Sintering and fusion (or melting) are both processes used to join or consolidate materials, but they differ significantly in their mechanisms, energy requirements, and applications. Sintering involves compacting and bonding particles of a material using heat and pressure without liquefying the material, making it a lower-energy process. Fusion, on the other hand, requires heating a material to its melting point, turning it into a liquid state before it solidifies into a new form. While fusion is ideal for creating strong, homogenous bonds, sintering is more suitable for creating porous or complex structures with controlled properties. Below, the key differences and applications of these processes are explained in detail.
Key Points Explained:
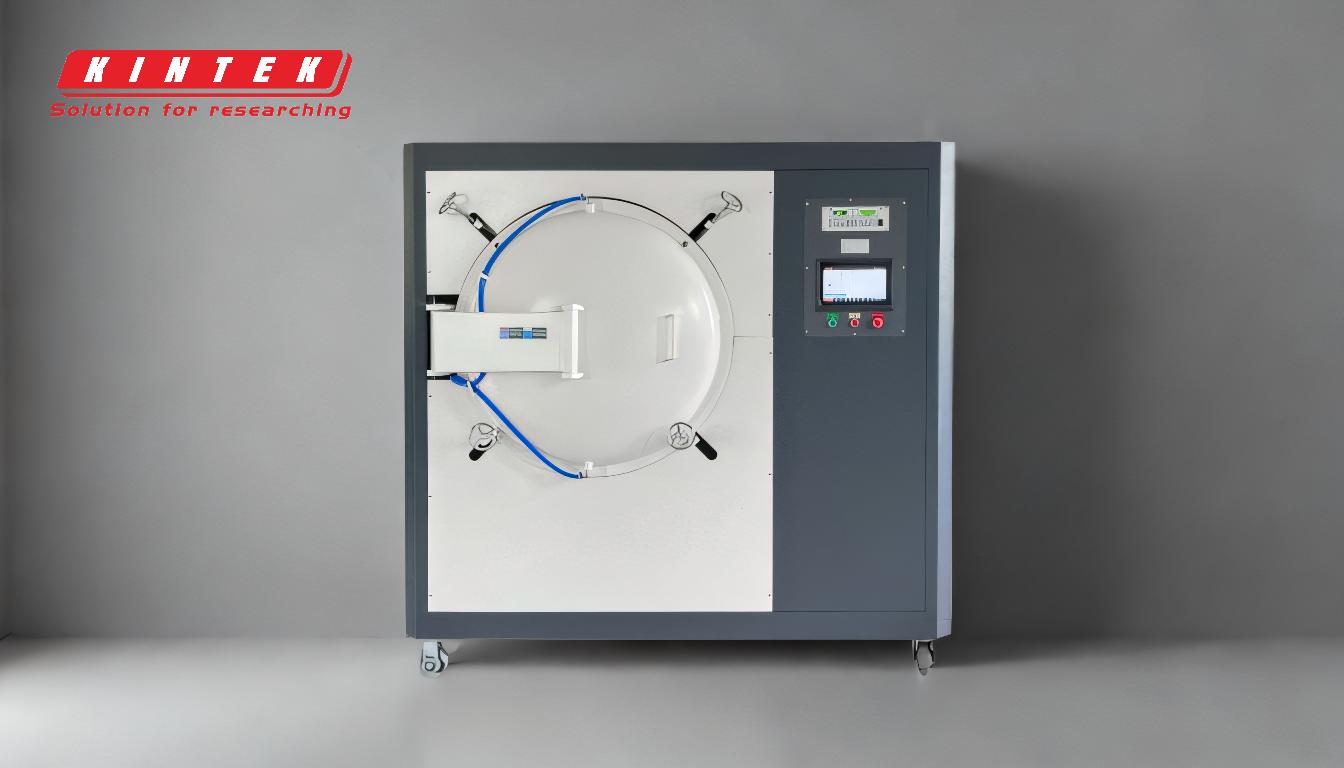
-
Definition and Mechanism:
- Fusion (Melting): Fusion involves heating a material to its melting point, where it transitions from a solid to a liquid state. This process requires significant energy to overcome the material’s latent heat of fusion. Once liquefied, the material can be reshaped or joined with other materials before cooling and solidifying.
