The primary difference between 2-plate and 3-plate molds lies in their design and functionality, particularly in how they handle the injection molding process and the gating system. A 2-plate mold is simpler and typically feeds material from the outer side of the cavity, often using side gates. In contrast, a 3-plate mold allows for more flexibility in gating, enabling material to be injected from any point in the cavity, often using pinpoint gates. This makes 3-plate molds more suitable for complex designs, especially when the product has large holes or requires internal gating.
Key Points Explained:
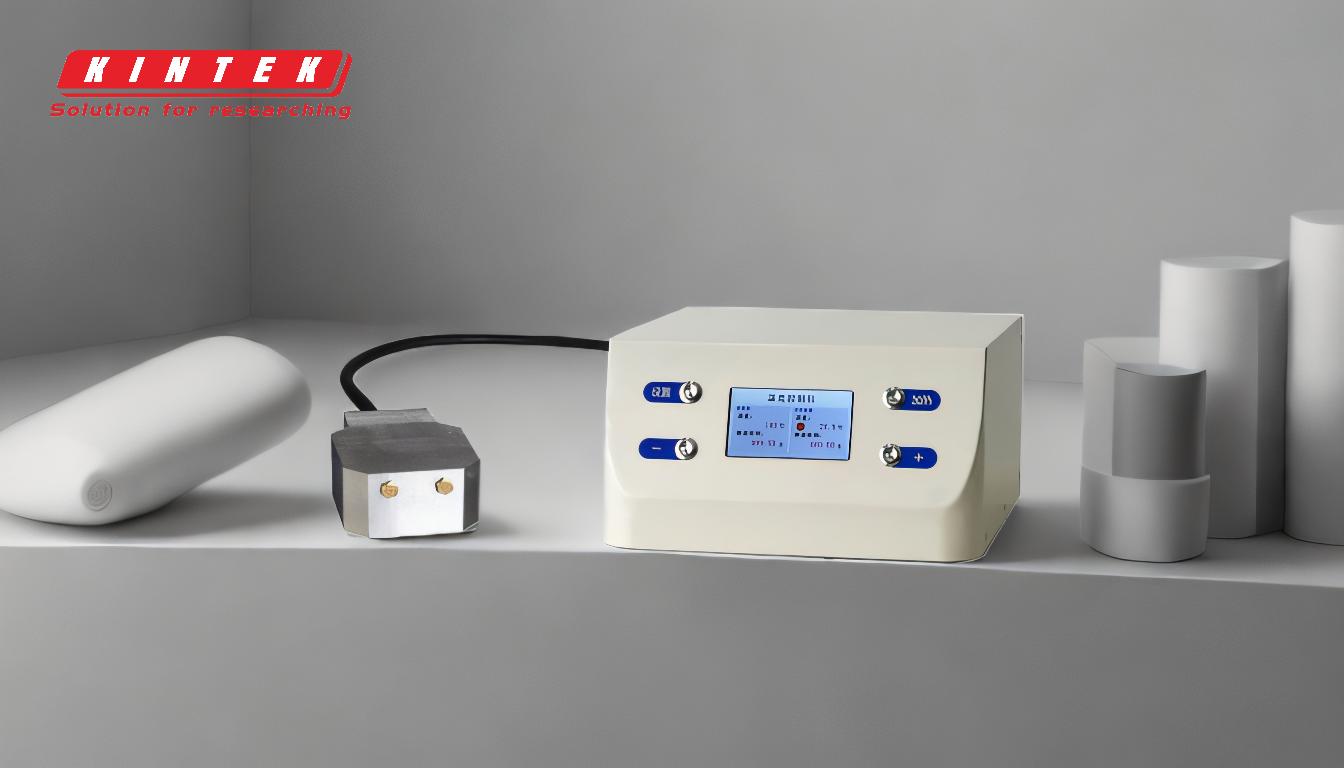
-
Design Complexity:
- 2-Plate Mold: Consists of two main plates—the cavity plate and the core plate. This design is simpler and more straightforward, making it easier to manufacture and maintain.
- 3-Plate Mold: Includes an additional plate (the runner plate) between the cavity and core plates. This extra plate adds complexity but provides more flexibility in the gating system.
-
Gating System:
- 2-Plate Mold: Typically uses side gates, which feed material from the outer side of the cavity. This is suitable for simpler designs where the gate location is not critical.
- 3-Plate Mold: Allows for pinpoint gates, enabling material to be injected from any point within the cavity. This is particularly useful for complex designs or when the product requires internal gating.
-
Material Flow:
- 2-Plate Mold: The material flow is generally more straightforward, but it may not be suitable for products with large holes or complex internal structures.
- 3-Plate Mold: Offers better control over material flow, making it ideal for products with intricate designs or large internal voids.
-
Application Suitability:
- 2-Plate Mold: Best suited for simpler, less complex products where the gating location is not a critical factor.
- 3-Plate Mold: More appropriate for complex products, especially those requiring internal gating or having large central holes.
-
Cost and Maintenance:
- 2-Plate Mold: Generally less expensive to manufacture and maintain due to its simpler design.
- 3-Plate Mold: More costly due to the additional plate and increased complexity, but it offers greater flexibility and control in the molding process.
-
Cycle Time:
- 2-Plate Mold: Typically has a shorter cycle time due to its simpler design and fewer moving parts.
- 3-Plate Mold: May have a longer cycle time due to the additional plate and more complex gating system, but this is often offset by the ability to produce more complex parts in a single cycle.
Summary Table:
Feature | 2-Plate Mold | 3-Plate Mold |
---|---|---|
Design Complexity | Simpler, 2 main plates | More complex, includes a runner plate |
Gating System | Side gates | Pinpoint gates |
Material Flow | Straightforward | Better control for complex designs |
Application | Simpler products | Complex products with internal gating |
Cost | Less expensive | More costly |
Cycle Time | Shorter | Longer |
Need help choosing the right mold for your project? Contact our experts today!