Hot isostatic pressing (HIP) is a critical process used to densify materials and eliminate internal defects, ensuring high-performance end-use properties. The densification mechanism involves two primary stages: (1) plastic deformation of internal defects and pores under high external pressure, and (2) high-temperature creep and diffusion bonding to fully eliminate porosity. This process applies equal pressure (100–200 MPa) in all directions and utilizes high temperatures (1000–2200°C) to achieve densification. The steps include loading powder into a flexible mold, sealing it, applying pressure via a liquid medium, and sintering the material. HIP is widely used for materials like aluminum, titanium, and high-temperature alloys to enhance their structural integrity and performance.
Key Points Explained:
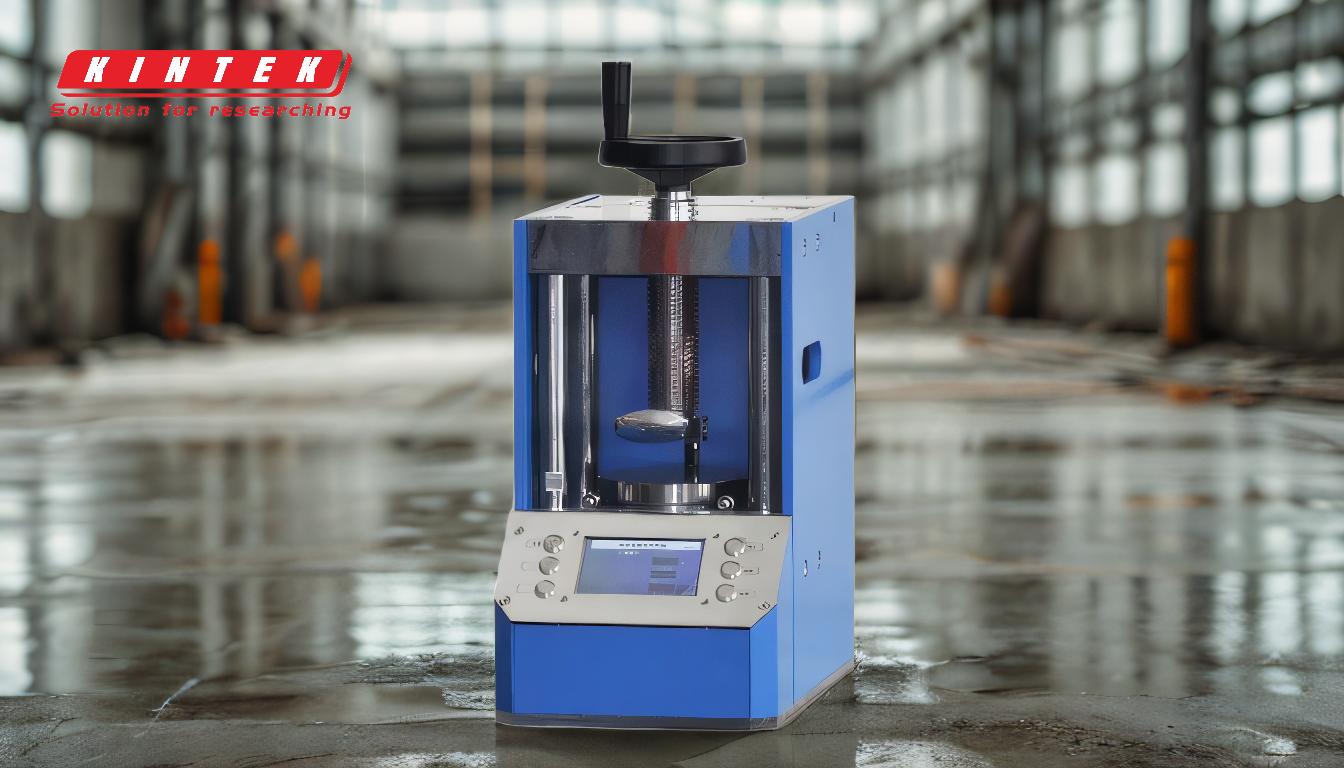
-
Purpose of Hot Isostatic Pressing:
- HIP is primarily used to eliminate internal defects such as porosity and voids in materials like aluminum, titanium, and high-temperature alloys. These defects often arise from uneven cooling rates during casting or forming processes.
- The process ensures that the material achieves optimal density and mechanical properties, meeting the highest standards for end-use performance.
- For more details on related equipment, see warm isostatic press.
-
Densification Mechanism:
- The densification process occurs in two distinct stages:
-
Stage 1: Plastic Deformation:
- Under high external pressure (greater than the material's high-temperature strength), internal defects and pores undergo plastic deformation.
- This leads to surface contact between particles, reducing porosity and initiating densification.
-
Stage 2: High-Temperature Creep and Diffusion Bonding:
- At lower external pressures (below the material's high-temperature strength), high temperatures facilitate creep and diffusion bonding.
- This stage fully eliminates residual porosity and defects, resulting in a homogeneous and dense material structure.
-
Stage 1: Plastic Deformation:
- The densification process occurs in two distinct stages:
-
Process Parameters:
- Pressure: HIP applies equal pressure (100–200 MPa) in all directions, ensuring uniform densification without distortion.
- Temperature: The process operates at high temperatures (1000–2200°C), which are essential for activating diffusion mechanisms and achieving full densification.
- These parameters are carefully controlled to suit the specific material being processed.
-
General Steps in HIP:
- Loading: The powder or preform is loaded into a flexible mold.
- Sealing: The mold is sealed to prevent contamination and ensure uniform pressure application.
- Pressure Application: Pressure is applied via a liquid medium in a pressure vessel, ensuring isotropic compression.
- Sintering/Densification: The material is sintered or densified under controlled temperature and pressure conditions.
- Cooling and Removal: After the process, the material is cooled, and the densified product is removed from the mold.
-
Applications of HIP:
- HIP is widely used in industries requiring high-performance materials, such as aerospace, automotive, and medical devices.
- It is particularly effective for processing castings and additive manufacturing components, where internal defects can compromise performance.
- The process is also used to bond dissimilar materials and repair defective components.
-
Advantages of HIP:
- Improved Material Properties: HIP enhances mechanical properties such as strength, fatigue resistance, and fracture toughness.
- Defect Elimination: It effectively removes porosity and internal defects, ensuring structural integrity.
- Versatility: HIP can be applied to a wide range of materials, including metals, ceramics, and composites.
-
Comparison with Other Processes:
- Unlike traditional sintering or forging, HIP applies uniform pressure in all directions, preventing distortion and ensuring consistent densification.
- The combination of high pressure and temperature distinguishes HIP from other densification methods, making it particularly effective for complex geometries and high-performance applications.
By understanding the densification mechanism and process parameters of HIP, manufacturers can optimize material performance and produce components with superior mechanical properties and reliability.
Summary Table:
Key Aspect | Details |
---|---|
Purpose | Eliminates internal defects like porosity and voids in materials. |
Densification Mechanism | 1. Plastic deformation under high pressure. 2. High-temperature creep and diffusion bonding. |
Process Parameters | Pressure: 100–200 MPa; Temperature: 1000–2200°C. |
Steps | Loading, sealing, pressure application, sintering, cooling, and removal. |
Applications | Aerospace, automotive, medical devices, and additive manufacturing. |
Advantages | Improves strength, fatigue resistance, and eliminates defects effectively. |
Discover how HIP can optimize your material performance—contact our experts today!