Induction melting and vacuum induction melting are both processes that use electromagnetic induction to heat and melt metals, but they differ significantly in their operational environments and outcomes. Induction melting is a general term for melting metals using induction heating in an open or controlled atmosphere, while vacuum induction melting (VIM) specifically involves melting metals under vacuum conditions. The vacuum environment in VIM prevents oxidation and contamination, making it ideal for producing high-purity metals and alloys. Both processes use induction coils to generate eddy currents that heat the metal, but VIM offers additional benefits such as improved material purity, precise alloying, and better control over the melting process.
Key Points Explained:
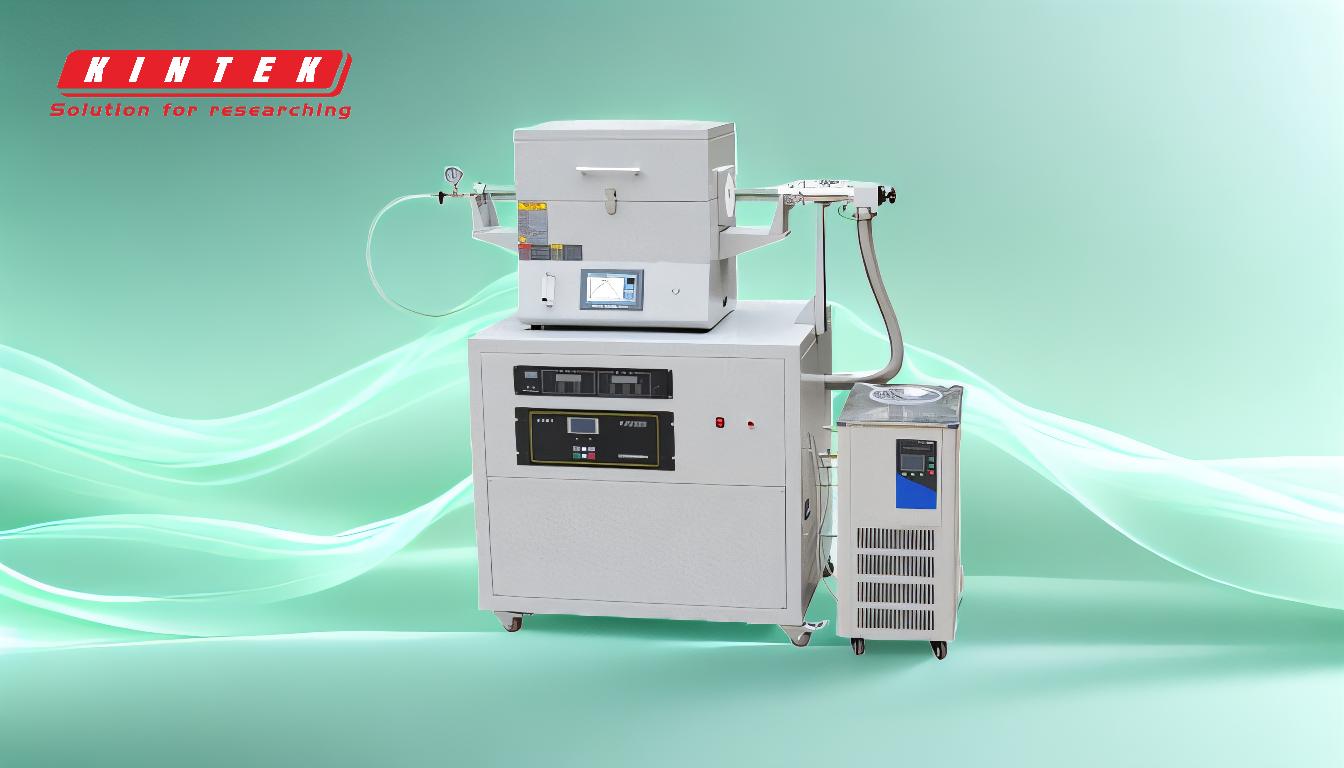
-
Operational Environment:
- Induction Melting: Typically occurs in an open or controlled atmosphere. The environment may include air, inert gases, or other protective atmospheres to prevent oxidation and contamination.
