Plasma-Enhanced Chemical Vapor Deposition (PECVD) and Atmospheric Pressure Chemical Vapor Deposition (APCVD) are both variants of Chemical Vapor Deposition (CVD) used to deposit thin films on substrates. The primary difference lies in the operating conditions and the mechanisms used to activate the chemical reactions. PECVD utilizes plasma to enable deposition at lower temperatures, making it suitable for temperature-sensitive substrates, while APCVD operates at atmospheric pressure and typically requires higher temperatures. Both methods have unique advantages and limitations, making them suitable for different applications in material science and thin-film fabrication.
Key Points Explained:
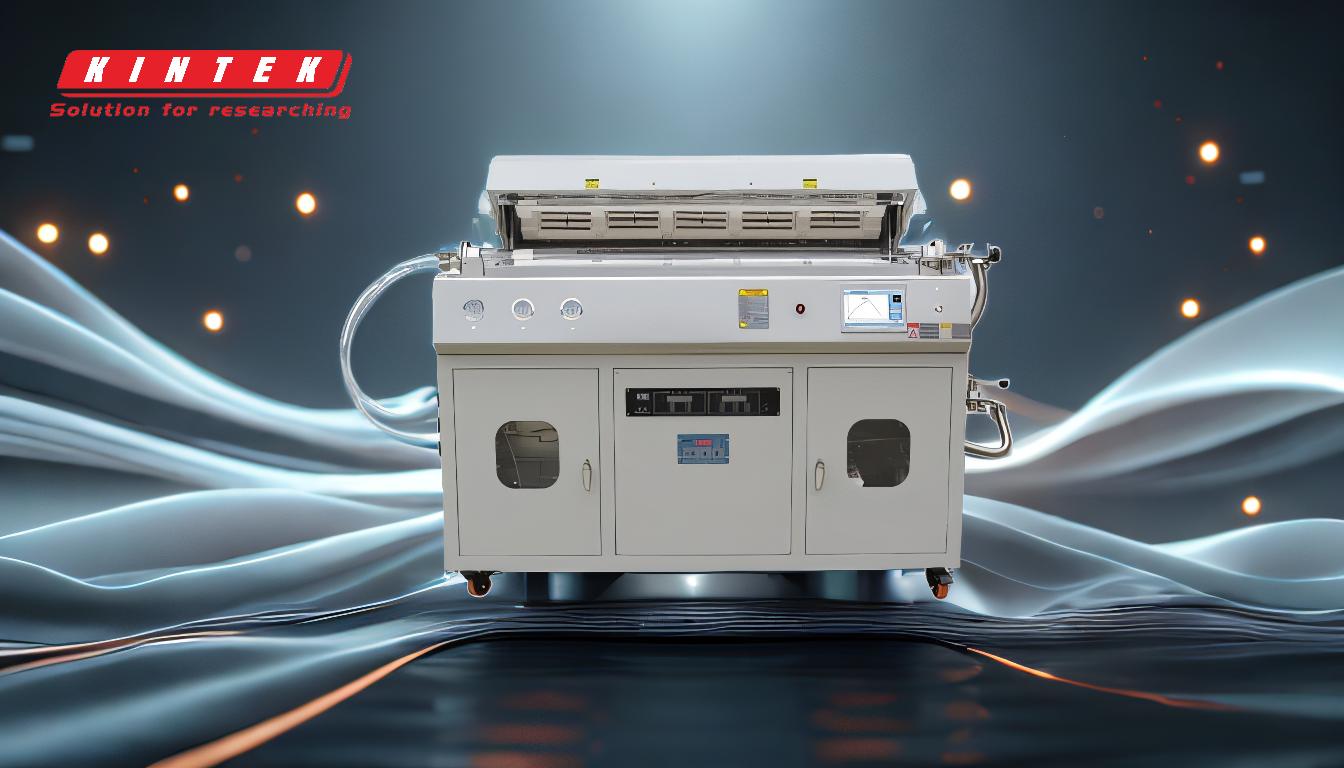
-
Operating Conditions:
- PECVD: Operates at lower temperatures due to the use of plasma, which provides the necessary activation energy for chemical reactions. This makes it ideal for temperature-sensitive materials.
- APCVD: Operates at atmospheric pressure and generally requires higher temperatures, which can limit its use with certain substrates.
-
Mechanism of Deposition:
- PECVD: Uses plasma to ionize gas molecules, creating reactive species that facilitate the deposition process. This allows for precise control over film properties and uniformity.
- APCVD: Relies on thermal energy to drive chemical reactions, which can result in less control over film properties compared to PECVD.
-
Applications:
- PECVD: Commonly used in the semiconductor industry for depositing dielectric layers, passivation layers, and other thin films on temperature-sensitive substrates.
- APCVD: Often used for depositing thicker films and coatings on larger substrates, such as in the production of solar panels and optical coatings.
-
Advantages:
- PECVD: Lower temperature operation, better film uniformity, and the ability to deposit high-quality films on complex geometries.
- APCVD: Simpler equipment setup, ability to handle larger substrates, and potentially lower operational costs due to the absence of vacuum systems.
-
Disadvantages:
- PECVD: Higher equipment and operational costs, complexity in controlling plasma parameters, and potential for plasma-induced damage to sensitive substrates.
- APCVD: Limited to higher temperature processes, less control over film properties, and potential for contamination due to the open atmospheric environment.
-
Health and Safety:
- PECVD: Requires careful handling of hazardous gases and plasma, necessitating stringent safety protocols.
- APCVD: Also involves the use of hazardous chemicals, but the risks may be somewhat mitigated by the absence of vacuum systems.
In summary, the choice between PECVD and APCVD depends on the specific requirements of the application, including substrate sensitivity, desired film properties, and production scale. Each method has its own set of advantages and limitations, making them complementary rather than directly comparable.
Summary Table:
Aspect | PECVD | APCVD |
---|---|---|
Operating Conditions | Lower temperatures, plasma activation | Atmospheric pressure, higher temperatures |
Mechanism | Plasma ionizes gas molecules for precise control | Thermal energy drives chemical reactions |
Applications | Semiconductor industry, temperature-sensitive substrates | Solar panels, optical coatings, larger substrates |
Advantages | Lower temperature, better uniformity, complex geometries | Simpler setup, larger substrates, lower operational costs |
Disadvantages | Higher costs, complex plasma control, potential substrate damage | Higher temperatures, less control, potential contamination |
Health & Safety | Requires stringent safety protocols for hazardous gases and plasma | Hazardous chemicals, mitigated risks due to no vacuum systems |
Need help choosing between PECVD and APCVD for your application? Contact our experts today for tailored advice!