Hardening and vacuum hardening are both heat treatment processes used to increase the hardness and durability of metals. However, they differ significantly in their methods, applications, and outcomes. Hardening involves heating the metal to a high temperature and then cooling it rapidly, often in air, oil, or water. Vacuum hardening, on the other hand, takes place in a vacuum environment, which eliminates oxidation and contamination, resulting in a cleaner and more precise hardening process. This method is particularly beneficial for high-performance metals and alloys, as it allows for better control over the hardening process and produces superior results.
Key Points Explained:
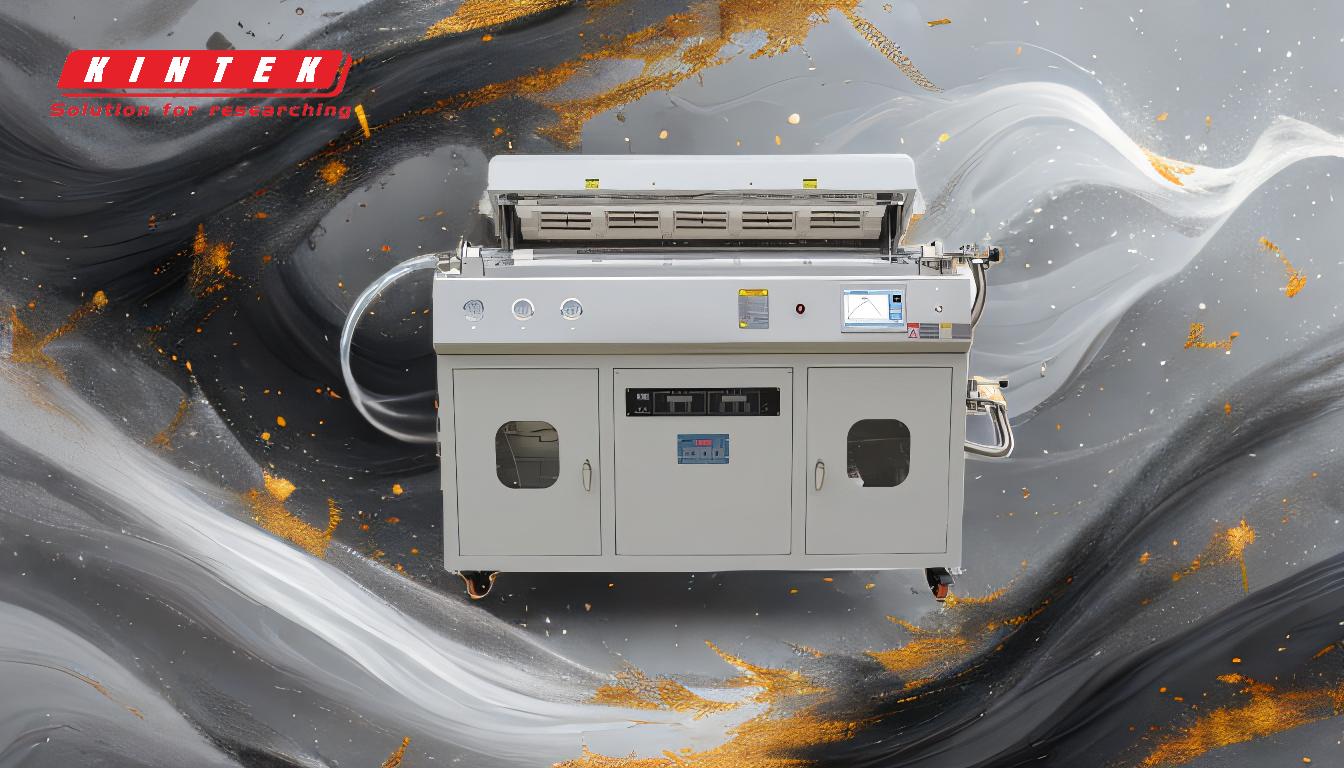
-
Environment and Process Control:
- Hardening: Traditional hardening is performed in an open environment, where the metal is heated and then quenched in a medium like oil or water. This process can lead to oxidation and scaling on the metal surface.
- Vacuum Hardening: This process occurs in a vacuum hardening furnace, where the air is evacuated before heating. This prevents oxidation and contamination, ensuring a cleaner and more controlled hardening process. The absence of oxygen also allows for better heat transfer and more uniform heating.
-
Cost and Complexity:
- Hardening: Generally less expensive and simpler to perform, as it does not require specialized equipment beyond a furnace and quenching medium.
- Vacuum Hardening: More expensive due to the need for a vacuum furnace and associated equipment like a pumping system to evacuate the chamber. The process is also more complex, requiring precise control over temperature and pressure.
-
Material Compatibility:
- Hardening: Suitable for a wide range of metals but may not be ideal for materials that are prone to oxidation or require precise control over the hardening process.
- Vacuum Hardening: Can be used on a broader range of metals, including those that are sensitive to oxidation or require high precision. This method is particularly beneficial for high-performance alloys and tool steels.
-
Outcome and Quality:
- Hardening: Produces a hardened metal with improved strength and wear resistance. However, the presence of oxidation and scaling can affect the surface quality.
- Vacuum Hardening: Results in a harder and more durable metal with a cleaner surface finish. The vacuum environment ensures that the metal is free from oxidation and contamination, leading to superior mechanical properties and longer lifespan.
-
Post-Treatment Processes:
- Hardening: Often followed by tempering to reduce brittleness and improve toughness. Tempering can be done in an open environment, but the risk of oxidation remains.
- Vacuum Hardening: Can also be followed by tempering, but the process can be performed in a controlled environment, further enhancing the quality of the final product. The use of inert gases like Argon for cooling ensures that the metal remains free from contamination during the entire process.
In summary, while both hardening and vacuum hardening aim to increase the hardness and durability of metals, vacuum hardening offers a more controlled and precise process, resulting in superior quality and performance. The choice between the two methods depends on the specific requirements of the application, including the type of metal, desired outcomes, and budget constraints. For high-performance applications where quality and precision are paramount, vacuum hardening is often the preferred method.
Summary Table:
Aspect | Hardening | Vacuum Hardening |
---|---|---|
Environment | Open environment; risk of oxidation and scaling. | Vacuum environment; prevents oxidation and contamination. |
Cost | Less expensive; simpler equipment. | More expensive; requires vacuum furnace and specialized equipment. |
Material Compatibility | Suitable for a wide range of metals. | Ideal for oxidation-sensitive metals and high-performance alloys. |
Outcome | Improved strength and wear resistance; surface oxidation may occur. | Superior hardness, durability, and cleaner surface finish. |
Post-Treatment | Tempering in open environment; risk of oxidation. | Tempering in controlled environment; inert gases ensure contamination-free results. |
Want to learn more about the best hardening process for your metals? Contact our experts today for personalized advice!