Liquid carburizing and gas carburizing are two distinct methods of surface hardening used to enhance the wear resistance and durability of steel components. Liquid carburizing involves immersing steel parts in a molten salt bath containing carbon-rich compounds, while gas carburizing uses a carbon-rich gaseous atmosphere to diffuse carbon into the steel surface. Both processes aim to increase the carbon content at the surface, but they differ in their mechanisms, equipment requirements, and process control. Liquid carburizing is often preferred for smaller parts and offers faster heating rates, while gas carburizing is more suitable for larger components and provides better uniformity and process control.
Key Points Explained:
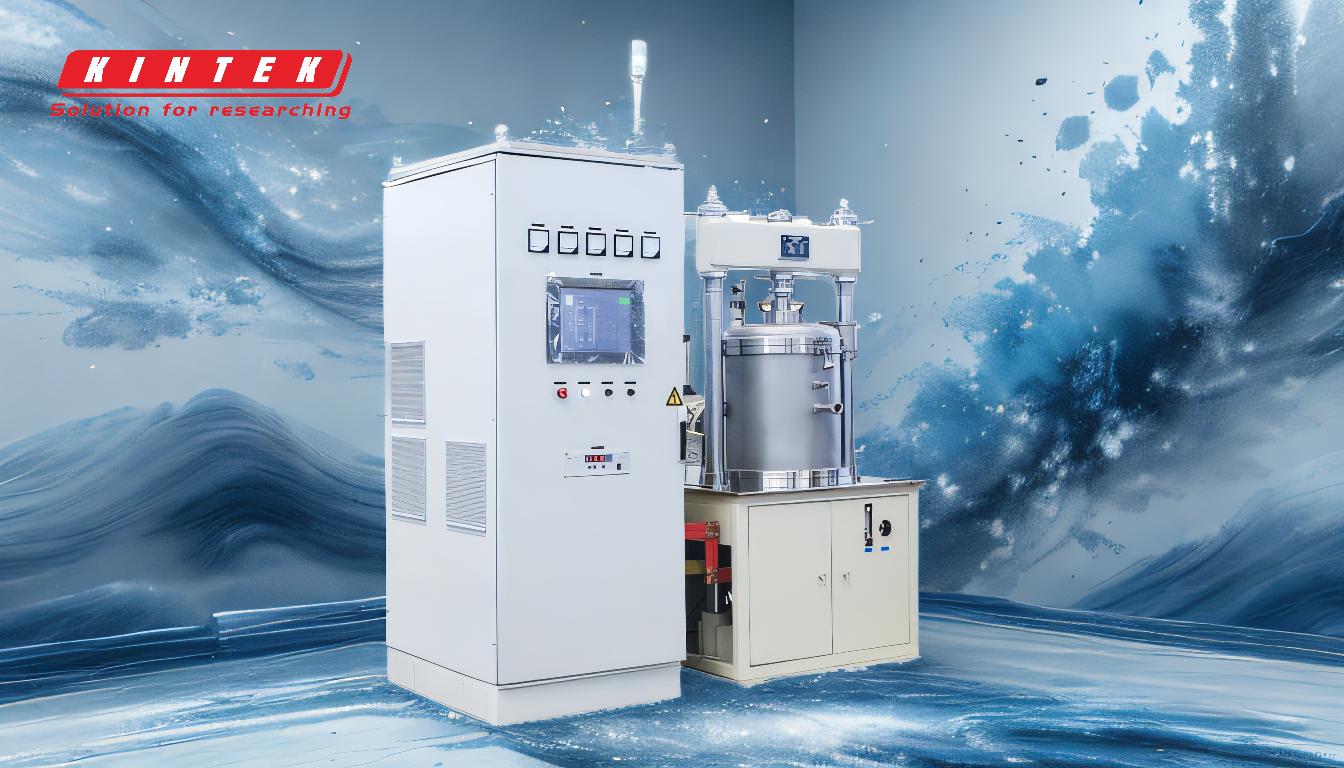
-
Process Mechanism:
- Liquid Carburizing: Steel parts are immersed in a molten salt bath containing carbon-rich compounds such as sodium cyanide or potassium cyanide. The carbon diffuses into the steel surface at high temperatures (typically 850-950°C).
