Blast furnaces and Electric Arc Furnaces (EAFs) are both used in the production of steel, but they differ significantly in their operation, energy sources, and applications. Blast furnaces are large, vertical structures that use coke, iron ore, and limestone to produce molten iron through a chemical reduction process. They are energy-intensive and primarily used in large-scale steel production. On the other hand, EAFs use electric arcs to melt scrap steel or direct reduced iron (DRI), making them more flexible and environmentally friendly. EAFs are often used for smaller-scale production and are capable of recycling scrap metal efficiently. The choice between the two depends on factors like production scale, raw material availability, and environmental considerations.
Key Points Explained:
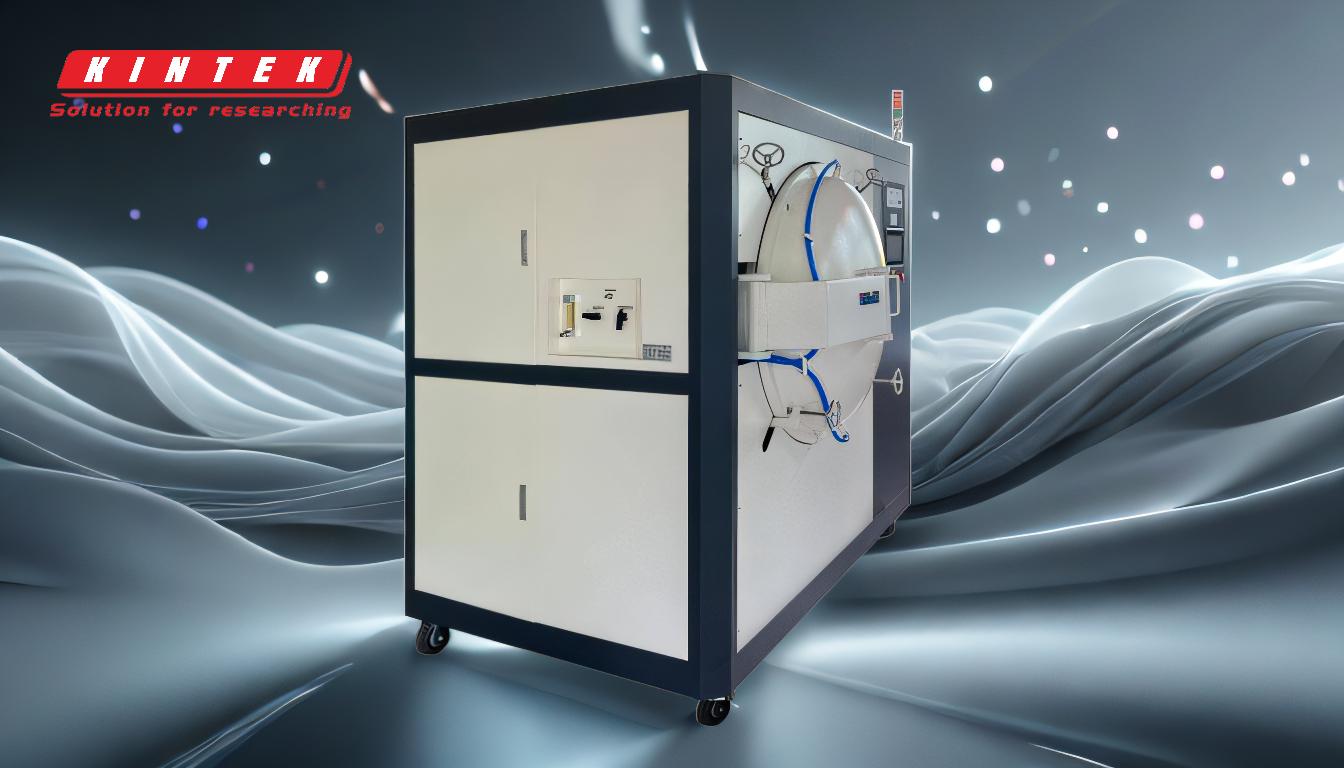
-
Operation and Process:
- Blast Furnace: Operates by blowing hot air into the furnace to combust coke, producing carbon monoxide which reduces iron ore to molten iron. This process is continuous and requires a steady supply of raw materials.
- Electric Arc Furnace (EAF): Uses high-voltage electric arcs to melt scrap steel or DRI. The process is batch-based, allowing for more flexibility in production schedules and material types.
-
Energy Source:
- Blast Furnace: Primarily relies on coke (a form of coal) as a reducing agent and energy source. This makes it highly dependent on fossil fuels.
- Electric Arc Furnace (EAF): Uses electricity as its primary energy source, which can be generated from renewable sources, making it more environmentally friendly.
-
Raw Materials:
- Blast Furnace: Requires iron ore, coke, and limestone. The process is less flexible in terms of raw material input.
- Electric Arc Furnace (EAF): Can use a variety of materials, including scrap steel and DRI, making it versatile and suitable for recycling.
-
Scale and Application:
- Blast Furnace: Typically used in large-scale steel production facilities. It is less adaptable to changes in production volume.
- Electric Arc Furnace (EAF): Suitable for both large and small-scale production. It is ideal for mini-mills and can quickly adjust to market demands.
-
Environmental Impact:
- Blast Furnace: Produces significant amounts of CO2 and other pollutants due to the combustion of coke.
- Electric Arc Furnace (EAF): Generally has a lower carbon footprint, especially when powered by renewable energy sources.
-
Cost and Efficiency:
- Blast Furnace: High initial capital cost and ongoing operational costs due to the need for continuous raw material supply and energy consumption.
- Electric Arc Furnace (EAF): Lower initial capital cost and operational flexibility can lead to cost savings, especially in regions with abundant scrap metal.
-
Temperature Control:
- Blast Furnace: Temperature control is less precise due to the nature of the combustion process.
- Electric Arc Furnace (EAF): Offers more precise temperature control, which is crucial for producing high-quality steel with specific properties.
In summary, while both blast furnaces and EAFs are essential for steel production, they cater to different needs and scales of operation. Blast furnaces are suited for large-scale, continuous production using raw materials, whereas EAFs offer flexibility, environmental benefits, and the ability to recycle scrap metal efficiently. The choice between the two technologies depends on various factors, including production scale, raw material availability, and environmental considerations.
Summary Table:
Aspect | Blast Furnace | Electric Arc Furnace (EAF) |
---|---|---|
Operation | Continuous process using coke, iron ore, and limestone to produce molten iron. | Batch-based process using electric arcs to melt scrap steel or DRI. |
Energy Source | Primarily coke (fossil fuel-dependent). | Electricity (can be sourced from renewables). |
Raw Materials | Iron ore, coke, and limestone. | Scrap steel, DRI, and other recyclable materials. |
Scale & Application | Large-scale production; less adaptable to changes. | Suitable for both large and small-scale production; highly flexible. |
Environmental Impact | High CO2 emissions and pollutants. | Lower carbon footprint, especially with renewable energy. |
Cost & Efficiency | High capital and operational costs. | Lower initial costs and operational flexibility. |
Temperature Control | Less precise due to combustion process. | More precise, enabling high-quality steel production. |
Need help choosing the right furnace for your steel production? Contact our experts today for tailored advice!