Annealing and tempering are both heat treatment processes used to alter the properties of metals, but they serve different purposes and are applied under different conditions. Annealing is primarily used to soften metals, reduce internal stresses, and improve ductility, making the material easier to machine or form. It involves heating the metal to a specific temperature, holding it there for a period, and then slowly cooling it. Tempering, on the other hand, is used to increase the toughness of hardened steels by reducing brittleness. It involves heating the metal to a temperature below its critical point, holding it, and then cooling it, often in air. The key differences lie in their objectives, temperature ranges, cooling rates, and the resulting material properties.
Key Points Explained:
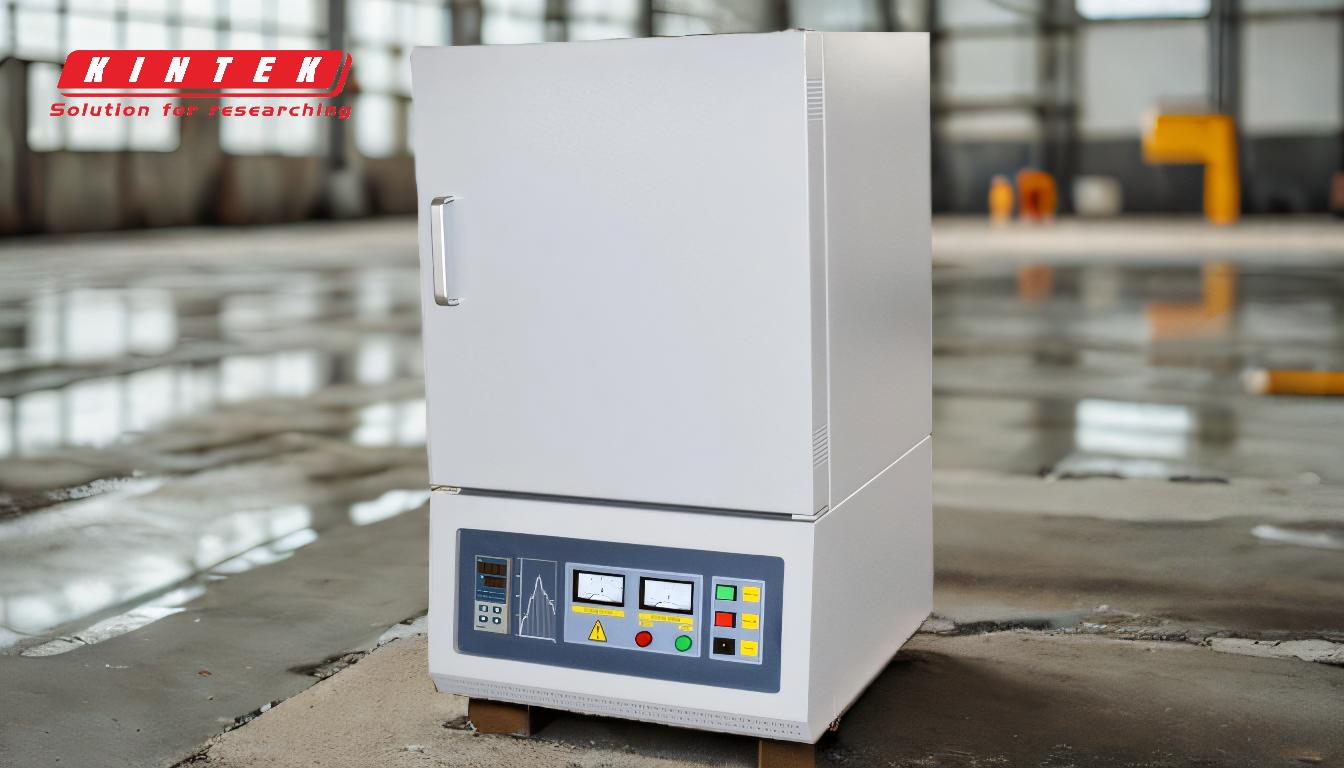
-
Purpose and Objectives:
- Annealing: The primary goal of annealing is to soften the metal, relieve internal stresses, and improve ductility and machinability. It is often used after cold working processes to make the material easier to work with.
- Tempering: Tempering is aimed at reducing the brittleness of hardened steels while maintaining a good balance of hardness and toughness. It is typically performed after quenching to achieve the desired mechanical properties.
-
Temperature Ranges:
- Annealing: Annealing involves heating the metal to a temperature above its recrystallization temperature but below its melting point. For steel, this is typically between 700°C to 900°C, depending on the type of steel.
- Tempering: Tempering is done at lower temperatures, usually between 150°C to 650°C. The exact temperature depends on the desired balance between hardness and toughness.
-
Cooling Rates:
- Annealing: The cooling process in annealing is slow, often done in a furnace or by burying the metal in an insulating material. This slow cooling allows the metal to form a more uniform microstructure, which contributes to its softness and ductility.
- Tempering: Tempering involves cooling the metal at a controlled rate, often in air. The cooling rate is faster than in annealing but slower than in quenching, which helps in achieving the desired toughness without excessive brittleness.
-
Resulting Material Properties:
- Annealing: After annealing, the metal is softer, more ductile, and has reduced internal stresses. This makes it easier to machine, form, or work with in subsequent processes.
- Tempering: Tempering results in a material that is less brittle than after quenching but still retains a significant amount of hardness. The exact properties depend on the tempering temperature and time.
-
Applications:
- Annealing: Annealing is commonly used in the manufacturing of components that require high ductility and low hardness, such as sheet metal, wires, and certain types of structural components.
- Tempering: Tempering is widely used in the production of tools, blades, and other components that need a balance of hardness and toughness to withstand impact and wear.
-
Microstructural Changes:
- Annealing: During annealing, the metal's microstructure undergoes recrystallization, leading to the formation of new, strain-free grains. This process reduces dislocations and internal stresses, resulting in a softer material.
- Tempering: Tempering causes the decomposition of martensite (a hard, brittle phase formed during quenching) into a more stable structure, such as tempered martensite or bainite. This transformation reduces brittleness while maintaining some of the hardness.
In summary, while both annealing and tempering are heat treatment processes that involve heating and cooling metals, they are used for different purposes and result in different material properties. Annealing is focused on softening and stress relief, whereas tempering aims to balance hardness and toughness. Understanding these differences is crucial for selecting the appropriate heat treatment process for a given application.
Summary Table:
Aspect | Annealing | Tempering |
---|---|---|
Purpose | Softens metal, relieves stress, improves ductility | Reduces brittleness, balances hardness and toughness |
Temperature Range | 700°C to 900°C (steel) | 150°C to 650°C |
Cooling Rate | Slow (furnace or insulating material) | Controlled (often in air) |
Resulting Properties | Softer, more ductile, reduced internal stress | Less brittle, retains hardness, improved toughness |
Applications | Sheet metal, wires, structural components | Tools, blades, impact-resistant components |
Microstructural Change | Recrystallization, strain-free grains | Decomposition of martensite into tempered martensite or bainite |
Need help choosing the right heat treatment process? Contact our experts today for personalized guidance!