The Chemical Vapor Deposition (CVD) process of diamond synthesis is a sophisticated method used to create lab-grown diamonds by depositing carbon atoms onto a substrate in a controlled environment. This process involves introducing a carbon-rich gas mixture, typically methane and hydrogen, into a reaction chamber under low pressure and high temperature. The gases are ionized to break their molecular bonds, allowing pure carbon to adhere to a diamond seed. Over time, the carbon atoms accumulate and form atomic bonds with the seed, resulting in a larger diamond. The CVD process is highly controllable and can produce diamonds with specific properties, including colored diamonds, by introducing trace elements during the growth phase.
Key Points Explained:
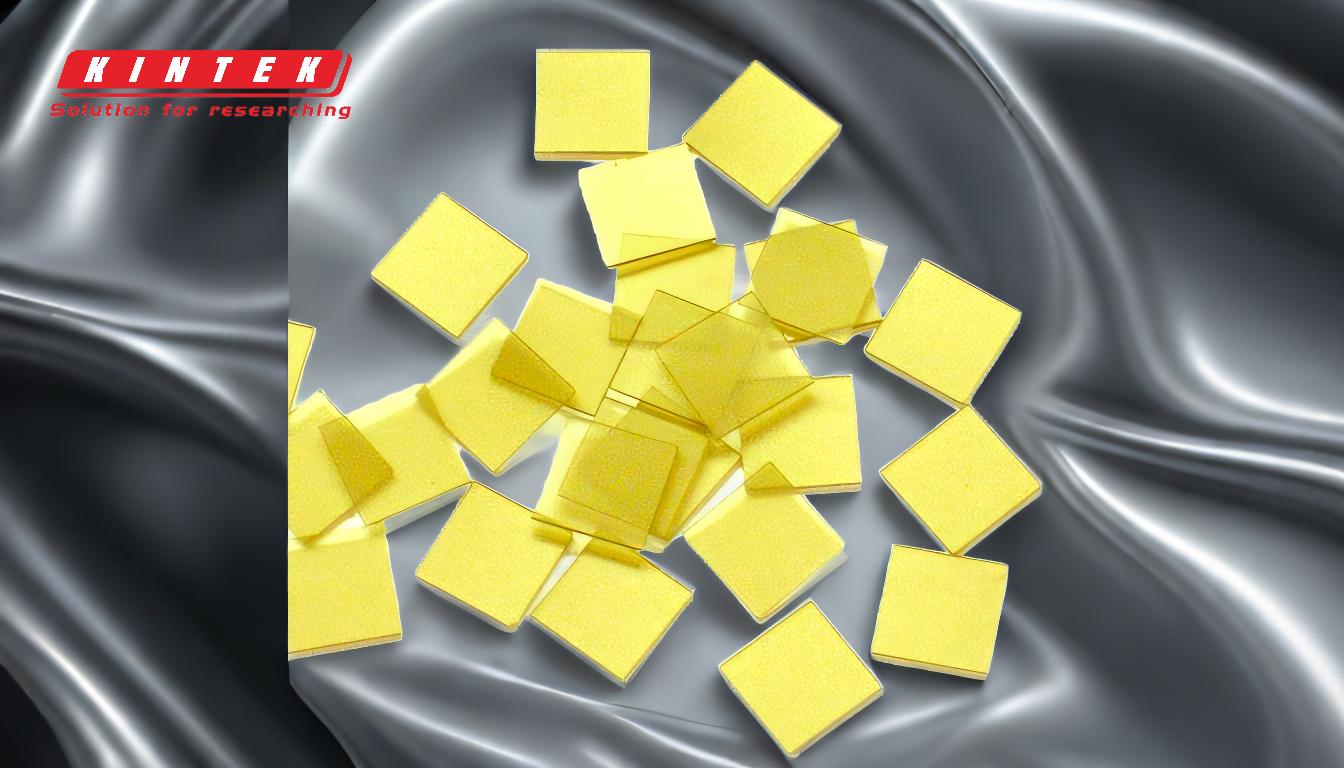
-
Introduction of Gas Mixture:
- The CVD process begins by introducing a mixture of hydrocarbon gas (usually methane) and hydrogen into a reaction chamber. This gas mixture is the source of carbon needed for diamond growth.