- Gas Carburizing: Steel parts are heated in a furnace with a carbon-rich gas atmosphere, usually composed of methane, propane, or natural gas. The carbon atoms diffuse into the steel surface at temperatures typically between 900-950°C.
-
Equipment and Setup:
- Liquid Carburizing: Requires a salt bath furnace, which is relatively simple and compact. The molten salt must be carefully maintained to ensure consistent carbon content and temperature.
- Gas Carburizing: Requires a more complex furnace setup with gas injection systems and precise atmosphere control. The furnace must be equipped with sensors to monitor and regulate the carbon potential of the gas atmosphere.
-
Process Control and Uniformity:
- Liquid Carburizing: Offers faster heating rates due to the direct contact with the molten salt, but it can be challenging to achieve uniform carbon diffusion, especially for complex geometries.
- Gas Carburizing: Provides better control over the carbon potential and allows for more uniform carbon diffusion across the surface of the parts, even for complex shapes.
-
Application Suitability:
- Liquid Carburizing: Ideal for small to medium-sized parts, such as gears, bearings, and fasteners, where rapid processing is required. It is also suitable for parts that require a thin, hard surface layer.
- Gas Carburizing: More suitable for larger components and mass production, where consistent and uniform surface hardening is critical. It is often used in the automotive and aerospace industries for parts like crankshafts, camshafts, and transmission components.
-
Environmental and Safety Considerations:
- Liquid Carburizing: Involves the use of hazardous chemicals like cyanide, which require careful handling and disposal. The process can also produce toxic fumes, necessitating proper ventilation and safety measures.
- Gas Carburizing: Generally considered safer and more environmentally friendly, as it does not involve toxic chemicals. However, it still requires proper handling of flammable gases and monitoring of furnace emissions.
-
Cost and Maintenance:
- Liquid Carburizing: Lower initial equipment costs but higher ongoing maintenance due to the need for regular salt bath replenishment and disposal. The process may also require more frequent part cleaning to remove salt residues.
- Gas Carburizing: Higher initial investment in furnace equipment and gas control systems, but lower maintenance costs over time. The process is also more energy-efficient, leading to potential cost savings in the long run.
-
Surface Finish and Post-Processing:
- Liquid Carburizing: Typically results in a smoother surface finish due to the polishing effect of the molten salt. However, parts may require additional cleaning to remove any residual salt.
- Gas Carburizing: May produce a slightly rougher surface finish, but this can be mitigated with proper process control. Parts generally require less post-processing compared to liquid carburizing.
In summary, the choice between liquid and gas carburizing depends on the specific requirements of the application, including part size, production volume, desired surface properties, and environmental considerations. Both methods offer unique advantages and challenges, making them suitable for different industrial needs.
Summary Table:
Aspect | Liquid Carburizing | Gas Carburizing |
---|---|---|
Process Mechanism | Immersion in molten salt bath (850-950°C) | Heating in carbon-rich gas atmosphere (900-950°C) |
Equipment | Salt bath furnace (simple, compact) | Complex furnace with gas injection and atmosphere control |
Process Control | Faster heating, less uniform diffusion | Better control, more uniform diffusion |
Application Suitability | Small to medium parts (gears, bearings) | Larger components, mass production (automotive, aerospace) |
Environmental Impact | Hazardous chemicals (cyanide), toxic fumes | Safer, no toxic chemicals, but flammable gases |
Cost & Maintenance | Lower initial cost, higher maintenance (salt replenishment, cleaning) | Higher initial cost, lower maintenance, energy-efficient |
Surface Finish | Smoother finish, but requires cleaning | Slightly rougher, less post-processing |
Need help deciding between liquid and gas carburizing for your application? Contact our experts today for tailored advice!