CVD (Chemical Vapor Deposition) and PVD (Physical Vapor Deposition) are two widely used coating technologies, each with distinct processes, advantages, and applications. CVD involves chemical reactions between gaseous precursors and the substrate at high temperatures, resulting in multidirectional deposition and the ability to coat complex geometries. PVD, on the other hand, relies on the physical vaporization of solid materials, depositing them in a line-of-sight manner at lower temperatures. The choice between CVD and PVD depends on factors such as substrate material, desired coating properties, and application requirements.
Key Points Explained:
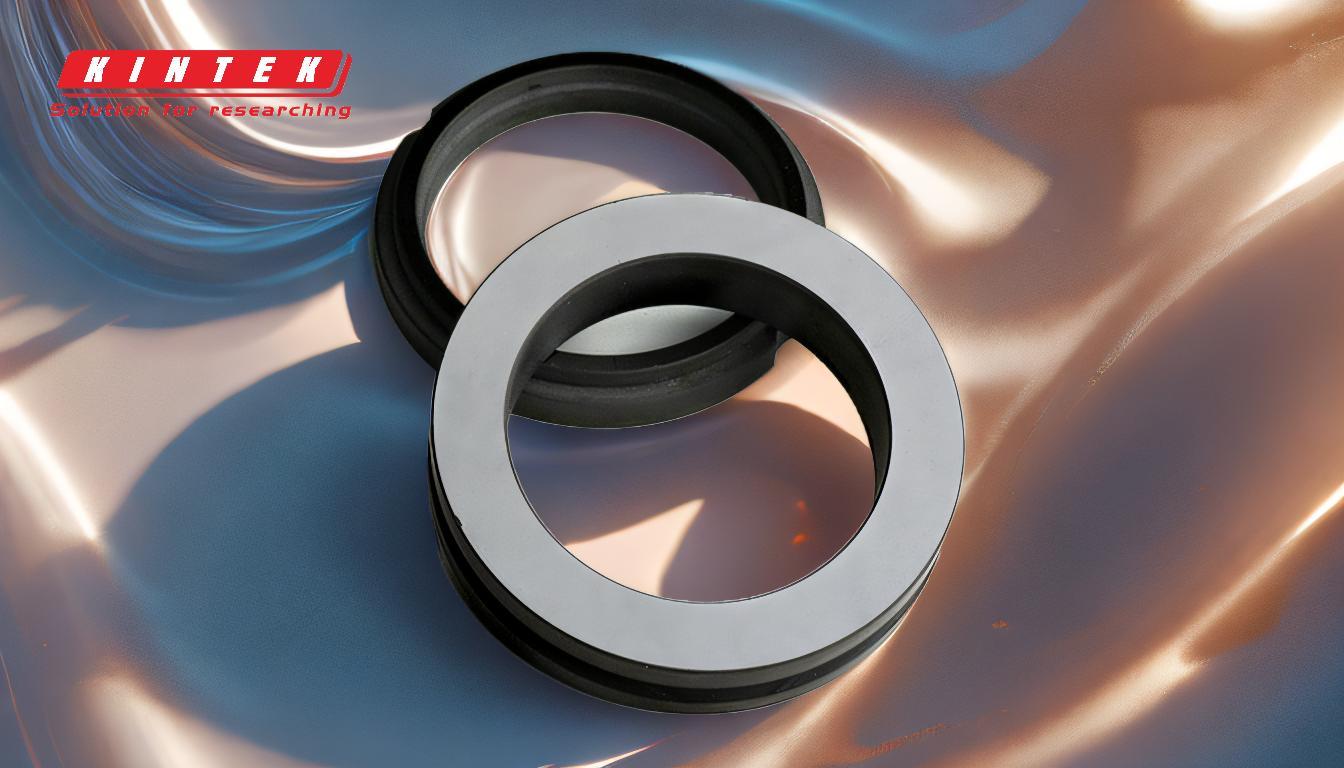
-
Deposition Mechanism:
- CVD: Involves chemical reactions between gaseous precursors and the substrate. The process is multidirectional, allowing for uniform coating of complex shapes, holes, and deep recesses.
- PVD: Relies on the physical vaporization of solid materials, which are then deposited onto the substrate in a line-of-sight manner. This limits its ability to coat complex geometries uniformly.
-
Temperature Requirements:
- CVD: Operates at high temperatures, typically between 450°C and 1050°C. This high-temperature environment facilitates chemical reactions but can also lead to thermal stress and fine cracks in the coating.
- PVD: Operates at lower temperatures, usually between 250°C and 450°C. This makes it suitable for temperature-sensitive substrates and reduces the risk of thermal damage.
-
Coating Material and Thickness:
- CVD: Uses gaseous precursors, which react to form a solid coating. CVD can produce thicker coatings (10~20μm) and is often used for applications requiring high wear resistance.
- PVD: Uses solid materials that are vaporized and deposited onto the substrate. PVD coatings are typically thinner (3~5μm) but offer excellent hardness and adhesion.
-
Coating Properties:
- CVD: Produces coatings with high throwing power, making it ideal for coating complex shapes and deep recesses. However, the high temperatures can lead to tensile stress and fine cracks.
- PVD: Forms compressive stress during cooling, resulting in coatings with high hardness and excellent adhesion. PVD coatings are also smoother and more uniform compared to CVD.
-
Applications:
- CVD: Commonly used in applications requiring thick, wear-resistant coatings, such as cutting tools, semiconductor devices, and wear-resistant components.
- PVD: Preferred for applications requiring thin, hard coatings with high precision, such as decorative coatings, optical coatings, and precision tools.
-
Economic and Operational Considerations:
- CVD: Often more economical due to high deposition rates and the ability to produce thick coatings. It does not require an ultra-high vacuum, which can reduce operational costs.
- PVD: While deposition rates are generally lower, PVD offers high material utilization efficiency and can be carried out at lower temperatures, reducing energy consumption.
In summary, the choice between CVD and PVD depends on the specific requirements of the application, including the substrate material, desired coating properties, and operational constraints. CVD is ideal for complex geometries and thick coatings, while PVD excels in producing thin, hard coatings with excellent adhesion and surface finish.
Summary Table:
Aspect | CVD | PVD |
---|---|---|
Deposition Mechanism | Chemical reactions with gaseous precursors; multidirectional deposition | Physical vaporization of solid materials; line-of-sight deposition |
Temperature | High (450°C–1050°C) | Low (250°C–450°C) |
Coating Thickness | Thicker (10~20μm) | Thinner (3~5μm) |
Coating Properties | High throwing power, uniform on complex shapes; tensile stress | High hardness, excellent adhesion; smoother and more uniform |
Applications | Cutting tools, semiconductors, wear-resistant components | Decorative coatings, optical coatings, precision tools |
Economic Considerations | High deposition rates, economical for thick coatings | Lower deposition rates, high material efficiency, energy-efficient |
Need help choosing the right coating solution? Contact our experts today for tailored advice!