Chemical vapor deposition (CVD) and physical vapor deposition (PVD) are two widely used techniques for depositing thin films onto substrates, but they differ significantly in their processes, applications, and outcomes. CVD involves chemical reactions between gaseous precursors and the substrate at high temperatures, leading to the formation of a solid coating. This process is multidirectional and can produce high-quality, uniform films, but it often requires elevated temperatures and may result in corrosive byproducts or impurities. PVD, on the other hand, relies on physical vaporization of materials, depositing them directly onto the substrate in a line-of-sight manner. PVD typically operates at lower temperatures, avoids corrosive byproducts, and offers high material utilization efficiency, though deposition rates are generally lower. The choice between CVD and PVD depends on the specific requirements of the application, such as temperature tolerance, film quality, and material compatibility.
Key Points Explained:
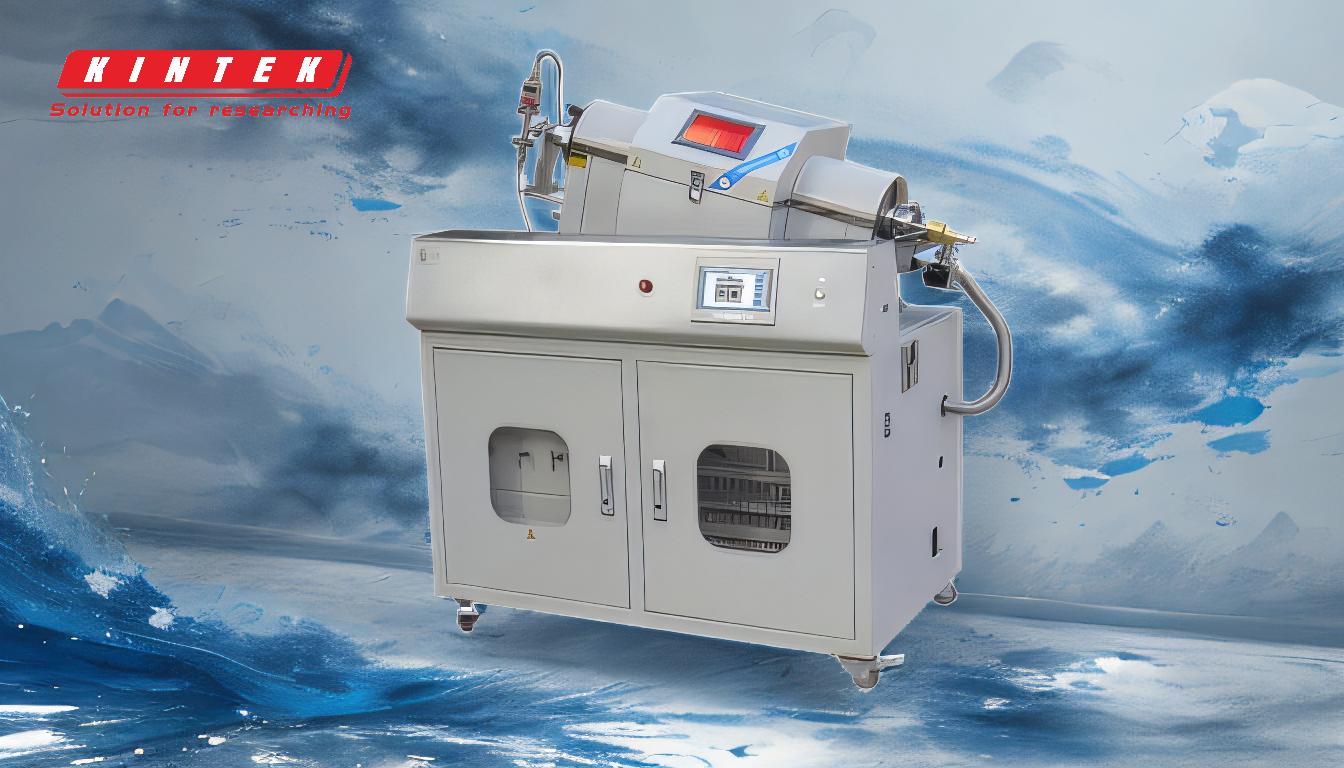
-
Process Mechanism:
- CVD: Involves chemical reactions between gaseous precursors and the substrate, leading to the formation of a solid coating. This process is multidirectional, meaning the coating can form uniformly on complex geometries.
