Pneumatic and hydraulic presses are both widely used in manufacturing and industrial applications, but they operate on different principles and are suited for different tasks. Pneumatic presses use compressed air to generate force, making them faster and more suitable for lighter tasks. Hydraulic presses, on the other hand, use fluid pressure to generate significantly higher force, making them ideal for heavy-duty applications. A heated hydraulic press combines hydraulic force with heating elements, enabling processes like molding, laminating, or bonding that require both pressure and heat. The choice between these presses depends on factors like required force, speed, precision, and cost.
Key Points Explained:
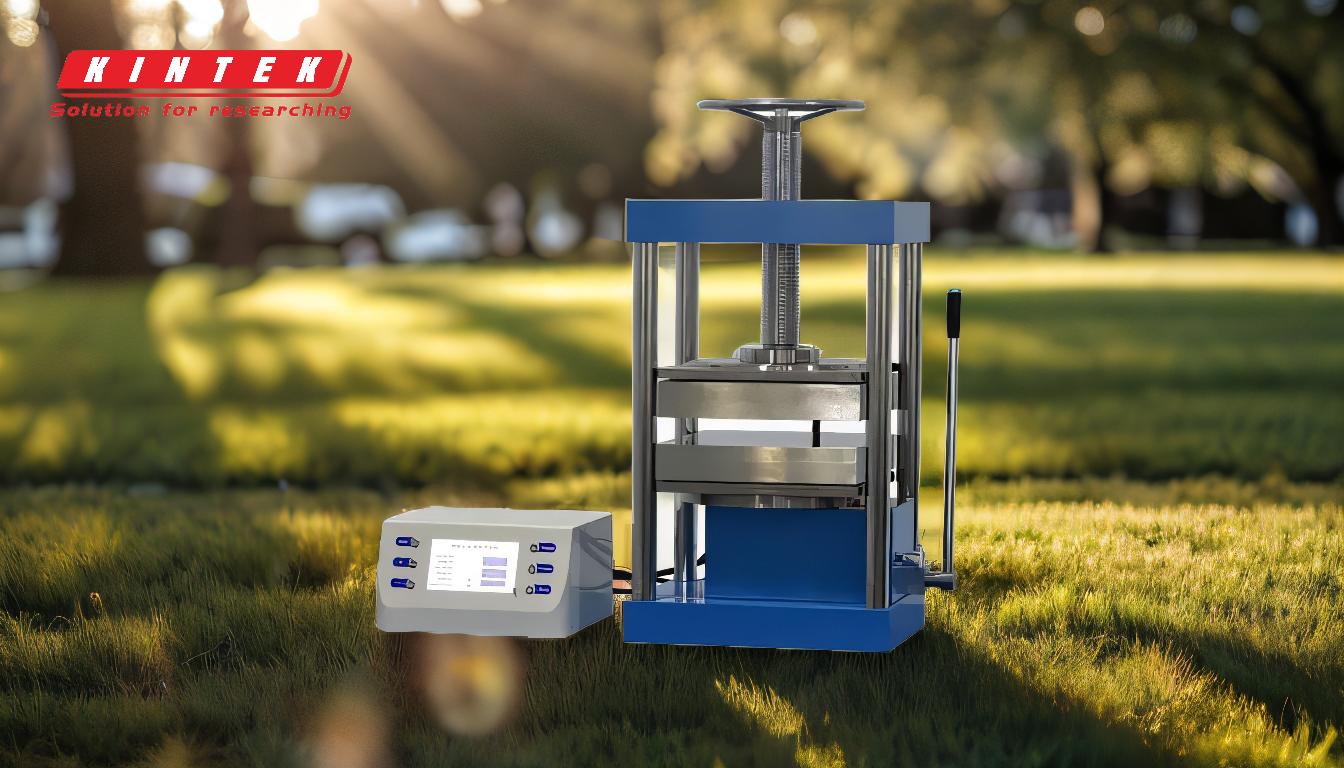
-
Operating Principle:
- Pneumatic Press: Operates using compressed air. When air is pressurized, it moves a piston to generate force. The force is typically lower compared to hydraulic presses but is delivered quickly.
- Hydraulic Press: Uses a hydraulic fluid, usually oil, to transmit force. A pump pressurizes the fluid, which then moves a piston to generate much higher force than pneumatic systems.
-
Force Generation:
- Pneumatic presses are limited in the force they can generate, typically up to a few tons. They are ideal for applications requiring lighter force, such as assembly or stamping.
- Hydraulic presses can generate immense force, often in the range of hundreds or thousands of tons. This makes them suitable for heavy-duty tasks like metal forming, forging, or crushing.
-
Speed and Precision:
- Pneumatic presses are faster in operation due to the quick movement of compressed air. They are well-suited for high-speed, repetitive tasks.
- Hydraulic presses are slower but offer greater precision and control over force application. This is crucial for tasks requiring consistent pressure over time.
-
Applications:
- Pneumatic presses are commonly used in industries like electronics, automotive assembly, and packaging, where speed and lighter force are sufficient.
- Hydraulic presses are used in heavy industries such as metalworking, construction, and aerospace, where high force is necessary. A heated hydraulic press is particularly useful for processes like composite material molding or rubber vulcanization, where heat and pressure are required simultaneously.
-
Cost and Maintenance:
- Pneumatic systems are generally less expensive to purchase and maintain. They have fewer components and are easier to repair.
- Hydraulic systems are more costly due to their complexity and the need for regular maintenance of hydraulic fluid and seals. However, their durability and power often justify the investment for heavy-duty applications.
-
Energy Efficiency:
- Pneumatic systems are less energy-efficient because compressing air requires significant energy, and some energy is lost as heat.
- Hydraulic systems are more energy-efficient for high-force applications, as hydraulic fluid is incompressible and transfers energy more effectively.
-
Environmental Considerations:
- Pneumatic systems can be noisy due to the release of compressed air and may require noise-dampening measures.
- Hydraulic systems pose a risk of fluid leaks, which can be environmentally hazardous. Proper maintenance and spill containment are essential.
In summary, the choice between a pneumatic press and a hydraulic press depends on the specific requirements of the task, including the force needed, speed, precision, and budget. A heated hydraulic press adds the capability of applying heat, making it indispensable for specialized applications like composite manufacturing or material bonding.
Summary Table:
Aspect | Pneumatic Press | Hydraulic Press |
---|---|---|
Operating Principle | Uses compressed air to generate force. | Uses hydraulic fluid (oil) to generate higher force. |
Force Generation | Up to a few tons; ideal for lighter tasks. | Hundreds or thousands of tons; suited for heavy-duty tasks. |
Speed and Precision | Faster operation, but less precise. | Slower operation with greater precision and control. |
Applications | Electronics, automotive assembly, packaging. | Metalworking, construction, aerospace; heated versions for molding and bonding. |
Cost and Maintenance | Less expensive and easier to maintain. | More costly and requires regular maintenance. |
Energy Efficiency | Less energy-efficient due to air compression. | More energy-efficient for high-force applications. |
Environmental Impact | Noisy; may need noise-dampening measures. | Risk of fluid leaks; requires spill containment. |
Need help choosing the right press for your application? Contact our experts today for personalized advice!