- The chamber is maintained at low pressure and high temperature, typically around 800°C, to facilitate the chemical reactions necessary for diamond formation.
-
Ionization and Breakdown of Gases:
- The gases in the chamber are ionized, often using microwaves or other energy sources, to break their molecular bonds. This ionization process converts some of the hydrogen into atomic hydrogen, which plays a crucial role in the diamond formation process.
- Atomic hydrogen reacts with the hydrocarbon gas, breaking it down into pure carbon atoms. These carbon atoms are the building blocks for the diamond.
-
Deposition of Carbon onto Substrate:
- A thin diamond seed, which serves as the substrate, is placed inside the chamber. The carbon atoms generated from the gas mixture deposit onto the surface of this seed.
- Over time, the carbon atoms accumulate and form atomic bonds with the seed diamond. This layer-by-layer deposition results in the growth of a larger diamond.
-
Formation of Diamond:
- As the carbon atoms continue to deposit onto the seed, they arrange themselves in the crystal lattice structure characteristic of diamond. This process is slow and meticulous, ensuring the formation of a high-quality diamond.
- The resulting diamond is chemically and structurally identical to natural diamonds, with the same hardness, brilliance, and durability.
-
Control and Customization:
- The CVD process offers excellent control over the diamond's properties. By adjusting the gas mixture, temperature, pressure, and other parameters, manufacturers can influence the diamond's size, quality, and even color.
- Colored diamonds can be created by introducing specific trace elements (e.g., boron for blue diamonds or nitrogen for yellow diamonds) into the carbon crystal lattice during the growth phase.
-
Equipment and Process Requirements:
- The CVD process requires specialized equipment, including a gas delivery system, a reaction chamber, a substrate loading mechanism, and an energy supplier (e.g., microwaves) to ionize the gases.
- The reaction chamber must be maintained under vacuum conditions to ensure the purity of the diamond and to facilitate the precise control of the deposition process.
-
Applications of CVD Diamonds:
- CVD diamonds are used in a wide range of applications, from jewelry to industrial uses. They are valued for their purity, consistency, and the ability to produce diamonds with specific properties tailored to different applications.
- In addition to gem-quality diamonds, CVD is also used to produce diamonds for cutting tools, optical components, and even in emerging technologies like quantum computing.
-
Advantages of CVD Over Other Methods:
- The CVD process has a relatively small equipment footprint and offers excellent process control, making it a preferred method for producing high-quality synthetic diamonds.
- Unlike high-pressure high-temperature (HPHT) methods, CVD does not require extreme pressures, which can simplify the equipment and reduce costs.
In summary, the CVD process of diamond synthesis is a highly controlled and versatile method for producing lab-grown diamonds. By carefully managing the gas mixture, temperature, and other parameters, manufacturers can create diamonds with specific properties, making CVD an essential technique in both the jewelry and industrial sectors.
Summary Table:
Key Aspect | Details |
---|---|
Gas Mixture | Methane and hydrogen introduced into a reaction chamber. |
Temperature & Pressure | ~800°C and low pressure for optimal diamond formation. |
Ionization | Gases ionized to break molecular bonds, releasing pure carbon atoms. |
Substrate | Diamond seed used as a base for carbon deposition. |
Diamond Formation | Carbon atoms bond to the seed, forming a larger diamond over time. |
Customization | Trace elements added to create colored diamonds (e.g., boron for blue). |
Applications | Jewelry, cutting tools, optical components, and quantum computing. |
Advantages | High control, small equipment footprint, and no extreme pressure required. |
Discover how CVD diamonds can meet your needs—contact our experts today!