The coreless and channel induction furnaces are two distinct types of induction furnaces used in metal melting and heating applications. The coreless induction furnace is characterized by its absence of a magnetic core, relying on a coil to generate an electromagnetic field that induces eddy currents in the metal, leading to heating. It is versatile, suitable for a wide range of metals, and allows for easy alloy changes. In contrast, the channel induction furnace features a molten metal loop that acts as a secondary winding, with a magnetic core to enhance efficiency. It is typically used for continuous melting of specific metals and is more energy-efficient for large-scale operations. The choice between the two depends on factors such as the type of metal, required melting capacity, and operational flexibility.
Key Points Explained:
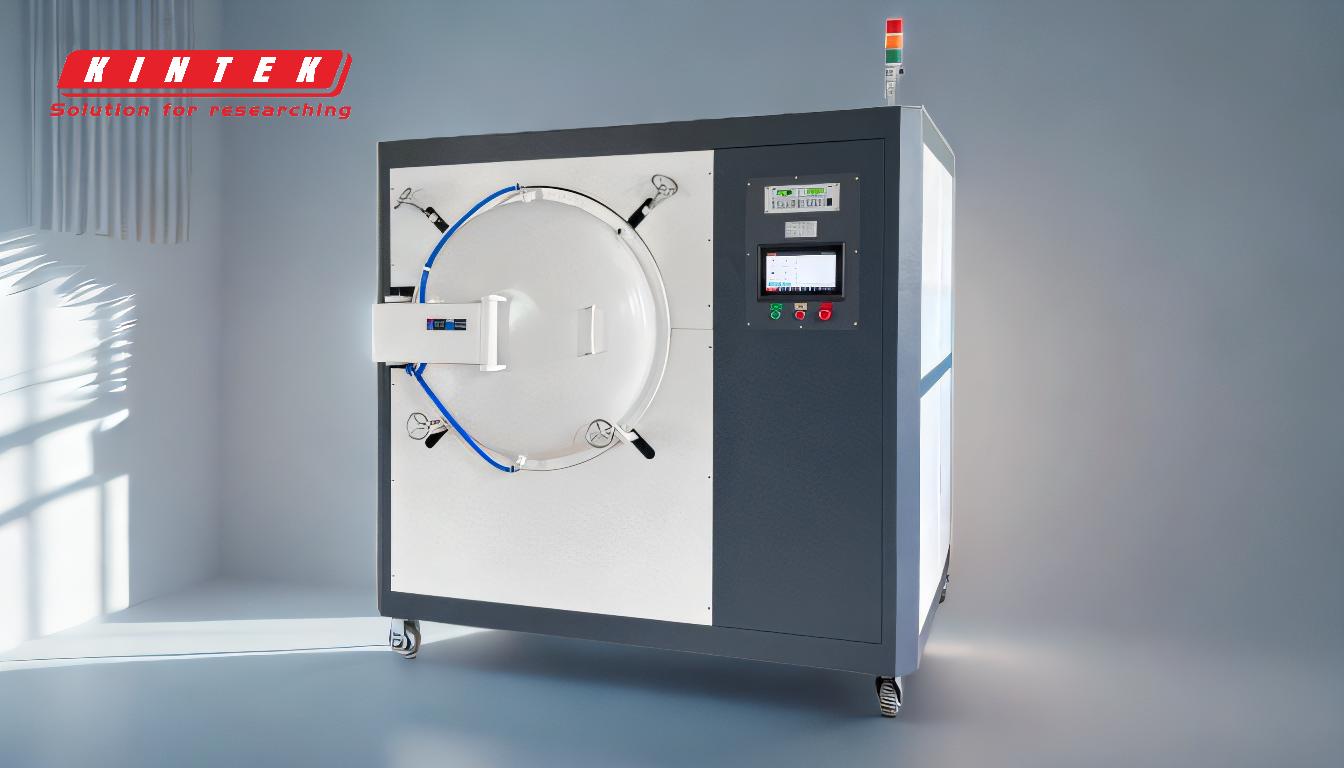
-
Coreless Induction Furnace:
- Design: The coreless induction furnace lacks a magnetic core. Instead, it uses a coil to create an electromagnetic field that induces eddy currents in the metal, causing it to heat up.
- Versatility: This type of furnace is highly versatile and can be used for melting a wide range of metals, including steel, iron, copper, and aluminum.
- Alloy Changes: One of the key advantages of the coreless induction furnace is the ease with which alloy changes can be made, making it ideal for foundries that require frequent changes in metal composition.
- Applications: It is commonly used in small to medium-sized foundries, as well as in laboratories for research and development purposes.
-
Channel Induction Furnace:
- Design: The channel induction furnace features a molten metal loop that acts as a secondary winding. It includes a magnetic core to enhance the efficiency of the electromagnetic induction process.
- Efficiency: This design makes the channel induction furnace more energy-efficient, particularly for large-scale operations. The magnetic core helps to concentrate the magnetic field, reducing energy losses.
- Continuous Melting: The channel induction furnace is typically used for continuous melting of specific metals, such as iron and non-ferrous metals. It is well-suited for applications where a consistent supply of molten metal is required.
- Applications: It is commonly used in large foundries and in industries where high-volume, continuous melting is necessary.
-
Comparison of Coreless and Channel Induction Furnaces:
- Energy Efficiency: The channel induction furnace is generally more energy-efficient than the coreless induction furnace, especially for large-scale operations. The presence of a magnetic core in the channel furnace reduces energy losses, making it more suitable for continuous, high-volume melting.
- Flexibility: The coreless induction furnace offers greater flexibility in terms of the types of metals that can be melted and the ease of alloy changes. This makes it more suitable for foundries that require frequent changes in metal composition.
- Operational Scale: The coreless induction furnace is typically used in smaller to medium-sized operations, while the channel induction furnace is more commonly used in large-scale industrial applications.
- Maintenance: The coreless induction furnace may require more frequent maintenance due to the absence of a magnetic core, which can lead to higher wear and tear on the coil. The channel induction furnace, with its magnetic core, tends to have lower maintenance requirements.
-
IGBT Induction Furnace:
- Technology: The IGBT induction furnace utilizes Insulated Gate Bipolar Transistor (IGBT) technology, which offers improved efficiency, precise control, and reduced energy consumption compared to traditional induction furnaces.
- Advantages: IGBT technology allows for better control of the melting process, leading to higher quality melts and reduced energy losses. It also enables faster heating and cooling cycles, improving overall productivity.
- Applications: IGBT induction furnaces are used in both coreless and channel induction furnace designs, offering the benefits of advanced technology across different types of induction melting applications.
In summary, the choice between a coreless and channel induction furnace depends on the specific requirements of the operation, including the type of metal, the scale of production, and the need for flexibility in alloy changes. The IGBT induction furnace technology further enhances the efficiency and control of both types of furnaces, making it a valuable option for modern metal melting applications.
Summary Table:
Feature | Coreless Induction Furnace | Channel Induction Furnace |
---|---|---|
Design | No magnetic core, uses a coil | Molten metal loop, magnetic core |
Versatility | High, suitable for various metals | Limited, specific metals |
Alloy Changes | Easy and frequent | Less frequent |
Energy Efficiency | Moderate | High for large-scale operations |
Operational Scale | Small to medium-sized operations | Large-scale industrial use |
Maintenance | Higher due to coil wear | Lower with magnetic core |
Need help choosing the right induction furnace for your needs? Contact our experts today!