- Sintering: Sintering uses heat and pressure to compact and bond particles of a material without reaching its melting point. The particles fuse at their boundaries, forming a solid structure. This process occurs below the material’s melting temperature, making it less energy-intensive.
-
Energy Requirements:
- Fusion: Requires high temperatures to achieve the melting point of the material, which can be energy-intensive, especially for materials with high melting points like metals.
- Sintering: Operates at lower temperatures, as it does not require liquefaction. This makes sintering more energy-efficient and cost-effective for certain applications.
-
Material State During Processing:
- Fusion: The material transitions to a liquid state, allowing for complete homogenization and the formation of strong, continuous bonds.
- Sintering: The material remains in a solid state, with particles bonding at their surfaces. This can result in a porous structure, which may be desirable for specific applications like filters or lightweight components.
-
Applications:
- Fusion: Commonly used in welding, casting, and additive manufacturing (e.g., 3D printing with metal powders). It is ideal for creating dense, homogenous structures with high strength and integrity.
- Sintering: Widely used in powder metallurgy, ceramics, and the production of composite materials. It is suitable for creating complex shapes, porous structures, and components with controlled porosity or thermal properties.
-
Resulting Material Properties:
- Fusion: Produces dense, non-porous materials with high mechanical strength and uniformity. The liquid state allows for the elimination of voids and defects.
- Sintering: Results in materials with varying degrees of porosity, depending on the process parameters. This can be advantageous for applications requiring lightweight materials, thermal insulation, or controlled permeability.
-
Process Control and Complexity:
- Fusion: Requires precise control of temperature and cooling rates to avoid defects like cracks or warping. The process is more complex due to the need to manage the material’s liquid state.
- Sintering: Offers greater control over the final material’s microstructure and porosity. It is less complex in terms of temperature management but requires careful control of pressure and particle size distribution.
-
Material Compatibility:
- Fusion: Suitable for materials that can be melted without degrading, such as metals and some polymers. Not ideal for materials that decompose or oxidize at high temperatures.
- Sintering: Compatible with a wider range of materials, including ceramics, metals, and composites. It is particularly useful for materials that cannot withstand the high temperatures required for fusion.
-
Economic and Environmental Considerations:
- Fusion: Higher energy consumption and costs due to the need for high temperatures. It may also require additional post-processing to address defects.
- Sintering: More economical and environmentally friendly due to lower energy requirements. It also reduces material waste, as it often uses powdered materials that can be precisely measured and shaped.
In summary, while both fusion and sintering are used to join or consolidate materials, they differ fundamentally in their mechanisms, energy requirements, and applications. Fusion is ideal for creating dense, strong structures, while sintering is better suited for producing porous or complex components with controlled properties. Understanding these differences is crucial for selecting the appropriate process based on the desired material properties and application requirements.
Summary Table:
Aspect | Fusion (Melting) | Sintering |
---|---|---|
Definition | Heats material to melting point, turning it into liquid. | Compacts and bonds particles without liquefying the material. |
Energy Requirements | High energy due to melting point temperatures. | Lower energy as it operates below melting point. |
Material State | Liquid state for homogenization. | Solid state with particle bonding at surfaces. |
Applications | Welding, casting, additive manufacturing (e.g., 3D printing). | Powder metallurgy, ceramics, composite materials. |
Material Properties | Dense, non-porous, high strength. | Porous, lightweight, controlled permeability. |
Process Complexity | Requires precise temperature and cooling rate control. | Easier temperature management but needs pressure and particle size control. |
Material Compatibility | Metals, some polymers. Not suitable for materials that degrade at high temperatures. | Ceramics, metals, composites. Ideal for heat-sensitive materials. |
Economic & Environmental | Higher energy costs, potential post-processing. | Lower energy use, reduced waste, cost-effective. |
Need help choosing the right process for your material? Contact our experts today!