Chemical Vapor Deposition (CVD) and Atomic Layer Deposition (ALD) are both advanced thin-film deposition techniques used in various industries, including semiconductor manufacturing, optics, and coatings. While they share some similarities, they differ significantly in their mechanisms, precision, and applications. CVD involves chemical reactions between gaseous precursors and a substrate to form thin films, often requiring high temperatures and offering high deposition rates. ALD, on the other hand, relies on sequential, self-limiting surface reactions to deposit films layer by layer, providing exceptional control over film thickness and uniformity, albeit at slower deposition rates. Below, we explore the key differences between CVD and ALD in detail.
Key Points Explained:
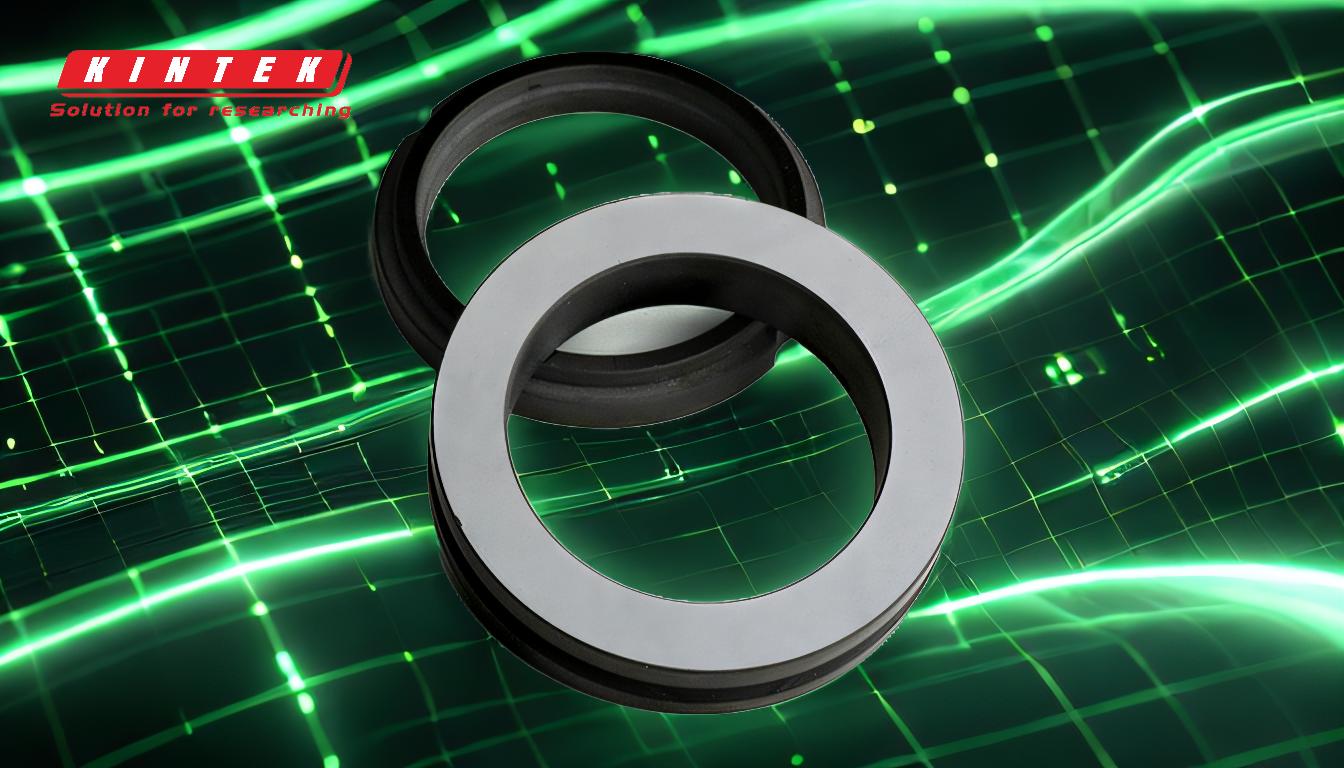
-
Deposition Mechanism:
- CVD: In CVD, gaseous precursors react or decompose on a heated substrate surface to form a solid film. The process is continuous and can involve multiple precursors simultaneously, leading to faster deposition rates. The chemical reactions occur in the gas phase or on the substrate surface, resulting in a relatively thick film in a single step.
- ALD: ALD operates through sequential, self-limiting surface reactions. Each cycle introduces one precursor at a time, which chemically bonds to the substrate surface in a controlled manner. The process repeats with alternating precursors, building the film one atomic layer at a time. This ensures precise control over film thickness and uniformity.
-
Precision and Control:
- CVD: While CVD offers high deposition rates, it lacks the atomic-level precision of ALD. The continuous nature of the process can lead to variations in film thickness, especially on complex geometries or uneven surfaces.
- ALD: ALD excels in precision, allowing for the deposition of ultra-thin films with atomic-level accuracy. This makes it ideal for applications requiring exact thickness control, such as in nanoscale semiconductor devices.
-
Temperature Requirements:
- CVD: CVD typically requires high temperatures (often 850-1100°C) to drive the chemical reactions. This can limit its use with temperature-sensitive materials or substrates.
- ALD: ALD can often be performed at lower temperatures, making it suitable for delicate materials or substrates that cannot withstand high heat.
-
Applications:
- CVD: CVD is widely used for depositing a variety of materials, including metals, ceramics, and compounds, on large surfaces. It is commonly employed in semiconductor manufacturing, protective coatings, and optical applications.
- ALD: ALD is preferred for applications requiring ultra-thin, conformal coatings, such as in advanced semiconductor devices, MEMS (Micro-Electro-Mechanical Systems), and nanotechnology.
-
Equipment and Complexity:
- CVD: CVD systems are relatively simple and cost-effective, making them suitable for large-scale industrial applications. However, they may require additional components like plasma or laser assistance to reduce reaction temperatures.
- ALD: ALD systems are more complex due to the need for precise precursor dosing and sequencing. This complexity often results in higher equipment costs and slower deposition rates.
-
Material Versatility:
- CVD: CVD can deposit a wide range of materials, including metals, non-metals, alloys, and ceramics. It is particularly effective for creating high-purity, dense films with good crystallinity.
- ALD: ALD is also versatile but is often limited to materials that can form self-limiting surface reactions. However, it is highly effective for depositing ultra-thin films of oxides, nitrides, and other compounds.
In summary, CVD and ALD are complementary techniques, each with its own strengths and limitations. CVD is ideal for high-throughput applications requiring thick, uniform films, while ALD is the go-to method for applications demanding atomic-level precision and conformal coatings. Understanding these differences is crucial for selecting the appropriate technique based on the specific requirements of the application.
Summary Table:
Aspect | CVD | ALD |
---|---|---|
Deposition Mechanism | Continuous chemical reactions with multiple precursors. | Sequential, self-limiting surface reactions, one precursor at a time. |
Precision | High deposition rates but less atomic-level precision. | Atomic-level precision for ultra-thin, uniform films. |
Temperature | High temperatures (850-1100°C), limiting use with sensitive materials. | Lower temperatures, suitable for delicate materials. |
Applications | Semiconductor manufacturing, protective coatings, optics. | Advanced semiconductors, MEMS, nanotechnology. |
Equipment | Relatively simple and cost-effective. | More complex, higher costs, and slower deposition rates. |
Material Versatility | Wide range of materials, including metals, ceramics, and alloys. | Limited to materials with self-limiting reactions, ideal for oxides. |
Need help choosing between CVD and ALD for your application? Contact our experts today!