- Vacuum Induction Melting (VIM): Conducted under vacuum conditions, which significantly reduces the presence of oxygen and other reactive gases. This environment is crucial for melting metals that are highly reactive with oxygen and nitrogen.
-
Process Mechanism:
- Induction Melting: Uses an induction coil carrying an alternating current to generate eddy currents within the metal. These eddy currents produce heat due to the metal's electrical resistance, eventually melting the metal.
- Vacuum Induction Melting: Also uses electromagnetic induction to generate eddy currents and heat the metal. However, the vacuum environment ensures that the metal is melted without exposure to atmospheric gases, which can cause impurities and oxidation.
-
Material Purity and Quality:
- Induction Melting: While effective for many applications, the quality of the melted metal can be affected by the surrounding atmosphere, leading to potential impurities and oxidation.
- Vacuum Induction Melting: Produces metals and alloys with higher purity due to the absence of atmospheric gases. The vacuum environment allows for the removal of dissolved gases and impurities, resulting in superior material quality.
-
Applications and Suitability:
- Induction Melting: Suitable for a wide range of metals and alloys, especially those that are less reactive with atmospheric gases. Commonly used in foundries and metalworking industries.
- Vacuum Induction Melting: Ideal for melting reactive metals and alloys, such as titanium, nickel-based superalloys, and other high-performance materials. VIM is often used in aerospace, medical, and high-tech industries where material purity and performance are critical.
-
Advantages:
- Induction Melting: Offers flexibility in terms of atmosphere control, relatively lower equipment costs, and suitability for a broad range of metals.
- Vacuum Induction Melting: Provides superior material purity, precise control over alloy composition, and reduced contamination. VIM is also energy-efficient and environmentally friendly compared to traditional smelting methods.
-
Equipment and Setup:
- Induction Melting: Requires an induction furnace with appropriate refractory linings and, optionally, atmosphere control systems.
- Vacuum Induction Melting: Involves a more complex setup, including an airtight, water-cooled furnace capable of maintaining a vacuum. The furnace is lined with refractories that can withstand high temperatures and vacuum conditions.
-
Economic and Environmental Considerations:
- Induction Melting: Generally more cost-effective for less demanding applications but may require additional measures to control oxidation and impurities.
- Vacuum Induction Melting: While more expensive due to the specialized equipment and vacuum requirements, VIM offers long-term savings through higher material quality, reduced waste, and lower energy consumption.
In summary, while both induction melting and vacuum induction melting utilize electromagnetic induction to melt metals, the key difference lies in the environment in which the melting occurs. VIM's vacuum environment provides significant advantages in terms of material purity, precision, and suitability for high-performance applications, making it the preferred choice for industries requiring the highest quality metals and alloys.
Summary Table:
Aspect | Induction Melting | Vacuum Induction Melting (VIM) |
---|---|---|
Operational Environment | Open or controlled atmosphere (air, inert gases) | Vacuum conditions, reducing oxygen and reactive gases |
Process Mechanism | Electromagnetic induction with eddy currents heating the metal | Electromagnetic induction in a vacuum, preventing oxidation and contamination |
Material Purity | Potential impurities due to atmospheric exposure | Higher purity due to absence of atmospheric gases, ideal for reactive metals |
Applications | Foundries, metalworking industries, less reactive metals | Aerospace, medical, high-tech industries, reactive metals (titanium, nickel-based superalloys) |
Advantages | Flexible atmosphere control, lower equipment costs | Superior material purity, precise alloying, reduced contamination, energy-efficient |
Equipment Setup | Induction furnace with refractory linings, optional atmosphere control | Airtight, water-cooled furnace with vacuum capability, high-temperature refractories |
Economic Considerations | Cost-effective for less demanding applications | Higher initial cost but long-term savings through superior material quality and reduced waste |
Interested in learning more about induction melting or vacuum induction melting? Contact our experts today to find the best solution for your needs!