- PVD: Relies on physical vaporization of materials, such as sputtering or evaporation, which are then deposited onto the substrate in a line-of-sight manner. This limits the uniformity on complex shapes but avoids chemical reactions.
-
Temperature Requirements:
- CVD: Typically requires high temperatures, often in the range of 500°–1100°C, to facilitate the chemical reactions necessary for film growth.
- PVD: Operates at lower temperatures, making it suitable for substrates that cannot withstand high heat. For example, electron beam physical vapor deposition (EBPVD) can achieve high deposition rates at relatively low temperatures.
-
Byproducts and Impurities:
- CVD: Can produce corrosive gaseous byproducts during the chemical reactions, which may leave impurities in the deposited film.
- PVD: Does not involve chemical reactions, so it avoids the formation of corrosive byproducts and impurities, resulting in cleaner films.
-
Deposition Rates and Efficiency:
- CVD: Generally offers higher deposition rates compared to PVD, making it suitable for applications requiring thick or rapid coatings.
- PVD: Typically has lower deposition rates, but techniques like EBPVD can achieve rates ranging from 0.1 to 100 μm/min with high material utilization efficiency.
-
Applications:
- CVD: Widely used for depositing high-quality, large-area films, such as graphene, carbon nanotubes, and various metallic, ceramic, and semiconducting materials. It is also used in applications like electronic transistors, corrosion coatings, and transparent conductors.
- PVD: Commonly employed for applications requiring precise, high-purity coatings, such as in the aerospace, automotive, and tooling industries. It is also used for decorative coatings and optical films.
-
Material Compatibility:
- CVD: Can deposit a wide range of materials, including metals, nonmetals (e.g., carbon, silicon), carbides, nitrides, oxides, and intermetallics. It is particularly effective for complex materials like GaN nanowires.
- PVD: Primarily used for depositing metals and alloys, though it can also be adapted for certain ceramics and semiconductors.
-
Film Quality and Uniformity:
- CVD: Produces highly uniform and conformal coatings, even on complex geometries, due to its multidirectional deposition process.
- PVD: Provides excellent film purity and density but may struggle with uniformity on non-planar or intricate surfaces due to its line-of-sight nature.
In summary, the choice between chemical vapor deposition and physical vapor deposition depends on the specific requirements of the application, including temperature constraints, desired film properties, and material compatibility. Both techniques have unique advantages and limitations, making them suitable for different industrial and research applications.
Summary Table:
Aspect | CVD (Chemical Vapor Deposition) | PVD (Physical Vapor Deposition) |
---|---|---|
Process Mechanism | Chemical reactions between gaseous precursors and substrate; multidirectional deposition. | Physical vaporization of materials; line-of-sight deposition. |
Temperature | High (500°–1100°C) | Lower, suitable for heat-sensitive substrates. |
Byproducts/Impurities | Corrosive byproducts and impurities possible. | No corrosive byproducts; cleaner films. |
Deposition Rates | Higher rates, suitable for thick or rapid coatings. | Lower rates, but high material efficiency. |
Applications | Graphene, carbon nanotubes, electronic transistors, corrosion coatings, transparent conductors. | Aerospace, automotive, tooling industries; decorative and optical coatings. |
Material Compatibility | Metals, nonmetals, carbides, nitrides, oxides, intermetallics. | Primarily metals and alloys; some ceramics and semiconductors. |
Film Quality | Highly uniform and conformal coatings on complex geometries. | High purity and density; limited uniformity on intricate surfaces. |
Need help choosing between CVD and PVD for your application? Contact our experts today for tailored advice!