pressure, suitable for high-throughput applications.
- Low-Pressure CVD (LPCVD): Operates under reduced pressure, providing better control over film properties.
- Plasma-Enhanced CVD (PECVD): Uses plasma to enhance chemical reactions, allowing deposition at lower temperatures.
- Metal-Organic CVD (MOCVD): Utilizes metal-organic precursors for depositing compound semiconductors.
-
Challenges in CVD:
- High Temperatures: Many CVD processes require high temperatures, which can limit the choice of substrates.
- Complexity: The process involves precise control of gas flow, temperature, and pressure, making it technically challenging.
- Cost: Equipment and precursor materials can be expensive, particularly for advanced CVD techniques.
-
Comparison with Other Deposition Methods:
- CVD vs. PVD: CVD uses chemical reactions, while PVD relies on physical processes. CVD generally provides better conformal coatings, whereas PVD is often faster and simpler.
- CVD vs. Chemical Deposition: Chemical deposition involves submerging the substrate in a chemical fluid, which is less precise and versatile compared to CVD.
By understanding these key points, equipment and consumable purchasers can make informed decisions about the suitability of CVD for their specific applications, considering factors like film quality, process complexity, and cost.
Summary Table:
Aspect | Details |
---|---|
Definition | Thin solid films formed via chemical reactions of gaseous precursors. |
Steps | Gas transport, adsorption, surface reactions, nucleation, growth, desorption. |
Applications | Semiconductors, optical coatings, wear-resistant coatings, graphene. |
Advantages | High-quality, uniform films; conformal coatings; versatile material options. |
Types of CVD | APCVD, LPCVD, PECVD, MOCVD. |
Challenges | High temperatures, process complexity, cost. |
Comparison with PVD | CVD uses chemical reactions; PVD relies on physical processes. |
Ready to integrate CVD technology into your workflow? Contact us today to learn more!