LPCVD (Low-Pressure Chemical Vapor Deposition) and PECVD (Plasma-Enhanced Chemical Vapor Deposition) are both techniques used for thin-film deposition, but they differ significantly in terms of temperature, deposition rate, substrate requirements, and the mechanisms driving the deposition process. LPCVD operates at higher temperatures, typically between 600°C to 800°C, and does not require a silicon substrate. In contrast, PECVD utilizes plasma to enhance the deposition process, allowing it to operate at much lower temperatures (room temperature to 350°C) and making it suitable for temperature-sensitive substrates. PECVD also offers faster deposition rates, better edge coverage, and more uniform films, making it ideal for high-quality applications.
Key Points Explained:
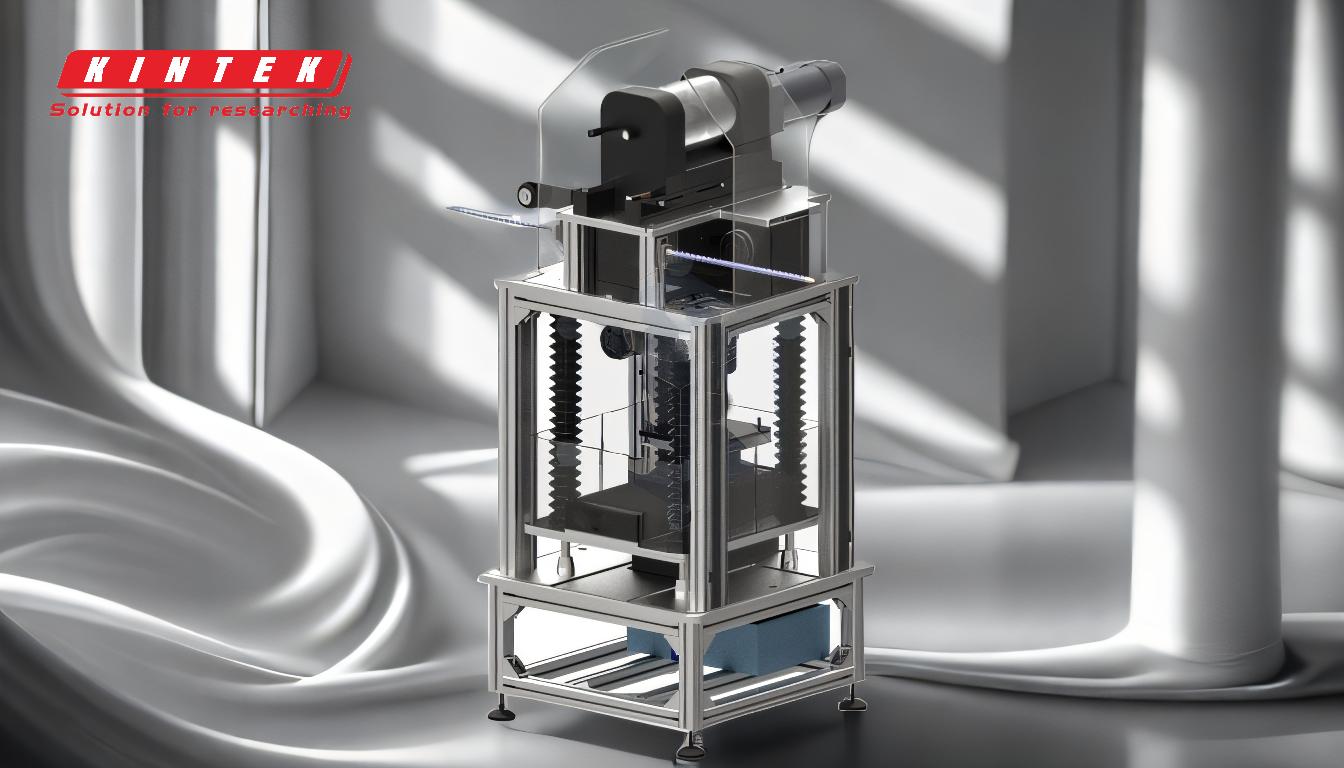
-
Temperature Differences:
- LPCVD: Operates at high temperatures, typically between 600°C to 800°C. This high-temperature environment is necessary to drive the chemical reactions for thin-film deposition.
- PECVD: Utilizes plasma to provide the activation energy needed for the deposition process, allowing it to operate at much lower temperatures, ranging from room temperature to 350°C. This makes PECVD suitable for substrates that are sensitive to high temperatures.
-
Deposition Rate:
- LPCVD: Generally has a slower deposition rate compared to PECVD due to the reliance on thermal energy alone to drive the chemical reactions.
- PECVD: Offers faster deposition rates because the plasma enhances the chemical reactions, leading to quicker film growth.
-
Substrate Requirements:
- LPCVD: Does not require a silicon substrate, making it more versatile in terms of the types of materials it can deposit on.
- PECVD: Typically uses a tungsten-based substrate, which is more specialized and may limit the types of materials that can be coated.
-
Mechanism of Deposition:
- LPCVD: Relies solely on thermal energy to drive the chemical reactions for thin-film deposition. The gas or vapor mixture is introduced into a vacuum chamber and heated to high temperatures to initiate the deposition process.
- PECVD: Uses plasma to enhance the deposition process. The high-energy electrons in the plasma provide the activation energy needed for the chemical reactions, allowing the process to occur at lower temperatures and with greater control over film properties.
-
Film Quality and Uniformity:
- LPCVD: Produces high-quality films but may have limitations in terms of edge coverage and uniformity due to the reliance on thermal energy alone.
- PECVD: Offers better edge coverage and more uniform films due to the enhanced control provided by the plasma. This makes PECVD more reproducible and suitable for high-quality applications.
-
Applications:
- LPCVD: Commonly used in semiconductor and optical coating manufacturing where high-temperature processes are acceptable.
- PECVD: Ideal for applications requiring low-temperature deposition, such as coating temperature-sensitive substrates or producing high-quality, uniform films for advanced semiconductor devices.
In summary, the choice between LPCVD and PECVD depends on the specific requirements of the application, including the desired film properties, substrate material, and temperature constraints. LPCVD is suitable for high-temperature processes and a wide range of substrates, while PECVD offers advantages in low-temperature deposition, faster rates, and superior film quality.
Summary Table:
Aspect | LPCVD | PECVD |
---|---|---|
Temperature | 600°C to 800°C | Room temperature to 350°C |
Deposition Rate | Slower, relies on thermal energy | Faster, enhanced by plasma activation |
Substrate Requirements | No silicon substrate required, versatile | Typically uses tungsten-based substrate, more specialized |
Mechanism | Thermal energy-driven chemical reactions | Plasma-enhanced chemical reactions |
Film Quality | High-quality but limited edge coverage and uniformity | Superior edge coverage, uniform, and reproducible films |
Applications | Semiconductor and optical coating manufacturing | Low-temperature deposition for sensitive substrates, advanced devices |
Need help choosing between LPCVD and PECVD for your application? Contact our experts today for tailored advice!