DC sputtering is a widely used thin-film deposition technique in the field of Physical Vapor Deposition (PVD). It involves bombarding a target material with high-energy ions, causing atoms to be ejected from the target surface. These ejected atoms then travel through a vacuum chamber and deposit onto a substrate, forming a thin film. The process is controlled by parameters such as ion energy, target material properties, and chamber conditions, ensuring consistent and high-quality film deposition. DC sputtering is particularly effective for conductive materials and is used in various applications, including semiconductor manufacturing, optical coatings, and decorative finishes.
Key Points Explained:
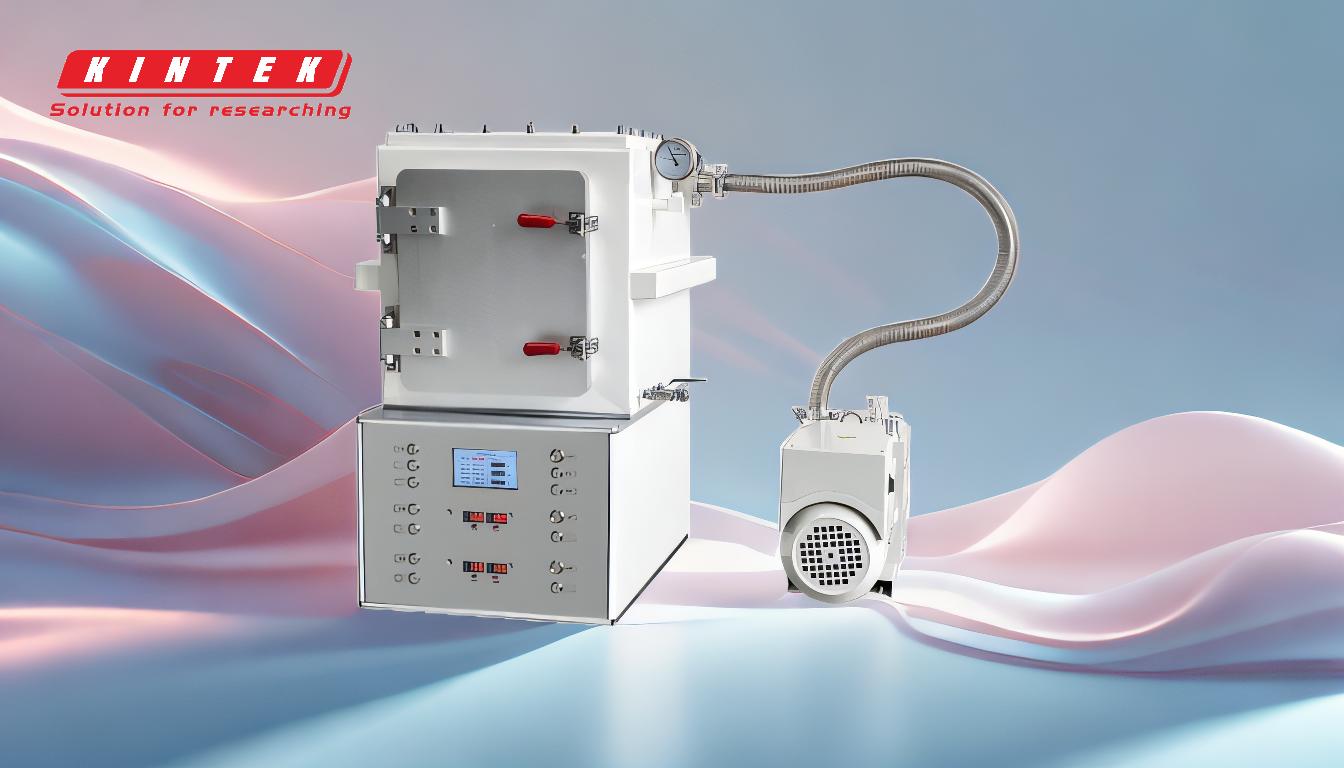
-
Basic Mechanism of DC Sputtering:
- DC sputtering is a PVD technique where a target material is bombarded with ionized gas molecules (usually argon ions) in a vacuum chamber.
- The high-energy ions collide with the target, causing atoms to be ejected or "sputtered" from the target surface.
- These sputtered atoms travel through the vacuum and deposit onto a substrate, forming a thin film.
-
Role of Ion Energy and Target Material:
- The efficiency of the sputtering process depends on the energy of the ions and the mass of the target atoms.
- Higher ion energy results in more atoms being ejected from the target.
- The mass of the target atoms also plays a role; heavier atoms require more energy to be sputtered.
-
Vacuum Environment:
- The process occurs in a vacuum chamber to minimize contamination and ensure a clean deposition environment.
- The vacuum allows the sputtered atoms to travel freely and deposit uniformly on the substrate.
-
Control and Consistency:
- The sputtering rate is tightly controlled to ensure a consistent deposition rate.
- Parameters such as ion flux density, target-substrate distance, and chamber pressure are carefully managed to achieve the desired film properties.
-
Applications of DC Sputtering:
- DC sputtering is commonly used for depositing conductive materials such as metals (e.g., gold, silver, copper) and alloys.
- It is widely used in the semiconductor industry for creating thin films in integrated circuits.
- Other applications include optical coatings, decorative finishes, and protective coatings.
-
Advantages of DC Sputtering:
- High deposition rates for conductive materials.
- Ability to deposit uniform and high-quality thin films.
- Suitable for a wide range of materials, including metals and alloys.
-
Limitations:
- DC sputtering is less effective for insulating materials due to charge buildup on the target surface.
- The process requires precise control of parameters, which can increase complexity and cost.
-
Mathematical Modeling:
- The sputtering rate can be calculated using the formula:
[
R_{\text{sputter}} = \left(\frac{\Phi}{2}\right) \times \left(\frac{n}{N_A}\right) \times \left(\frac{A}{d}\right) \times \left(\frac{v}{1 + \frac{v^2}{v_c^2}}\right)
]
where:
- (\Phi) is the ion flux density,
- (n) is the number of target atoms per unit volume,
- (N_A) is Avogadro's number,
- (A) is the atomic weight of the target material,
- (d) is the distance between the target and substrate,
- (v) is the average velocity of the sputtered atoms,
- (v_c) is the critical velocity.
- The sputtering rate can be calculated using the formula:
[
R_{\text{sputter}} = \left(\frac{\Phi}{2}\right) \times \left(\frac{n}{N_A}\right) \times \left(\frac{A}{d}\right) \times \left(\frac{v}{1 + \frac{v^2}{v_c^2}}\right)
]
where:
In summary, DC sputtering is a versatile and effective technique for depositing thin films of conductive materials. Its mechanism involves the bombardment of a target with high-energy ions, resulting in the ejection of target atoms that deposit onto a substrate. The process is highly controlled and offers numerous advantages, making it a cornerstone of modern thin-film deposition technologies.
Summary Table:
Aspect | Details |
---|---|
Mechanism | Bombardment of a target with high-energy ions to eject atoms onto a substrate. |
Key Parameters | Ion energy, target material properties, vacuum environment, and control. |
Applications | Semiconductor manufacturing, optical coatings, decorative finishes. |
Advantages | High deposition rates, uniform thin films, suitable for conductive materials. |
Limitations | Less effective for insulators, requires precise parameter control. |
Discover how DC sputtering can enhance your thin-film processes—contact our experts today!